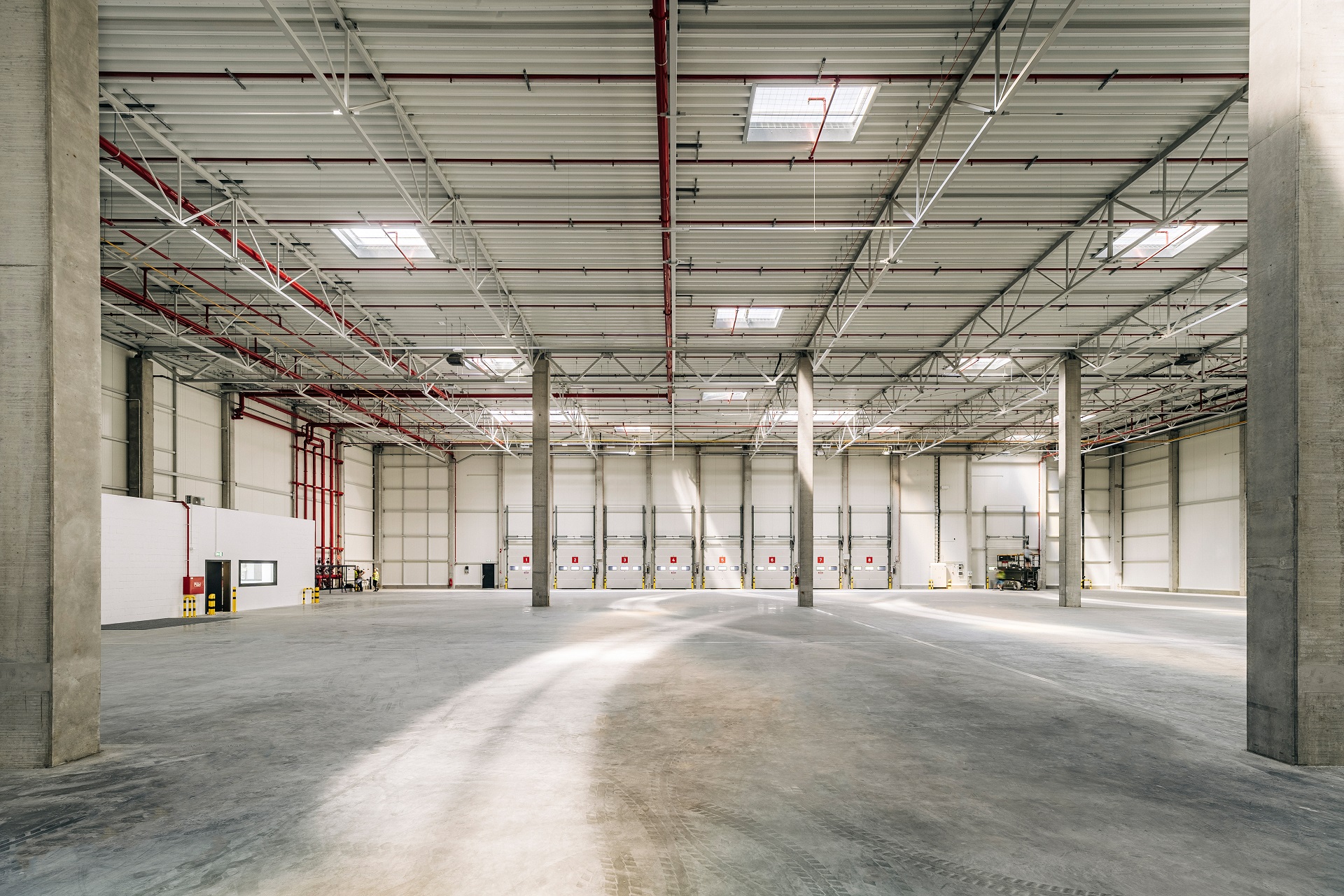
Industrial flooring is a special finishing solution dedicated to industrial facilities. Everyone has certainly experienced them – they stand out visually with their uniform, even structure. How are industrial floors constructed, what are their types and what is a layered system?
What is an industrial floor?
Industrial flooring is a type of floor finish used in large facilities such as warehouses, production and logistics halls. You can also find them in supermarkets, garden centres and DIY stores.
Choosing the right industrial flooring is key to maintaining the safety of work and the high usability of the building. Floors in industrial halls have higher strength and a completely different construction. Industrial flooring is very durable, resistant to mechanical damage and often also to individual chemicals. No additional work is required during the life of the building. What is more, it can withstand heavy loads and high and low temperatures. The particular properties of such floors will vary depending on its type and material, including, for example, the concrete mix used for industrial flooring in the construction process.
