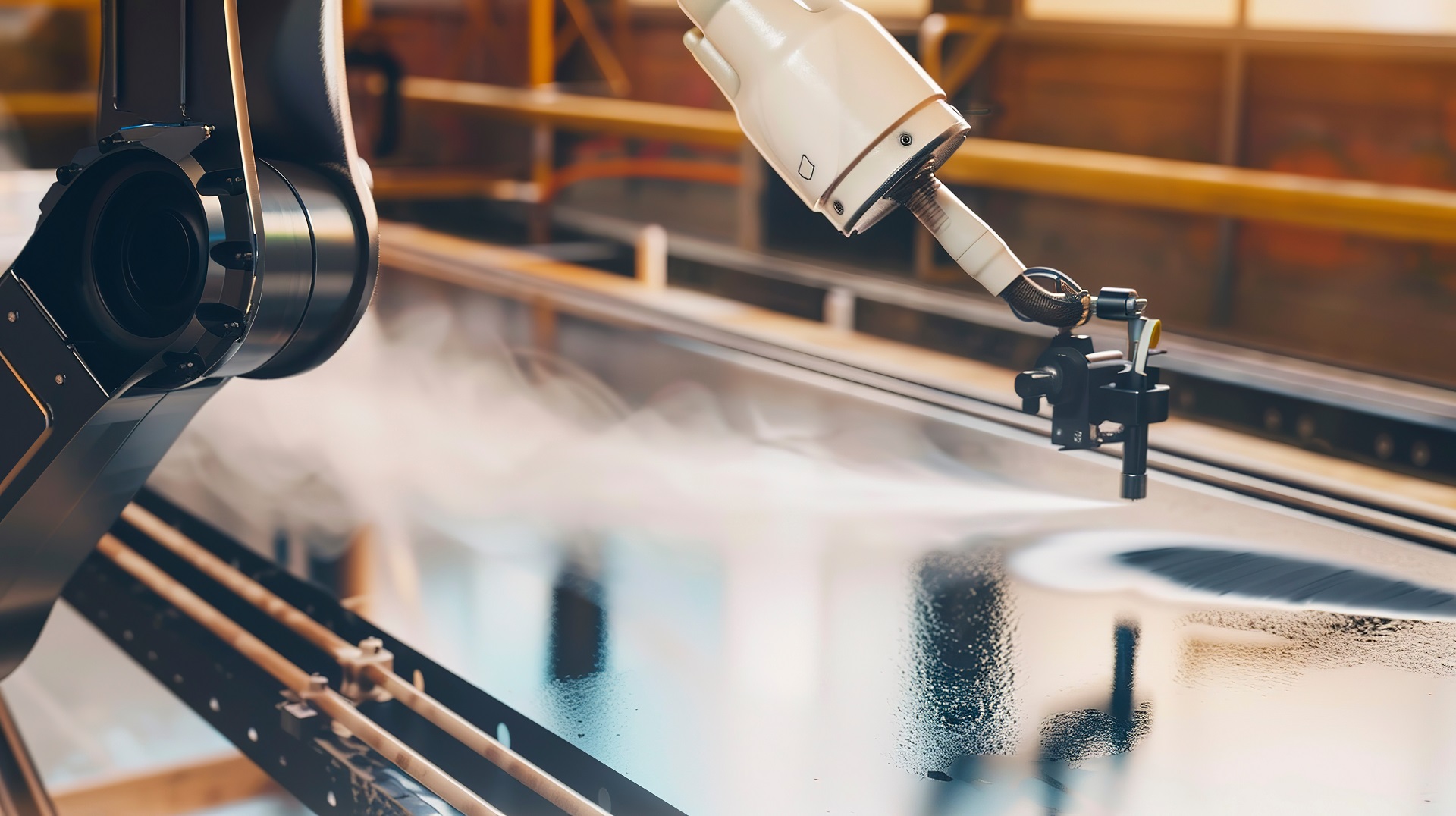
Types of corrosion protection paint for steel structures
Steel structures are currently one of the most favoured constructions, especially when it comes to the industrial sector. Steel halls of various purposes, whether for manufacturing or warehousing, are structures usually built using steel as the load-bearing material. This is due to the lightness of the structure, its high strength and the ease and speed of installation. It goes without saying that, as an Investor, we want these facilities to perform their functions for as long as possible without incurring additional operating costs. This is an issue directly related to the durability of the structure and the assumed service life. For the structures mentioned earlier, such an estimate is 50 years. Factors that negatively affect steel structures are:
- corrosion;
- material fatigue;
- mechanical wear and tear.
Of the factors mentioned, it is corrosion that has the most destructive effect. It is important to realise that corrosion will not threaten enclosed structures at humidity levels below 80%. In other cases, the structure (especially the joints) should be designed to provide access for maintenance. If such access is not possible, material allowances that take into account the negative effects of corrosion are used.
