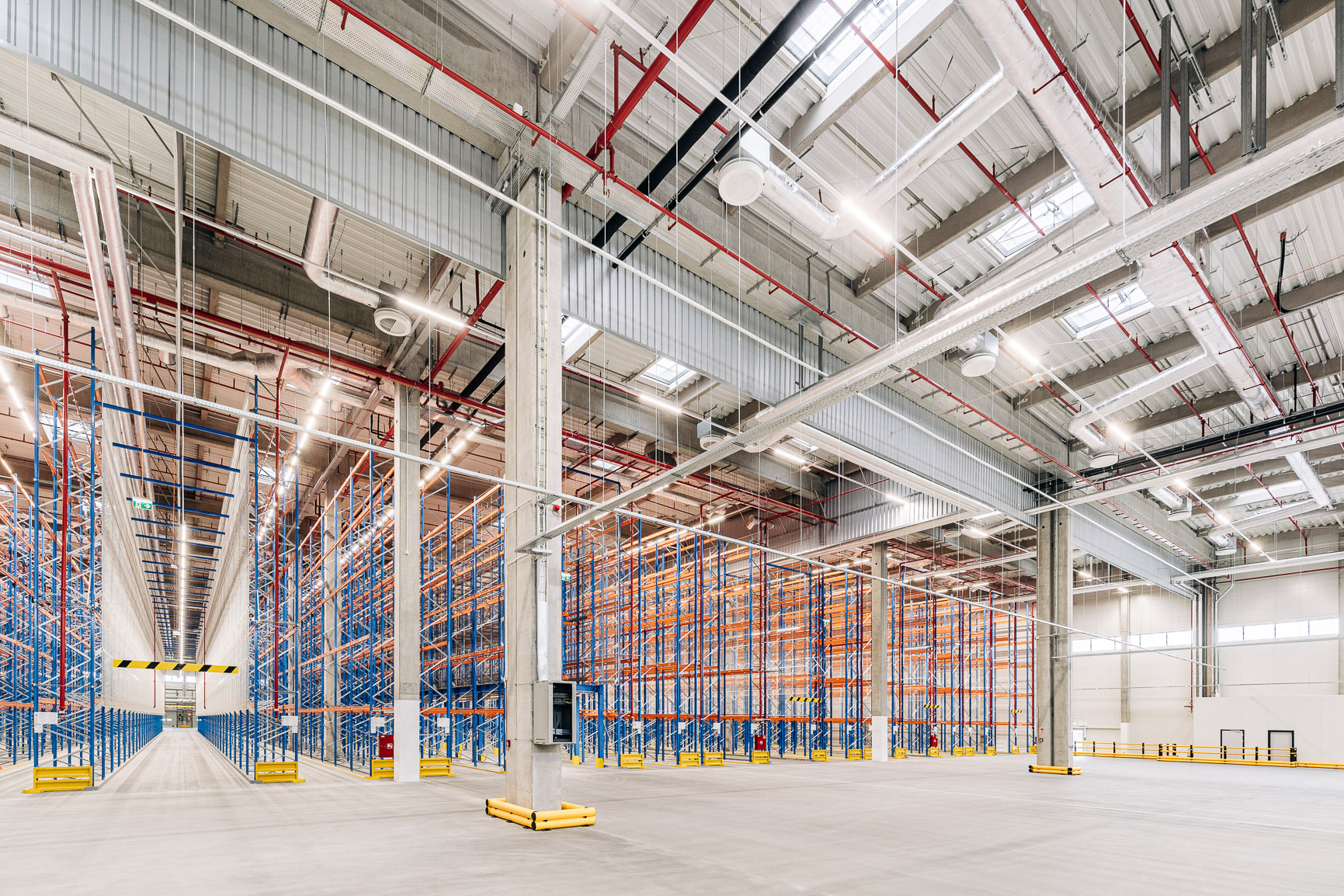
Warehouse space in Poland and Central Europe has experienced significant expansion over the last few years. The arrangement and management of a warehouse’s usable space is a key aspect in determining its effective operation. This poses an extremely important and complex decision-making problem for the investor and the management of a storage facility. The layout of the racks in a warehouse and the choice of a suitable racking system is thus a very important factor that ultimately influences the operational efficiency of the facility.