Types of industrial flooring
There are several types of industrial flooring. Some components of the floors may be identical for different varieties. These includes the base course and substructure. The key distinguishing element is the wear layer, i.e. the finishing layer. It affects important performance characteristics (e.g. anti-slip properties) and the looks. The choice of a particular type also affects the cost of the industrial floor. The most popular industrial flooring options today by type of finish include:
- concrete floors – indoor and outdoor concrete layers are very durable, impact resistant and dust-free; the cost and exact thickness adjustment are additional advantages,
- acrylic floors – steel halls and buildings that also have a representative function can have an acrylic finish, which is very aesthetic; another important advantage is short installation time,
- epoxy floors – highly resistant to abrasion and easy to clean are the reasons for the great interest in epoxy floors in the food industry, but not only.
Construction of industrial floors
Industrial concrete flooring is made in several stages, which correspond to the individual layers. The work begins with preparing the ground. In terms of construction, expansion joints are a characteristic element of flooring. Expansion joints of industrial flooring consists in cutting the floor into separate sections. The gaps must then be filled with a special heat-expanding agent. Their depth should be 1/3 of the thickness of the floor slab. The specific way in which the joints are made and the choice of measures will vary, among other things, depending on what type of industrial floor you are building. This protection makes the floor extremely durable and resistant to deformation that could occur during intensive use.
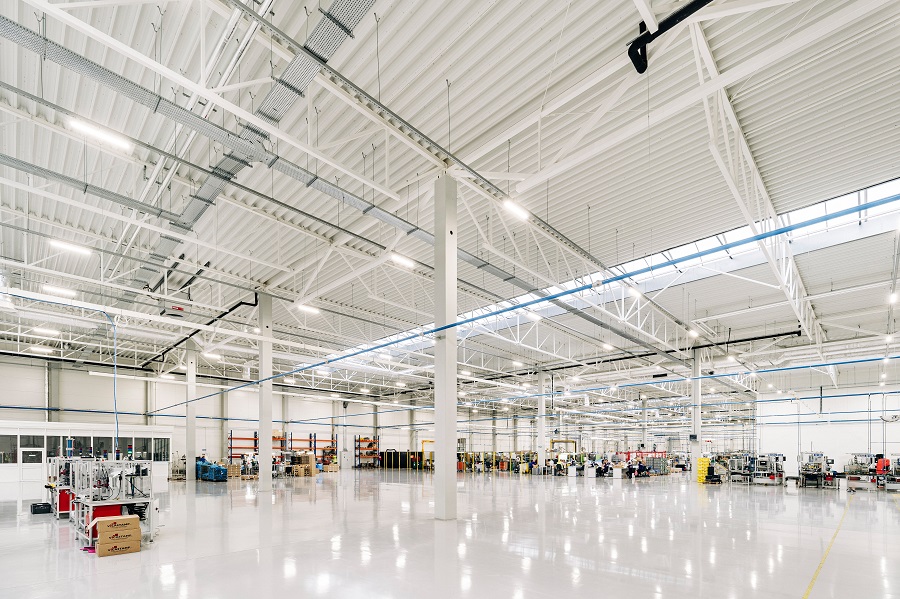
Industrial flooring – layers
Typically, industrial facilities have to cope with heavy loads, so the flooring in warehouses and factories should be extremely durable. The resistance of the floors depends on the design, i.e. primarily the layers. An industrial floor is usually built of the following layers:
- substructure – this is the “foundation” of the floor which is laid on top of the subsoil and may consist of sand, gravel or lean concrete.
- capillary rise barrier – made of two coats of polyethylene film of appropriate thickness (approx. 0.3 mm).
- insulation layer – consists of moisture protection (e.g. bituminous materials, membranes) and thermal insulation (e.g. polystyrene) coats which prevent from cold and moisture penetration.
- load-bearing concrete – traditional steel bars as well as dispersed fibres can be used for reinforcement.
- wear layer – a finishing coat that can be made of different materials, e.g. concrete, cement, acrylic or resin.
What should be the thickness of an industrial floor?
Depending on the type, industrial floors can range from 0.5 mm to approx. 300 mm in thickness. The thinnest floors are made of resin. The most common industrial concrete floors should have a thickness of at least:
- 120 mm – for floating variants,
- 80 mm – for surface cured floors.
The thickness of the floors is influenced by the desired of load performance level. The differences in thickness are mainly due to the layer of reinforced concrete, e.g. with dispersed fibre. As a general rule, the greater the load that such a floor has to withstand, the thicker the layer that has to be applied.
Examples of industrial flooring projects: