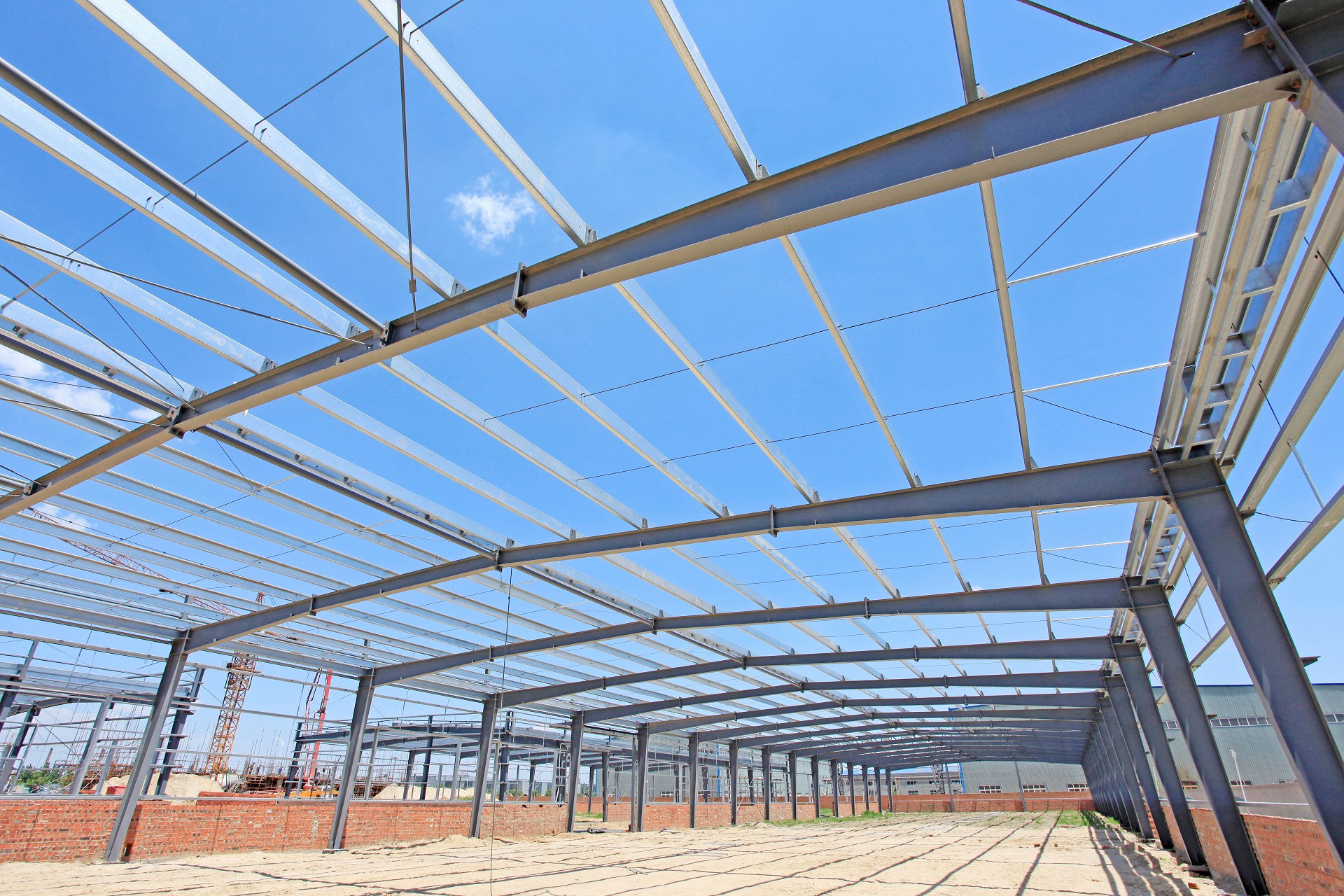
Purpose of Z purlins
Today, steel halls, with their various uses, are among the most popular building structures. Their structure consists of columns, rafters, bracing and purlins, which are the beams that support the roof. It is the purlins that are the elements that are very often made from cold-bent profiles such as Z purlins. This is a very economical approach due to the low weight of this type of profile compared to hot-rolled purlins (e.g. IPE, HEA). The cladding, usually flat (trapezoidal sheet metal, sandwich panels), requires good adhesion and connection to the substructure. Z purlins are sections that are able to meet these requirements because their belts are parallel to the cladding providing a large contact area. In the case of purlins, it is very important that they usually slope in line with the roof slope. This affects the way these components work and carry loads and significantly affects the choice of cross-section. In simple terms, it is a question of whether the resultant load passes close to the axis of symmetry of the section. If this is the case, torsion, which is very unfavourable for open steel sections, is minimised. In addition, the choice of purlin profile will depend on the installation and strength conditions. Initially, Z purlins were made as pieces with uniformly wide webs. In this case, the centre of gravity coincides with the centre of shear and for this reason they work as diagonally bent elements (without torsion). Computationally, this is a major advantage, but technology and installation requirements have resulted in Z purlins now being designed with webs of different widths (usually the top foot is wider). This makes it easier to create lap joints in the buttress zones, pulling the beam from the section sections. In addition, the angled edge bracing of the Z purlins allows for easy package formation, as one section can be slid into another. This is also advantageous for reasons of transport and on-site storage. In the case of bent sections, stronger steels are used than those commonly used for hot-rolled sections. It is usually a steel with a yield strength in the range 350-460 MPa. This is dictated by the desire to achieve maximum load-bearing capacity with minimum element weight. For this reason, the serviceability limit state (deflection) will rarely be decisive for the selection of this type of section. Thinning of section walls increases the load-bearing capacity and rigidity of the section, but the consequence is the occurrence of local and distortional instability. This is reduced by using edge and intermediate stiffeners in the form of bends, folds or furrows that run along the longitudinal axis of the Z purlin.