The most commonly chosen means of corrosion protection are specially formulated paints and coatings.
The best and most popular types of paint currently used to protect steel structures are listed below:
- Acrylic paints – these are modern anti-corrosive paints with good durability properties and are resistant to weather conditions, including UV radiation. Their indisputable advantage is that they need minimal substrate preparation. They are quick-drying, water-based and protect the structure for 20-25 years. Acrylic paint will perform well in contact with seawater or acids. A structure covered with it looks good and is therefore often used in bridge or viaduct maintenance.
- Polyurethane coatings – paint designed mainly for contact with heavy chemicals and very high humidity. Used in permanently submerged components or to protect moving machine and vehicle components. It can be used as a primer as well as a topcoat.
- Alkyd paints – paints with good durability characteristics. Mainly for priming. Used for the painting of structural components, parts of construction machinery, agricultural machinery, boats, cars. They have high hardness and resistance to impacts or scratches. They withstand well the effects of chemicals, oils, petrol and high temperatures of 120-150˚C.
- Epoxy paint – creates a high-strength surface which, through the addition of anti-corrosive pigments, is also widely used for corrosion protection of structures. It is capable of producing a thick protective layer (150 μm) in a single application. It shows high resistance to common oils and solvents. It is therefore applicable to tanks, pipelines or industrial halls.
- Polyvinyl (polyvinyl) paints – used for painting galvanised and coated sheet metal parts, as well as galvanised and phosphate steel. They can also be used to protect components made of aluminium. Used to protect roofs, gutters or parapets. An additional advantage is that they do not leave streaks or stains, which enhances the aesthetic value of the parts being coated.
In addition to these types of paint, there is corrosion protection for steel structures used in ‘special’ conditions. These include, for example, heat-resistant paints that withstand temperatures of up to 600˚C, or specialised products for localised weld patches that often occur during assembly.
It is important to bear in mind that steel construction paints will only do their job if the substrate is properly and carefully prepared, and must be cleaned and degreased before the protective coatings are applied.
Atmospheric corrosivity categories
The anti-corrosion paint is selected depending on the environment in which the component will be located. Five categories of environmental corrosivity have been specified which relate to conditions outside and inside buildings. All categories are listed below:
- C1 – heated rooms with a neutral atmosphere;
- C2 – rural areas with low levels of pollution (applies to outdoor elements) and unheated buildings with condensation occurring (interior of halls, warehouses);
- C3 – urban and industrial areas in medium pollution (outside) and production rooms with high humidity inside (e.g. food production rooms);
- C4 – coastal and industrialised areas (e.g. swimming pools, chemical plants) and interiors of facilities such as swimming pools, structures above sea water;
- C5 – exteriors are industrial areas with high humidity and aggressive atmospheres (maritime, coastal areas with high salinity) and interiors of facilities with high permanent pollution and very high humidity.
Knowing this classification, it is possible to estimate the rate of corrosion progression in a given environment and also to approximate the thickness loss of a steel component in relation to one year.
The best paints to protect steel halls
This is a statement to which there is no clear-cut answer, as the choice of corrosion protection paint depends on the type of structure, its location, its purpose and, above all, the conditions in which it will operate. However, elastomers, or new-generation acrylic paints, have a number of advantages that place them at the forefront of the best types of corrosion protection. The long duration of protection, ease of substrate preparation and water-solubility are the main advantages of this type of protection.
Fire protection – which paint to choose?
The situation in which a fire occurs is an exceptional one and requires special treatment, not least from the point of view of securing the steel structure. Under fire conditions, the ambient temperature often exceeds 600-800˚C. These are values at which the mechanical parameters of the steel are severely degraded and the load-bearing capacity of the structural components is significantly reduced. According to the requirements of the construction law, a structure should be designed to be able to carry loads for a certain period of time, referred to as the fire resistance time R. Covering the structure with an appropriate coating allows this condition to be met. Of the outline ways of securing structures, we have two types to choose from. The first is spray protection and the second is intumescent paints (coatings). The advantage of using spraying is the high speed of its application on the structure. In a fairly short time, a skilled worker is able to secure a large area of the structure. This type of insulation makes it possible to achieve fire resistance as high as R240. Intumescent coatings are a modern and aesthetically pleasing solution. It consists of three layers that are both fireproof and anti-corrosive. In a fire situation, the first layer increases in volume under the influence of the high ambient temperature and is additionally charred, providing insulation for the steel. By using intumescent coatings, we are able to provide resistance up to R120.
In summary, steel structures are a modern, lightweight and easily mouldable type of construction. However, due to the disadvantages of steel as a building material, adequate protection of the structural elements must not be overlooked. By choosing Commercecon we are assured of securing, delivery and installation of steel structures will be of the highest standard.