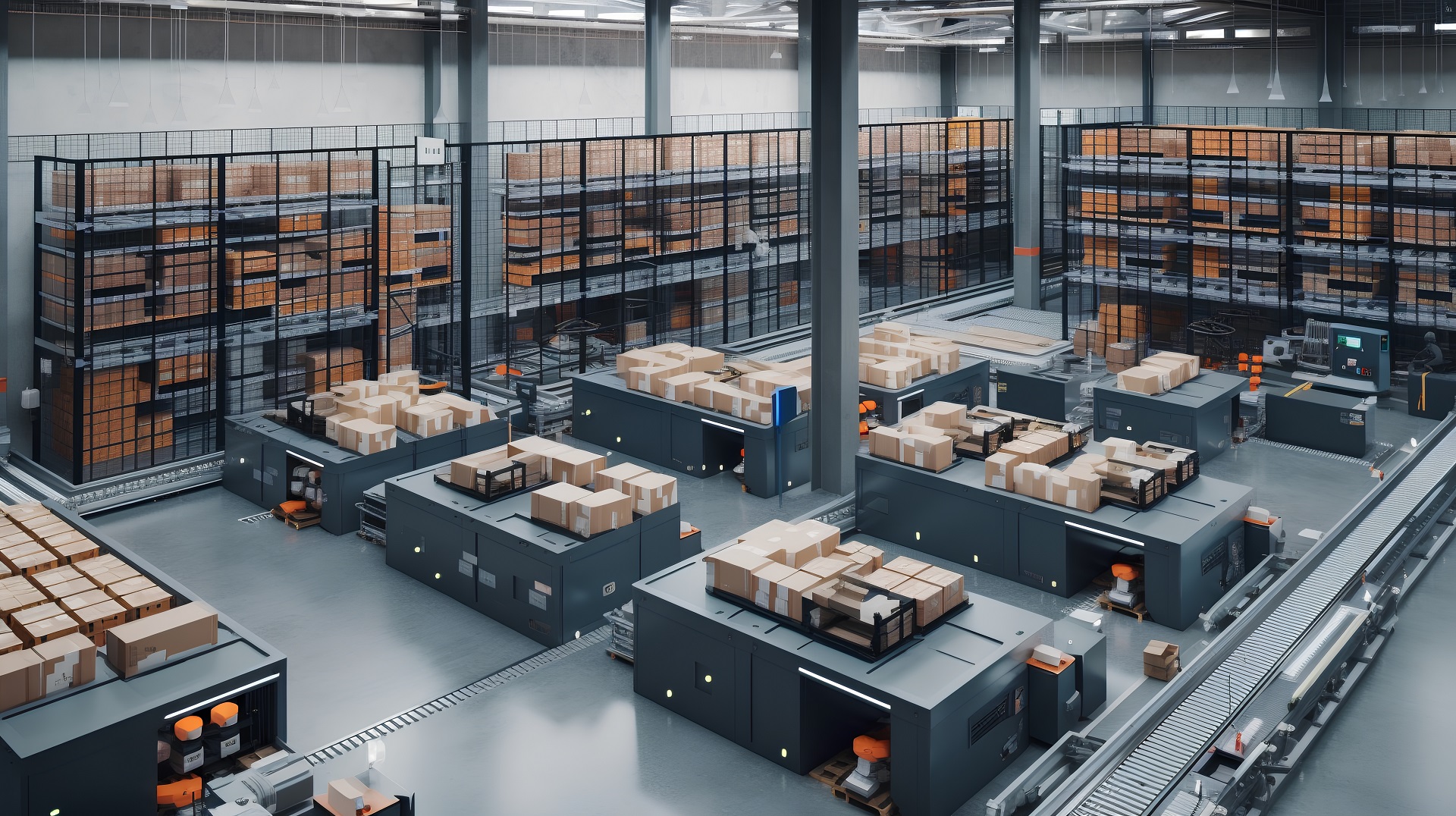
The e-commerce industry in Poland has been growing steadily for several years. The driving force behind this dynamic growth has been a pandemic – the closure of bricks-and-mortar stores and the shift to remote working have greatly changed the shopping preferences of Poles, with many transactions being shifted to the internet. The result of these changes has been a rapidly growing interest in warehouse space from logistics operators and large companies specialising in e-commerce. It was therefore only a matter of time before developers active in the warehousing market became more active in order to provide customers with fit-for-purpose space. Modern storage halls have become the answer to the sudden market demand.