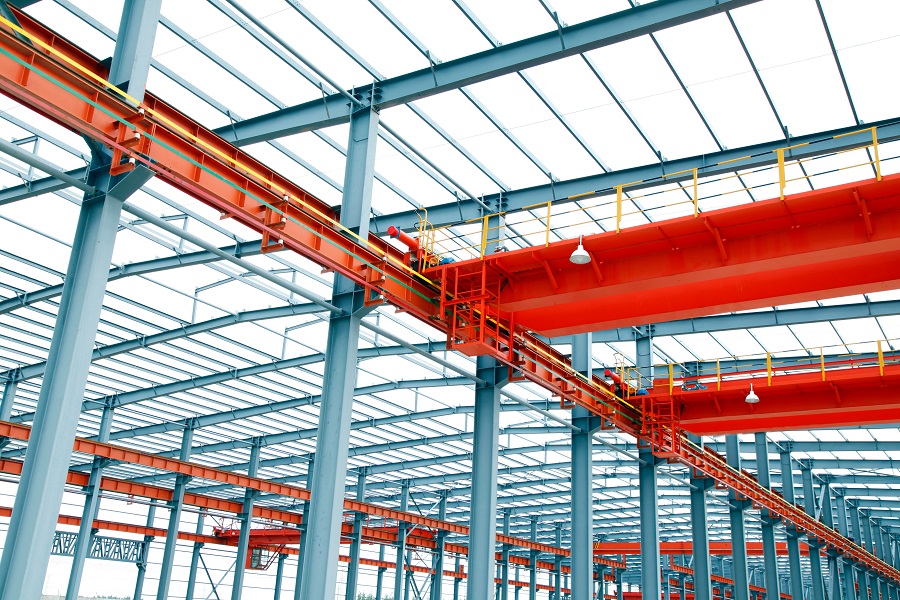
A separate and at the same time very interesting group of cold-formed profiles are hat sections. They belong to the omega (Ω) section group. Their main advantage is that they have a vertical axis of symmetry on which the centre of gravity (G) and the centre of shear (S) lie. This is very important for the operation of a beam made from such a section, as its deformation corresponds to pure unidirectional bending (torsion and diagonal bending do not occur). This leads to a significant reserve of load-bearing capacity compared to z sections or channels. The hat section acts as two adjacent Z purlins, connected by sheathing. Sections of this type are particularly popular in the southern hemisphere (mainly Australia), where they are successfully used as roof purlins.
The production of bent sections was first mentioned as early as in 1855. At the end of the 20th century, systems of small halls made entirely of bent sections were already being developed. Cold-formed profiles, such as Z purlins, became widespread with the publication of the world’s first design guidelines for bent section components in the USA in 1946.
Dimensions of Z purlins
Z purlins are very common load-bearing elements in steel structures with purlin roofs. These certainly include industrial facilities including steel production halls and warehouses. For this reason, their product range is highly developed. Manufacturers offer slightly different solutions when it comes to the dimensions of the Z purlins. Crucial to the lightness of these elements is the thickness of the sheet metal from which the Z purlins are formed during the bending process. In general, it can be assumed that the sheet thickness varies between 1.0-4.0 mm. The height of the Z purlin is assumed to be in the range 100-450 mm. It was mentioned in the previous headline that the widths of the upper and lower shelves are usually different, due to strength and installation advantages. The upper shelf (usually wider) is 45-100 mm wide, while the narrower, lower shelf is 40-95 mm wide. The choice of plate thickness, section height and Z purlin wall proportions depend, of course, on the length of the beam (purlin) and the gravity (cladding weight and snow) and uplift (wind) loads assumed. Z purlins are very lightweight sections. Their weight ranges from 1.6 kg/m to as much as 18.2 kg/m for the highest cross-sections made from sheets of 3.0÷4.0 mm.