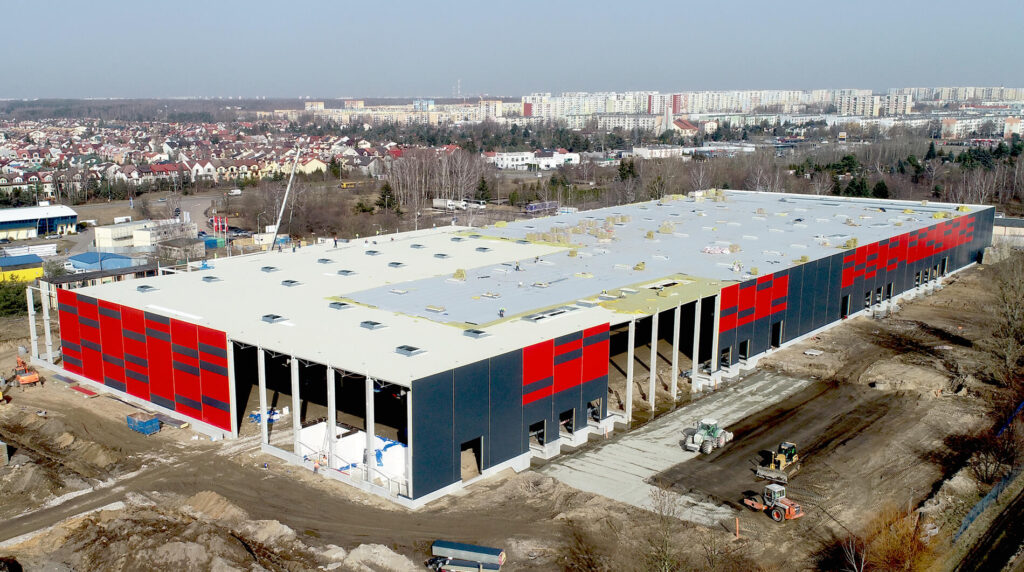
A steel roof is a key part of the building. Typically, the roof structure of a hall consists of the main load-bearing components such as girders and purlins, each having a different function.
Individual structural components have various roles. The hall roof must protect the interior from the outside conditions, while ensuring the highest tightness and insulation standards. Moreover, the local weather effects, dead load as well as any additional process loads (e.g. systems suspended under or affixed to the roof) must also be considered in the roof design. A modern sheet metal roof structures efficiently combine safety and functional aspects with a presentable appearance. Since the construction materials are available in a wide range of colours, you can easily and conveniently arrange the space and match your warehouse or production hall to any other buildings on the premises.
Steel structure roof
These days, steel structure roofs can be designed in a variety of ways. For large-area buildings, steel roof structures ensure safety through the use of supporting force. The physical forces and weights of the roof covering of a steel hall are distributed evenly over the load-bearing components and the external walls.
The most common system is a purlin roof with the supporting beams (purlins) arranged parallel to the eaves. The beams are positioned according to the roof slope. The purlins can be made from various materials, depending on the span of the building, the spacing of adjacent frames and the loads involved. Common types of steel structure roofs use purlins made with:
- hot-rolled sections,
- cold-formed sections,
- openwork or lattice sections.
The current approach to the structure and materials of steel hall roofing includes a number of solutions for a perfect finish of the building. Some of the common solutions include corrugated sheet metal, sandwich panels and sheet metal panels that can be combined with insulating materials.
Roof construction
There are a number of methods for roof construction and types of steel structures. An uninsulated steel roof is the most basic solution. It works for facilities which do not require maintaining high temperatures inside. This solution is most often based on trapezoidal metal sheets fixed directly to the roof purlins. Properly made sheet joints are also waterproof. Constructing a trapezoidal sheet metal roof requires careful and accurate installation of the metal sheets on the supporting components using mechanical fasteners which must be carefully selected, as they seriously affect the load-bearing capacity and rigidity of the roof structure. The following can be used depending on the design:
- sheet metal screws,
- self-tapping screws,
- self-drilling and self-tapping screws,
- blind rivets.
Steel structure of a roof covered with trapezoidal metal sheet is typically insulated with mineral wool placed directly on the sheet. Steel roofing of trapezoidal sheets is fastened to the purlins with standing fasteners which remain concealed in the sheet folds. Another group is that of sandwich panels. In this case, the core (insulating material) is permanently fixed to the inner and outer layers of the steel cladding, while the panel is attached to the structure with fasteners.
Roof structure
Steel roof structure must be carefully chosen at an early design stage. This vitally important parameter will largely depend on the adopted design approach.
The structure of a steel hall roof depends among other things on the bay span. The individual building parameters require slightly different technology:
- For a span of <20 m, one economically viable solution would be to use solid-web spandrel beams made with IPE, HEB or HEA type hot-rolled I-sections. These sections are 40-50 cm high,
- For a bay span of 20-26 m, the best solution would be to use spandrel beams in the form of welded plate girders, 50-80 cm high; spandrel beams are also recommended when the span is shorter, but there are significant loads involved.
Where the main column spacing of the hall is >25 m, trusses are used as load-bearing components. The truss height is approx. 1/10–1/12 of the hall span. In this case, roof purlins are a secondary load-bearing elements. They should be fastened directly to the main spandrel beams, making the steel roof structure strong and stable. Their height depends on the span of the main building frames. For an efficient steel roof structure, 20-30 cm high lightweight purlins made with cold-formed elements (e.g. channel sections, Z-bars, sigma and omega sections), as well as delicate lattice purlins, are often used.
The steel roof structure is also affected by its cladding which forms the top section. It shoThe steel roof structure is also affected by its cladding which forms the top section. It should be suitable for a given structure and the type of industrial hall roofing. Most commonly used are trapezoidal sheets, available in three generations:
- first generation trapezoidal sheets, with height not exceeding 70 mm,
- second generation, up to 160 mm high,
- third generation, up to 210 mm high.
The thickness of a hall roof structure may vary greatly. These parameters depend mainly on the solutions adopted at the basic design stage. The steel roof structure of a typical warehouse is approx. 700-900 mm high, but the final dimensions are affected by a number of various factors.
Why Commercecon?
As an expert in the design and construction of steel roofs, we offer custom-made solutions with great attention to every structural and process detail, providing superior quality and comprehensive services:
- We design steel hall cladding with the load-bearing capacity, tightness and insulation performance in the focus of attention.
- We design steel roof structures with the most optimum weight vs. load-bearing capacity vs. rigidity relationship.
- We choose eco-friendly solutions with as little heat loss as possible in the design of steel frame roofs.
- The steel hall roofing we use adds to its aesthetic value.
Let our expertise work for you.