Development of the e-commerce market in Poland
Although the high growth rate of the warehouse market in Poland was predicted by analysts long before the global pandemic, it should not be forgotten that it is the coronavirus restrictions that have contributed most to its dynamic growth. Note, however, that the trend had already been growing since 2012 and was due, among other things, to the leap year-on-year growth of the e-commerce industry, accompanied by an increasing interest in storage space for the storage of a very wide range of products. After all, behind one of the successes of the growing interest in on-line shopping, e.g. for clothing, is a far greater choice of products, as well as size availability, than in regular shops. The pandemic has passed, and the new shopping habits have stayed with us. Therefore, further growth of the industry is almost certain, just as it is certain that new shop halls, i.e. facilities built for the e-commerce industry, will be created. What are they specific for?
Warehouses and the e-commerce market
The term “warehouse halls” is broad. This is to mean both, steel halls built next to production facilities for the storage of components or finished products, but warehouse halls are also cross-dock warehouses, equipped with a large number of gates (docks). This is a warehousing model specific to large e-commerce companies that bypasses the process associated with long-term storage of goods – they arrive at the warehouse, whereupon they are almost immediately unloaded, assembled according to customer orders and then dispatched to their final destination. This method of distributing goods is also referred to as picking handling. This diversity means that the construction of industrial halls for the warehousing market requires general contractors to have both experience and a very good knowledge of building materials and hall technical equipment solutions.
Warehouse halls – rent or build your own?
One of the goals of every entrepreneur is to grow the company and attract new customers. And the growth of a commercial company usually involves the need for new storage space. Then, the owner is faced with a dilemma whether to build a hall or rent the space needed? There is no clear answer to this question, as each solution has both advantages and drawbacks. Renting the space – especially when demand exceeds supply – is hardly economically viable. On the other hand, however, it offers flexibility in operation and the possibility of adapting the area to the current needs.
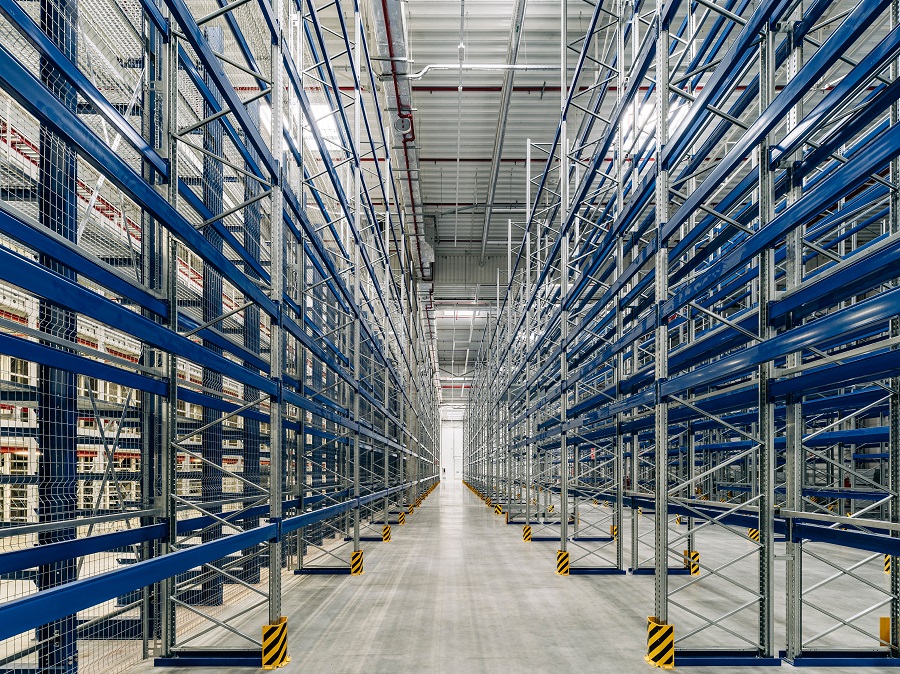
Building your own warehouse, on the other hand, is a huge investment, so the decision must be very carefully considered. In this case, however, you will not be paying rent for years to come, the rates of which have risen rapidly in recent times. What is more, you can design the space in such a way that a selected part of it can be used for rent and make a profit. If you decide to go ahead with such a development, how do you start the investment process?
Building a steel hall for e-commerce – what to look out for?
General Contractor. The construction of industrial halls is a complex and lengthy process every potential investor must be aware of. It requires not only extensive knowledge of the design and construction area, but also a huge time commitment. This is why investors are increasingly willing to entrust these tasks to general contractors, who will handle the investment process comprehensively (both, when it comes to preparing the necessary documentation, and the construction itself) and take full responsibility for its various stages.
