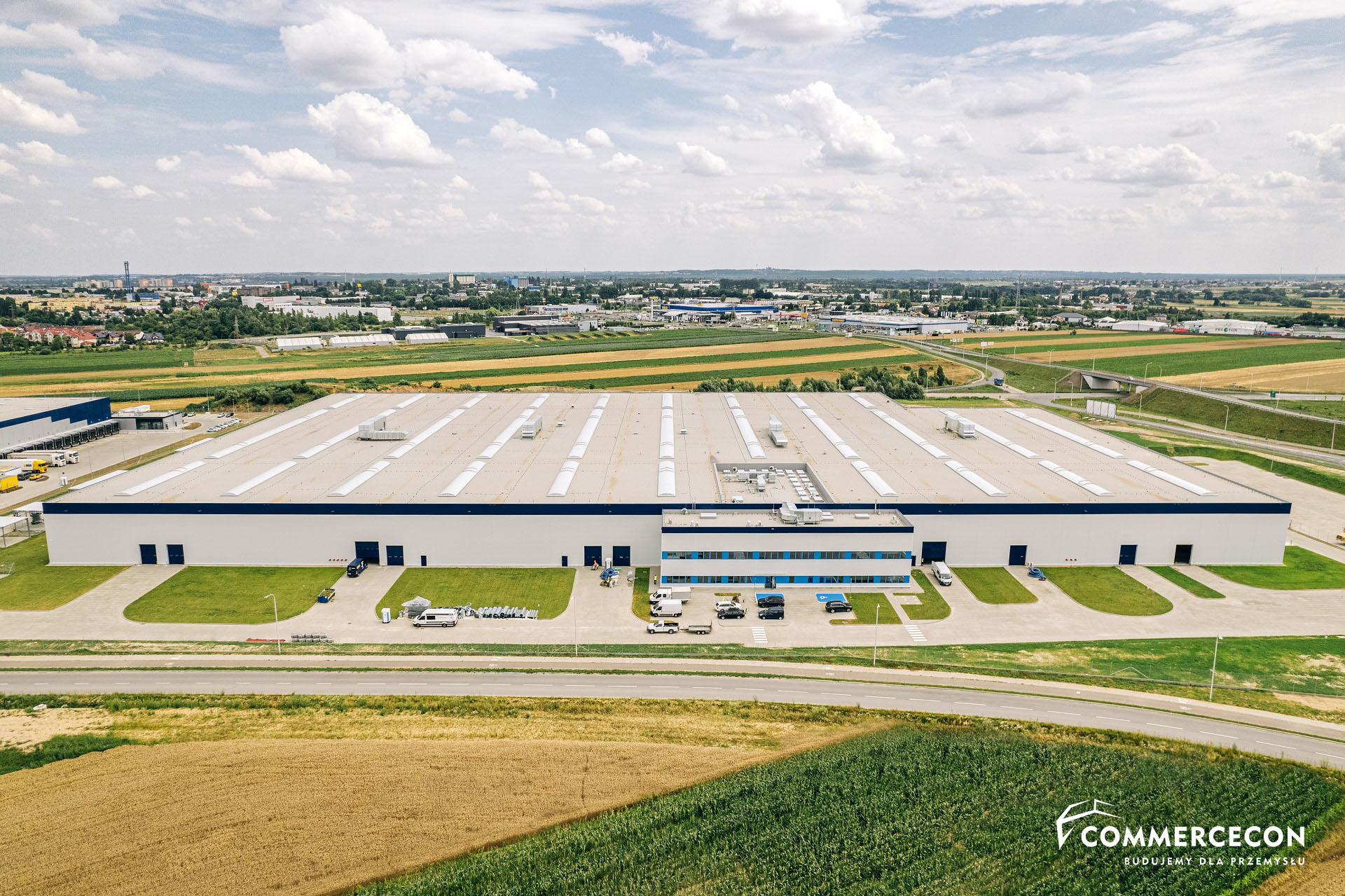
Build-to-suit facilities are not new on the property market, and tailor-made production and warehouse halls have been gaining popularity for several years. This solution is dedicated to demanding customers who want the building and its equipment to be fully adapted to the needs of their business. BTS facilities offer users the benefits they would not get if they were to buy or rent an existing building, but they can be a challenge to the general contractors. Why?
A build-to-suit project is a facility that is designed and built to order for a specific customer. Such solutions are most often offered by developers, but can also be ordered directly from a general contractor. They are built for both warehouse and production customers. For example, they help the former to make maximum use of storage space, while the can rationally use the floor space and make efficient use of all the technical solutions installed. However, the list of benefits is longer. What else can we find?
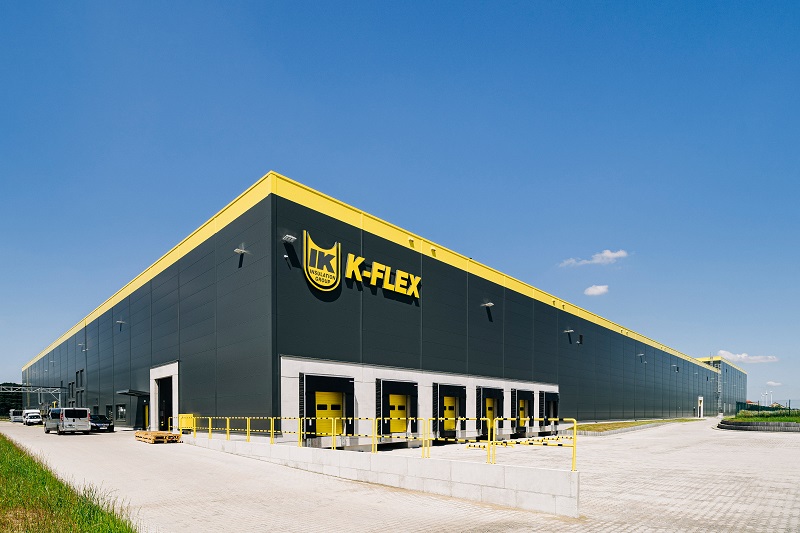
Location choice possible
One of the key factors in customers choosing to build in a BTS formula is the choice of location. A rough location on a map is often enough, but it is important that it meets a number of the customer’s requirements. What is the priority for them? – This is primarily the availability of technical infrastructure: utilities and road access, but also a network of suppliers and potential customers in the vicinity of the future project site. A well-developed labour market and availability of qualified workforce for the new-built production plant or warehouse are also important. To conclude, it is important for a location to guarantee fast construction and efficient business operations in the future – explains Marzena Tkaczuk, BTS Development Director Head of BTS Integrity & Management at Panattoni.
