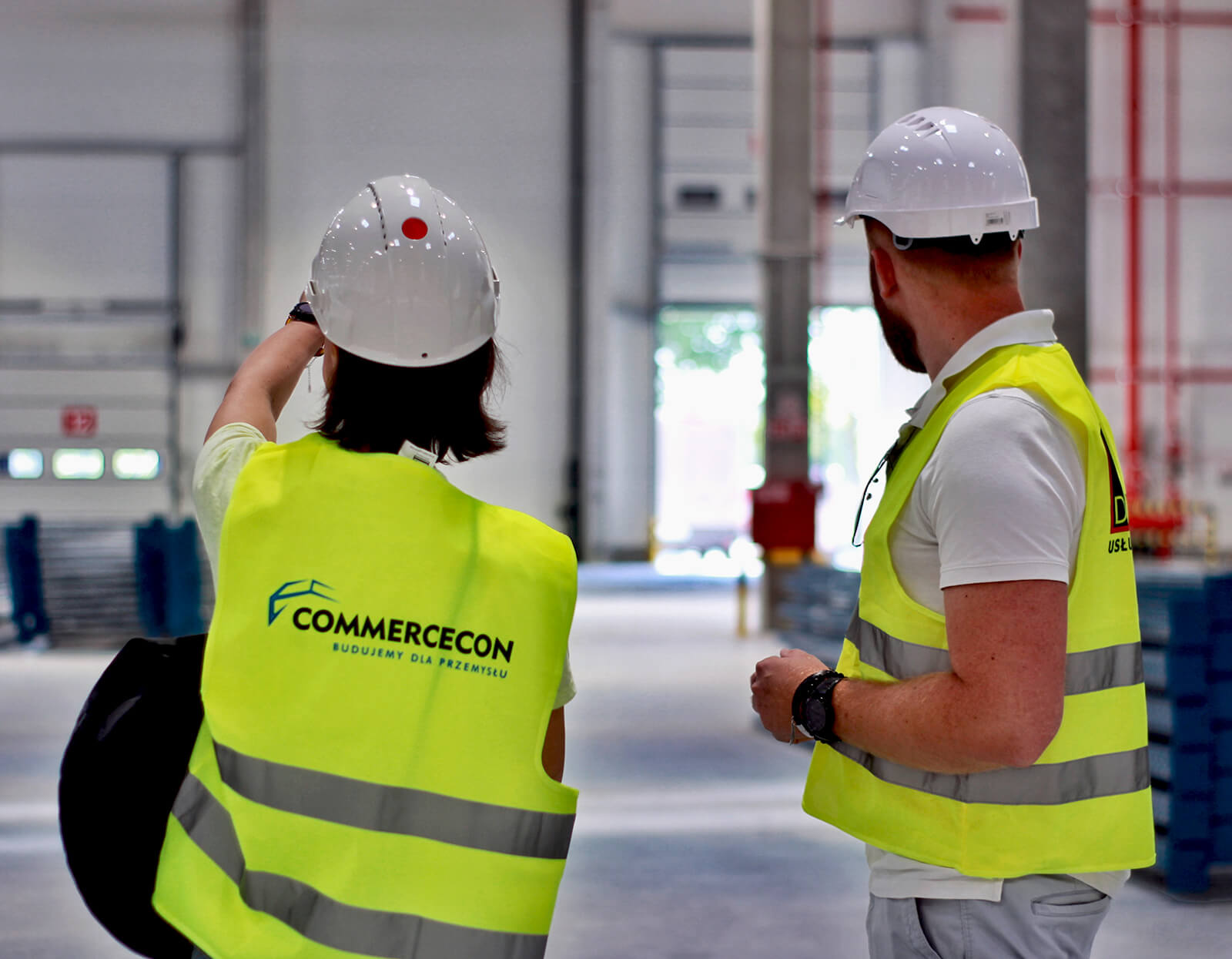
The industrial construction market in Poland has strongly accelerated due to the pandemic. Development of e-commerce and the insecurity of supplies from Asia, forcing businesses to shorten their supply chains by opening factories locally, have led to demand for warehouse and production space to reach a record 5.2 million sq. m in 2020. However, the increase in the construction of new production halls can also result from the development of businesses and the growing demand for their products. How should an investor prepare for the construction process? What details could a potential industrial hall contractor be interested in? An expert from Commercecon, a general contractor for this type of facilities with a long tradition, answers the above questions.