Location. When planning to invest in the construction of an e-commerce warehouse hall, it is important to analyse its location very carefully. Why is it important? Firstly, it is about delivery time. The rapid growth of e-commerce means that the desired lead time, i.e. the delivery time to the buyer, is constantly reducing. The same day delivery is becoming more and more common, so the location of shop halls close to the centres of large cities, but also a developed road network, are almost a necessity. But location is also important in terms of labour availability. And although warehouses are becoming more and more modern, packed with innovative technology, there are still many logistics operations, such as handling returns or creating promotional kits, that cannot be automated and will require the involvement of employees. It is important to note that e-commerce is highly seasonal, and, during sales peaks, such as holidays or seasonal sales in the clothing industry, periodic access to human resources is the key issue. Only large urban centres will be able to meet these demands.
Technology. Automation in the warehouse for the e-commerce industry seems to be the standard. Very fast-growing order volumes and the increasing share of on-line sales in retail are forcing technology equipment suppliers to look for new, more efficient solutions. They allow picking times to be reduced and mistakes to be avoided, but they also help to deal with many of the industry’s challenges, such as in the area of manpower, fluctuations in sales volumes and time pressure. And although modern solutions involve extensive investment, you cannot give them up if you want to remain competitive in the market.
Disrupted industrial supply chains
However, when talking about the growing demand for warehousing halls, one should not forget the industrial sector, which has also contributed to the upward trend. How? Disrupted in the pandemic, the supply chains of components and sub-assemblies – manufactured in Asia and used in European industrial plants in the automotive, electronics or white goods sectors – halted production lines on our continent, including Poland, for months. This generated huge cost, so entrepreneurs began to look for solutions that could help them protect themselves from such problems in the future.
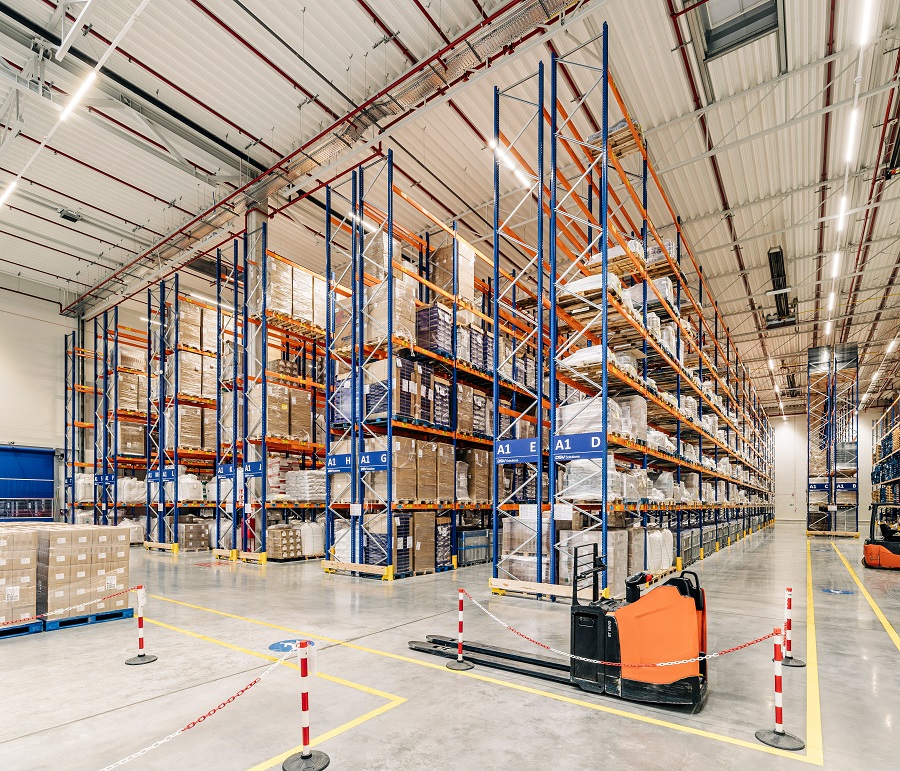
For this, however, a change of concept in the approach to doing business was needed. Some investors have opted to build new manufacturing plants closer to their markets, which are supplied with components by suppliers located close by. Others, on the other hand, have opted to increase their existing storage space, thus being able to store much larger quantities of production components, which would keep production running for longer in an emergency. And so, they changed their ‘just in time’ stock management strategy to stockpiling just in case, or ‘just in case’. However, both solutions have had the same effect – greater demand for new industrial halls.