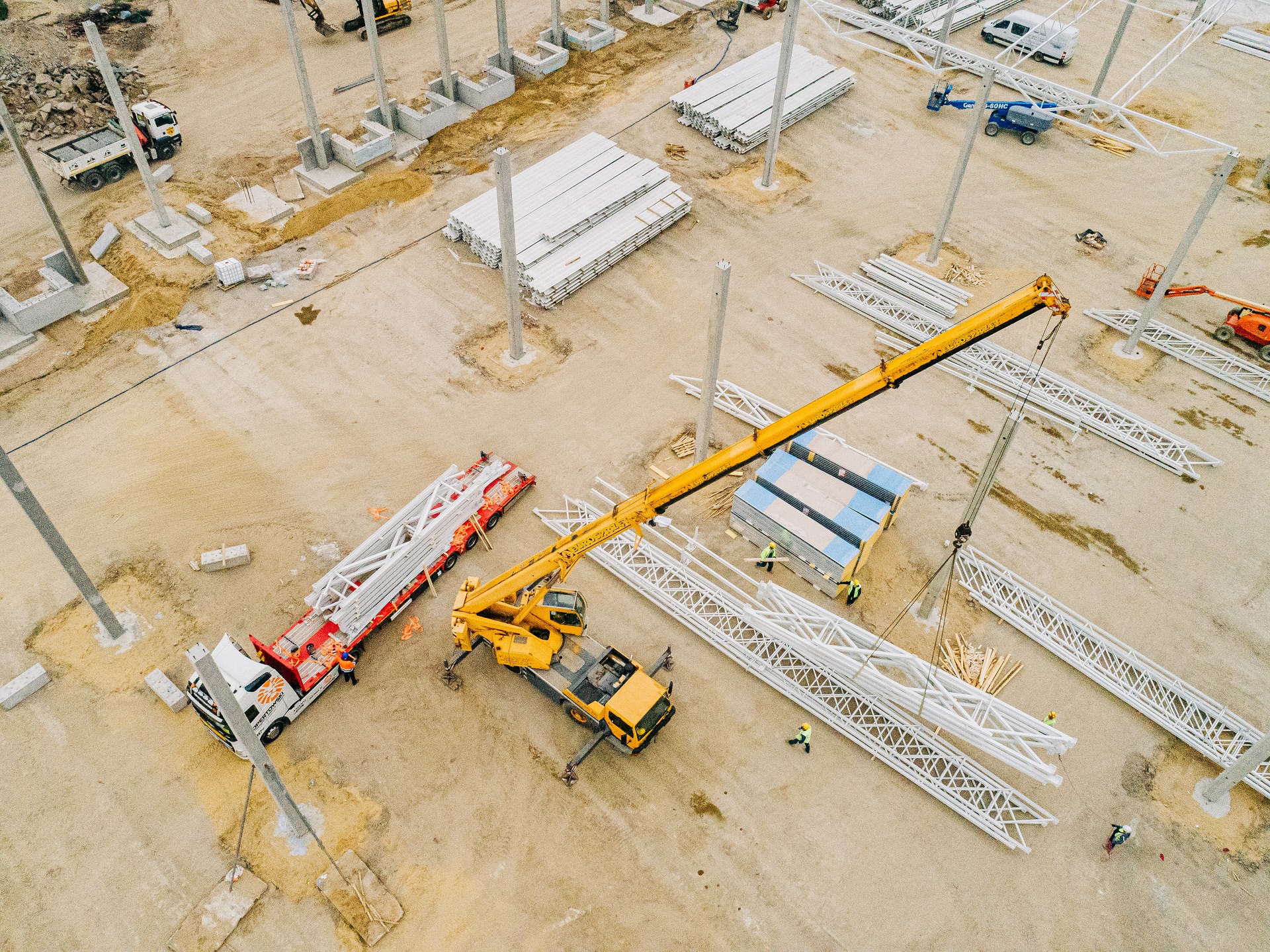
What are the stages of steel hall assembly?