But some customers happen to be very clear on the location of a future plant. – This was the case with our recently delivered project for Panattoni, whose customer is a global provider of innovative solutions for the industry and the construction sector. The modern production and storage hall was erected just 5 km from the manufacturer’s present site. Thanks to that the production at the new location will rely on the existing skilled team of specialists, which has been a priority from the start – explains Piotr Błaszczyk, Commercecon’s Construction Manager responsible for the project on behalf of the general contractor.
Tailor-made space design
When deciding on a BTS project, the customer has the opportunity to arrange the space as needed from the very beginning. This flexibility applies both to the size of the facility (within the limits of the available plot) and to its division into individual utility zones: production hall, warehouses, social facilities or offices. Speaking of offices, it is worth mentioning here a new approach to the design of modern warehouse spaces.
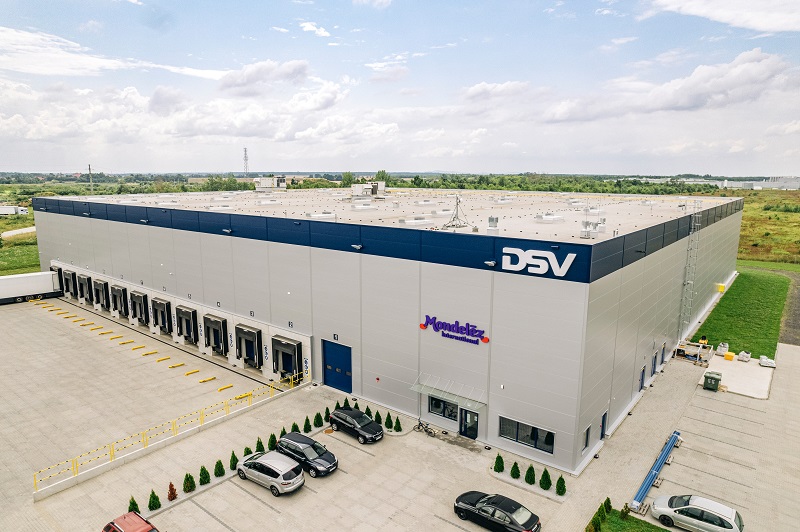
As the latest trends show, the share of offices in the total usable area of buildings in the logistics industry is constantly growing, sometimes exceeding ten per cent. – Customers’ expectations regarding the standard of finish are also growing rapidly – office space in newly built warehouses often does not differ from the standard offered by office buildings located in the centres of large cities. With a customised approach to design, the customer receives a facility that is ideally suited to the type of business which, on the one hand optimises construction cost, while, on the other, reduces future expenses on day-to-day use of the building – adds Piotr Błaszczyk of Commercecon.
An extremely important thing, which also speaks in favour of the build-to-suit building, is the adaptation of the building’s structure to the technology deployed, and thus to the machinery and technical equipment. This is particularly true for manufacturing facilities. What are the most common requirements faced by general contractors?
BTS construction formula not for every contractor
The complexity of build-to-suit projects means that the choice of a general contractor becomes a key issue in determining the success of such developments. Not everyone will be able to cope with the complexity and scope of the work, and ensure specialised construction machinery needed to deliver to the required accuracy and timing. Another issue for many smaller construction companies can be constant engagement of the executive team, who must work closely with the developer at every stage of the work, and often with the future user of the building directly involved in the project.
What requirements do we most often face when it comes to building construction? – This can be illustrated by the example of the project mentioned earlier. One of the greatest challenges was the installation of the several-tonne cranes several dozen centimetres below the roof structure which required exceptional accuracy of the installation work. Also noteworthy is the construction of the plant foundations, for which more than 750 tonnes of concrete were used, and the special flooring, in the steel warehouse, which can withstand the load of 70 tonnes per rack foot. It is also worth mentioning the use of automated building management systems and the installation of an intelligent system for monitoring of roof structure deflection that will accurately notify you of the moment when snow needs to be removed – explains Juliusz Kuźnik, Director – Head of BTS Technical & Construction Panattoni.
Note that the construction of a production plant requires not only the preparation of a structural design of the building, but also the development of the plant design. It must include all special services required by the production process. These include, for example, air extraction, compressed air, power generators or high-tech dust extraction and sprinkler systems which require considerable experience to install.
– When talking about build-to-suit projects, the financing is also what deserves attention. They can be developed both, as rental units and the customer’s property – the build-to-own (BTO) formula is then involved, where the cost of the project is borne by the future user – clarifies Marzena Tkaczuk from Panattoni, the leader in the BTS space market. According to the company’s expert, the developer has so far completed more than 2.9 million sq m of BTS space, with another half a million under construction.
Read also the article: Industrial hall roofs under constant surveillance. Artificial intelligence supports security