In order to make efficient use of the entire volume of the warehouse, the goods items are stored in a multi-level arrangement (not only on the floor) using racking systems of various types. A warehouse facility using a multi-storey scheme for the storage of goods is commonly referred to as a high-bay warehouse. Properly selected and designed racking systems in high-bay warehouses are precisely the key to efficient, safe and thus economical use of the facility. Rack systems in warehouse halls are selected according to a number of criteria, one of the most important of which is the type of goods stored and how they are stored. In the following subsections, the different types of rack systems as well as the criteria for choice are explained.
Goods and how they are stored
One of the key aspects of selecting rack storage equipment is knowing what type of goods to store. Identifying the essential characteristics of the stored goods will certainly help in selecting the right rack system. An outstanding issue is the size and weight of the stored units and how they are packed. The shelf life and permissible storage time of the stored goods is naturally also an important aspect. Another important factor is the information on the type of materials stored, if only for the information on the fire load of the rack hall, which is often correlated with the adaptation of the system for protecting the stored goods and the building as a whole against the spread of fire. This is because it has an impact on the choice of a rack system due to the possibility of installing, among other things, sprinkler systems in the racks.
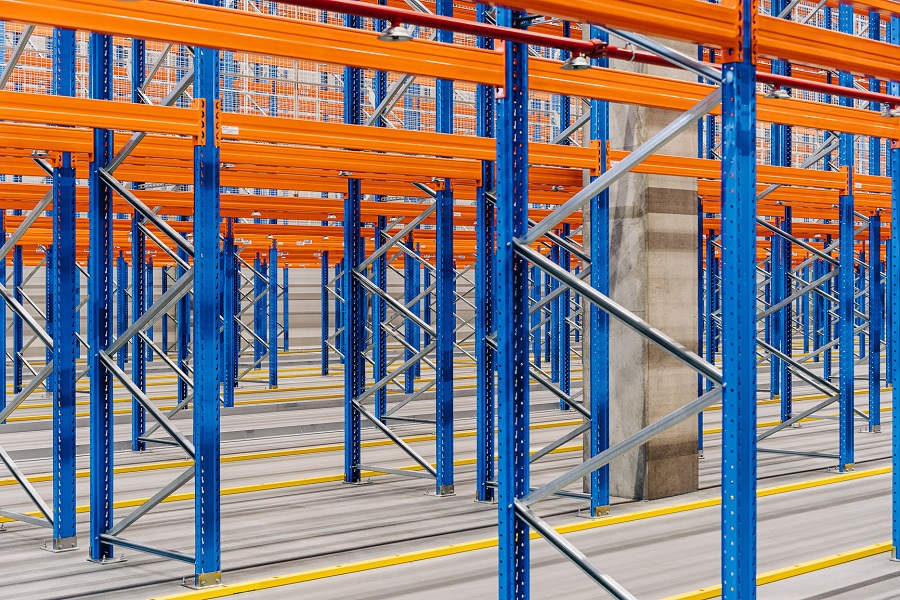
Types of rack systems
The most common storage system for goods stored on pallets (pallet load units) is the fixed frame rack system. Frame racks have simple design that ensures access to all stored items. Due to the simplicity of this system, it has a relatively low price compared to competing solutions. However, fixed frame racks require fully drive-through aisles with adequate handling widths, which in turn results in a fairly low utilisation of storage space.
An alternative to the fixed frame system is track mobile rack systems. At the base, these racks are equipped with mobile units that allow them to be moved along a specially prepared track. The operation of rack movements in such an arrangement can be manual or assisted/mechanical. The track system makes it possible to eliminate unused space only one service corridor is required to operate this type of system. In the case of track mobile racks, it is possible to adapt the type of handling of the system as required. The track mobile racks in the forced-drive variant provide automated handling and maximum utilisation of storage space, but restrict access to the stored units according to the First In – First Out (FIFO) principle, which means that the first load unit placed in the racking system will leave it as first. Alternatively, in the partially-driven variant, access to the goods is possible and handling takes place according to the Last In – First Out (LIFO) principle, where the last load unit placed in the rack system will leave it first. The track mobile rack system is also available in a manually operated variant providing access to all load units.