The investment process of building a steel hall is a complex and time-consuming undertaking that requires a great deal of knowledge from all stakeholders. This involves statisticians, designers, architects, installers or work organisation experts. Five main stages of steel hall construction can be identified:
- collecting documentation and drawing up a design for the facility,
- fabrication of structural elements (prefabrication),
- assembly using prefabricated elements,
- installation and finishing works,
- acceptance and obtaining the required permits.
Quite obviously, the assembly of the structure is one of the construction stages of the hall. At the same time, it is a kind of validation of the assumptions made by the designers. All steel elements (shipping elements) must be positioned in accordance with the assembly drawings included in the detailed design. A structure is considered technical when its assembly is as simple and uncomplicated as possible, and the structural components are connected only with bolts, without the need for on site welding.
The assembly of steel halls is a schematic process and can be divided into the following stages:
- Construction site preparation,
- Foundation works,
- Correct installation of steelwork components (columns, rafters, purlins, bracing, transom structure),
- Installation of wall and roof cladding,
- Installation of joinery (doors, gates, windows, skylights) and flashings,
- Construction of a concrete industrial floor.
Of course, one of the most important factors is the time it takes to build the hall. Therefore, stages 5 and 6, which are referred to as finishing works, can be carried out in parallel.
The remainder of this article will describe the above-mentioned stages of steel hall assembly.
Steel hall assembly step by step
The first step to be taken in assembling a hall, once the relevant permits have been obtained, is to organise the construction site accordingly which is crucial to the efficient and smooth erection of the steel hall. To begin with, the site needs to be fenced off, the access road planned and the ground paved to allow for safe installation work using heavy equipment (crane, skips). Staff facilities for employees (toilets, rest and eating areas) must also be provided. Safety on site is a critical matter of course. A fire extinguisher and a first aid kit are therefore indispensable. A considerable amount of waste is generated during the works. Therefore, it is important to remember to bring waste containers to the construction site.
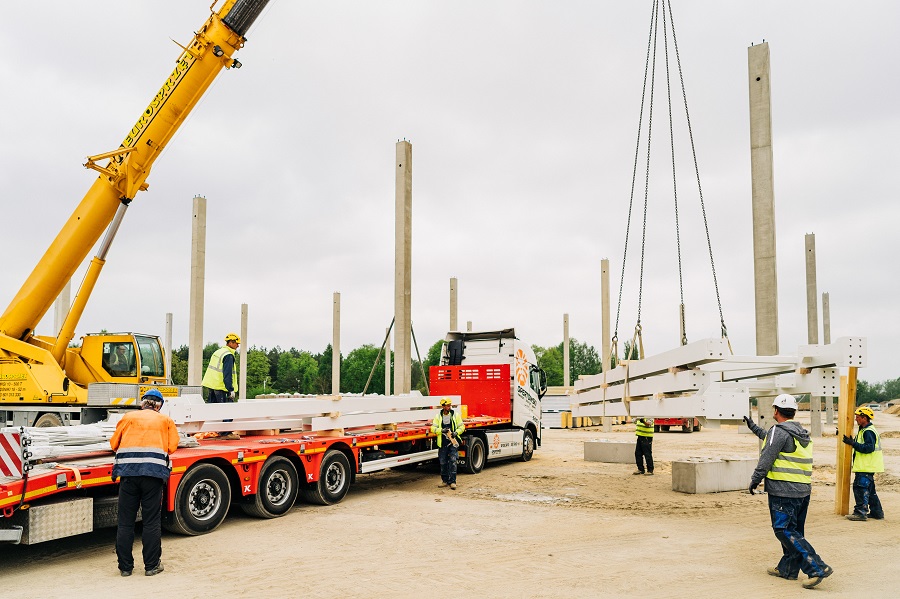
The next step is the construction of the foundations, or more precisely the construction of the footings, as industrial halls do not require a full linear foundation or a surface foundation slab. Foundation footings can be made as solid, on the site, or in the form of precast elements brought to the site. Both solutions have their advantages and drawbacks. A solid foundation means lower construction cost, but it is important to remember that concrete achieves its design strength after 28 days. This requires breaks after concrete pouring. Prefabricated footings are a more expensive solution because they are usually outsourced to specialist companies. The advantage is that they do not require process breaks, as they are delivered to the site according to schedule requirements. When using prefabricated footings, however, it is important to consider their weight, which often exceeds 7 tonnes for a single footing unit of a typical steel hall around 12 metres high.