Construction documentation is a must for a project kick off.
Having decided to build a production plant, the investor should brace for a lengthy and sometimes complicated preparatory procedure. Being aware of that, many investors at this stage choose to involve their prospective general contractor in the formal procedure.
“This is a very good decision. Many investors may get lost in the maze of legal and administrative complexities, and the situation can be aggravated even further by frequent changes in the construction law of which a business owner may not be aware. This is where companies like Commercecon come in, keeping abreast of the new regulations and ensuring that all documentation is prepared in compliance with them. It is important to realise that obtaining a building permit sometimes involves a huge time commitment that investors usually cannot afford” – explains Monika Górko, Architect at Commercecon.
However, if an investor decides to handle the formal matters on their own, they must obtain a map for the location or design of the plot and establish whether a zoning plan exists. If so, it must be verified whether the zoning plan aligns with the investor’s expectations and an extract from the plan must be obtained. If no zoning plan exists, the investor is required to apply for a land development conditions decision. One more requirement is to obtain technical conditions from suppliers of utilities, such as electricity, water, gas, etc.
How much floor area does the plant require?
Another stage of preparations is to determine the desired area for the planned project. This information is critical for the general contractor. What other questions could be asked?
“The contractor will for sure want to have a brief description of the technology process, which often determines the shape of the building and the division into individual sections, such as the production hall, the warehouse for components and finished products, laboratories or offices. Remember that building a manufacturing plant to make specific products requires a technology design” – adds Commercecon’s expert.
At this stage, it is worth resolving on the future expansion of the plant, as it affects the design and construction of the building being erected. This information will help you design the building and plan its location on the plot in the most optimal way.
Production profile and material storage
The characteristics of the process mentioned earlier are also crucial in determining the type of systems needed. This involves more than just electrical power, lighting, water supply and sewage, and HVAC systems. Specialist systems required for the production process (compressed air supply, air exhaust, dust extraction or sprinkler systems) and also heating are also required. It is sometimes the case that the heat needed for building heating can be drawn from the process. This solution will reduce the building running cost and aligns with the green trend in industrial construction.
The details of the planned machinery or process lines are another key piece of information in terms of the building construction and its timing. Both, the size (any extra loads on the foundation and other structural components to which they will be fixed), and the planned installation date are also considered.
The storage of components for production and finished products, i.e. how they will be stored and in what type of packaging, should also be considered. This may affect the fire load of the hall and the selection of a suitable sprinkler system.
Internal handling and external logistics
Most medium and large production halls require mechanical handling equipment. Various types of carts, fork-lift trucks and other vehicles moving on internal roads are typically used for that purpose. They may vary in terms of how they are powered. Although the power supply details may seem irrelevant to the investor at this stage, it is of key importance for the general contractor. In practice, this requires the contractor to design extra solutions, e.g. umbrella roofs for gas cylinder storage or charging stations for battery-powered trucks and carts.
Every production plant requires also the external means of transport to be planned to handle component deliveries as well as the loading and export of finished products. At the construction planning stage, the need for loading docks (number and type) must be determined, along with the estimated traffic volume and type of vehicles predominantly used in the logistics. This will affect the land development around the building and will allow for an optimal connection of the plant to a public road through a junction.
The above list of aspects to be discussed with the general contractor is by no means exhaustive. However, it gives the investor an overview of the decisions to be made at an early project planning stage.
Find out more about Commercecon’s comprehensive offer.