Another type of storage system is flow storage racking which allows storage according to the First In – First Out principle. They allow the storage of load units stored on wooden, metal and plastic pallets. They come in automated and manual variants. The manual handling variant of the system additionally allows the storage of goods stored in cardboard boxes and plastic containers (palletless).
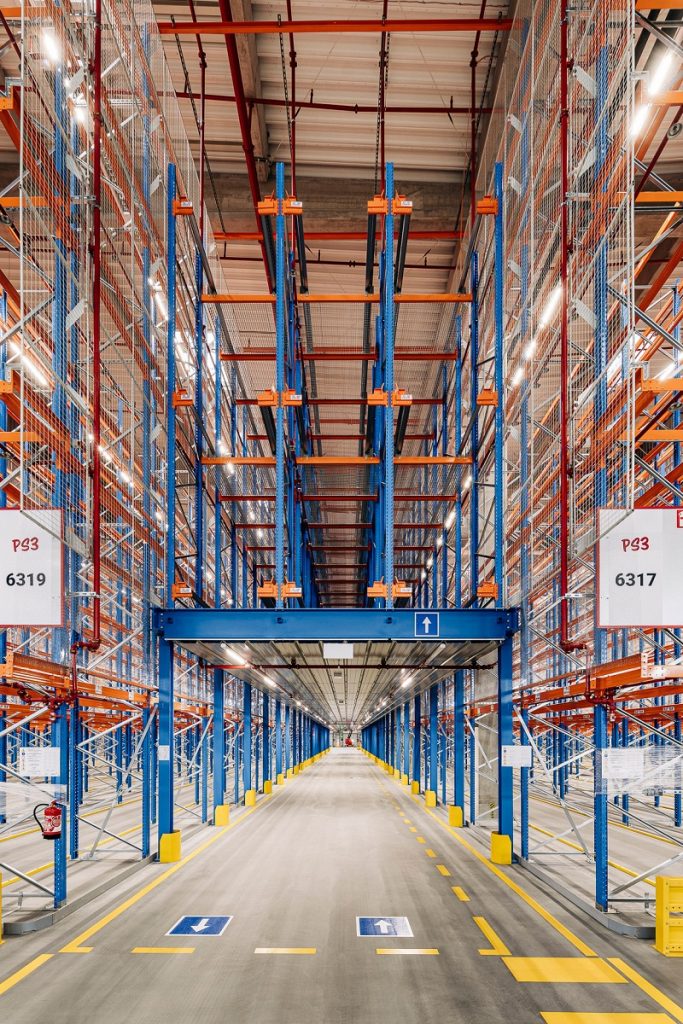
An attractive alternative to the solutions presented is the construction of a rack hall in a self-supporting warehouse variant. The racks of a self-supporting warehouse constitute both the storage structure for storing the load units and the primary load-bearing structure of the facility, allowing the wall cladding and roofing to be installed without erecting an independent structure for the facility. In addition to their own weight and the weight of the stored goods, theself-supporting warehouse racking carries the weight of the hall cladding and all external influences such as snow on the roof or the effects of wind on the building. This solution allows full automation of the storage scheme and is currently the most advanced approach.
What type of racks for a high-bay hall?
The racking warehouse should be equipped with a system that allows the facility to be used as economically as possible. The choice of rack system in a high-bay warehouse is therefore dependent on the particular situation. In order to adapt a racking system to your project you should, among other things, take into account the cost of purchasing the racking system, of operating it , the development of the area around the warehouse (delivery and dispatch of goods) and consider whether future expansion of the warehouse is possible.
When it comes to choosing the optimum method for storing goods, it is advisable to turn to a general contractor with a portfolio of numerous warehousing projects completed under the design and build formula, who can advise you on this highly complex issue.