Once the foundations are in place, the actual installation of the steelwork components can begin. At Commerceceon, an assembly plan is always drawn up. Structural components should be adequately prepared in the factory so that assembly work proceeds smoothly and without downtime. It is a matter of drilling and anchoring them properly and accurately so that they can be joined together easily using screws. The erection of the steel hall begins with the setting and anchoring of the main columns (a technology involving the setting of entire frames of the structure is also possible). The roof girders, which are the main load-bearing element of the roof, are then installed. These elements can be solid-walled, made of rolled sections (IPE, HEB, HEA) or their counterparts made of flat sheets (plate girders), which can then often have a varying section height along the element; alternatively, truss girders are also made. It is particularly important to level and ensure the verticality of the aforementioned elements. This has implications for the final aesthetics of the hall and its safe use. The contractor then moves on to the installation of the secondary elements. These include roof purlins, wall and roof bracing, cladding rafters, gate and window substructures and other elements provided for in the design. At this stage, the pre-tensioning of the bar bracing is very important. Once all the components have been bolted together, it is time to move on to paint touch-ups to protect the steel components from corrosion. This is an indispensable operation, as any damage of it (caused during transport or installation) will result in corrosion outbreaks appearing more quickly.

Once the frame of the steel structure is in place, the cladding installation can begin. In uninsulated steel halls, trapezoidal sheeting is used as the covering in most cases. If the hall is insulated, then sandwich panels are a good solution. The cladding elements are fastened using self-drilling screws of the appropriate length to suit the solution adopted. It is important to remember that the roofing is done first and the wall cladding then. The next step is to close all the hall openings with the finished products specified in the design: windows, doors, gates, skylights, docks. The right location and number of windows reduces the cost of illuminating the hall during its operation. The final closure of the facility is achieved through the installation of doors and gates. They can be insulated or uninsulated, with manual or electric drive. The next stage that is closer to the end is the installation of the flashings. This is an important stage that affects the visual aspect of the building and seals the hall against weather conditions. These include the finishing of corners, ridges, eaves and wind braces. An industrial floor can be made at the same time. Its durability and endurance over the long life of the facility is important. Therefore, the most common concrete floors are provided with steel or polypropylene reinforcement. Expansion gaps are very important to prevent the floor from cracking. After 28 days, the floor achieves its full strength. The contractor then moves on to providing the hall with the necessary services (sewage and water supply, heating and ventilation). Depending on the nature of the project, these may additionally include refrigeration or gas systems. The final stage in the construction of a steel hall is the landscaping around it. Based on the Investor’s vision, fences, car parks, roads, footpaths, landscaping and greenery are constructed. The culmination of all stages is the submission of the building to the authorities for acceptance.
Assembly of a steel hall according to Commercecon
Commercecon is a company with an established brand not only in the domestic market, but also abroad. We provide the Investors with assistance at every stage of the project. We offer drafting of a design to the best quality assurance and the installation of the structure based on skilled workers with state-of-the-art tools and machinery. We always prepare a detailed installation plan to keep the work on schedule.
If you are looking for a company that builds steel industrial halls of the highest standard, then we encourage you to visit the Commercecon website. The Investor’s Guide section provides a number of interesting articles on building steel halls. You can find our offer for the supply of steel structure assembly under the link https://commercecon.pl/en/offer/delivery-and-installation-of-steelwork/.