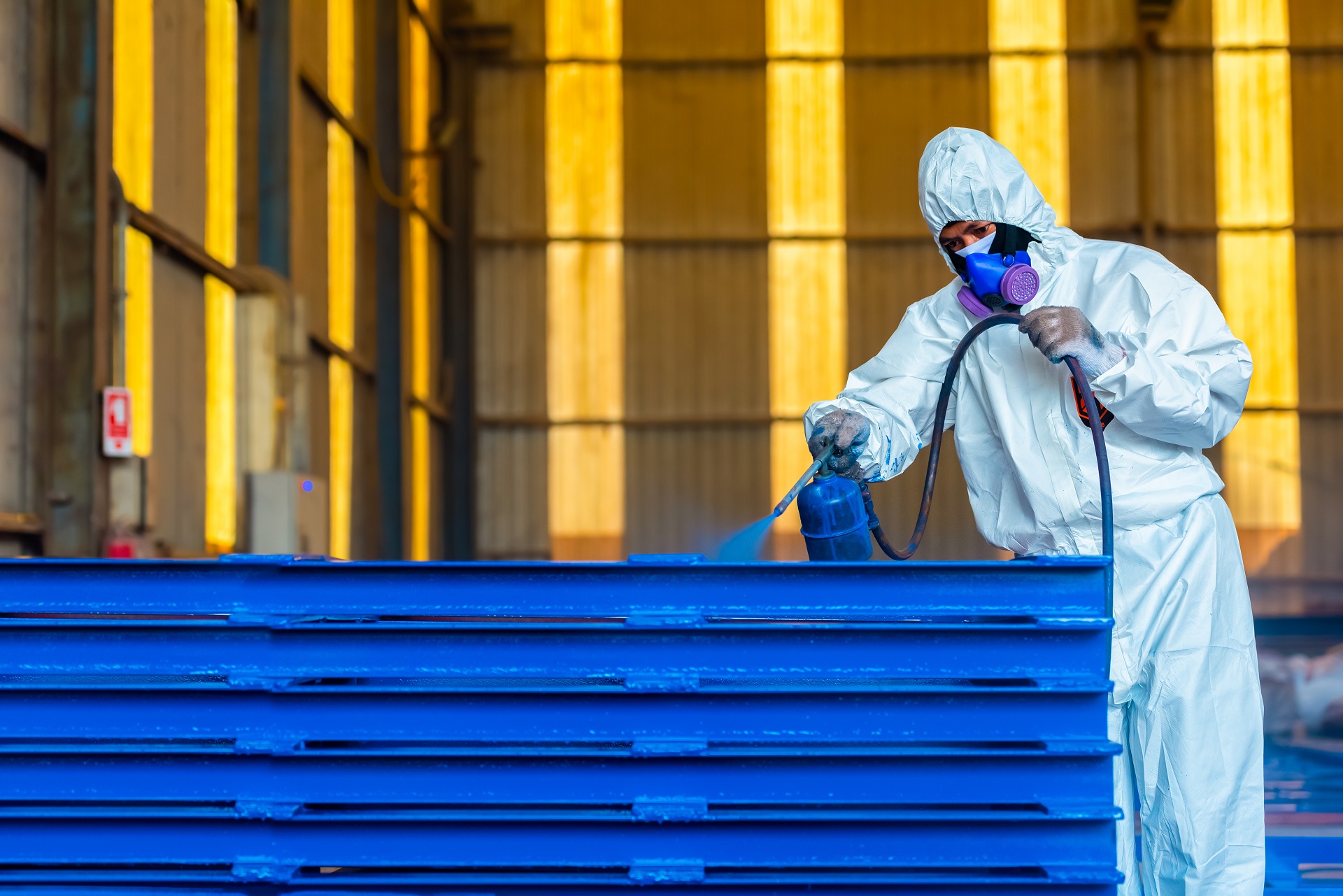
Industrial halls are very often constructed from steel elements. Thanks to its high strength and rigidity, steel makes it possible to achieve large structural spans and make more efficient use of the built-up space. However, this material also has its drawbacks and one of the most significant is its susceptibility to corrosion.
Is it worth protecting halls from corrosion?
Corrosion of steel structures is a very dangerous aspect from an engineering point of view. The process of steel oxidising over time, or colloquially speaking ‘rusting’ the structure, leads to a reduction in the thickness of the load-bearing material and thus to a reduction in the strength and stability of the structure. Thus, corrosion protection is not just an option worth considering but an absolute necessity. Rust-proofing the hall can be done in a number of ways, which are described later in the text.
Corrosion – what is it and what causes it?
Corrosion is understood to be the process of gradual destruction of the metal structure. It occurs under the influence of electrochemical processes or chemical reactions. Furthermore, the rate at which this material-degrading process occurs can also be influenced by radiation, external electric fields or stresses in the loaded or faulty structure.
Electrochemical corrosion is the most common cause and it occurs in electrolyte solutions such as water, in the air or in the ground. It involves the degradation of a material as a result of the oxidation of iron (the main component of steel) on the anodes of the cells, which are fragments of the surface of the corroding object. In this process, an electrical circuit is closed by a liquid exhibiting ionic conductivity (e.g. water droplets).
Chemical corrosion occurs in a non-electrically conductive environment such as the presence of dry non-conductive gases (water vapour) or non-electrically conductive liquids (e.g. grease). In this case, the corrosion process occurs through direct contact between the steel surface and the oxidant particles.
Professional corrosion protection for steel halls
Rust-proofing the hall is an extremely important aspect that affects the safety and durability of the structure, and therefore the facility as a whole. The main idea behind a number of solutions that constitutes corrosion protection is to isolate the corrosive material from the surrounding corrosive environment.
The first group of solutions is the application of different types of paint systems. Depending on the chemical composition, this group includes one- and two-component paints: alkyd, epoxy, polyurethane, polyvinyl, silicone, ethyl silicate and polyvinyl acrylic. Painting systems also include the use of primers, which are categorised as single-component systems. Rust-proofing of industrial halls is most often carried out using two-component epoxy and polyurethane systems. Irrespective of the type of coating used, it is extremely important that the surface of the structure to be painted is properly prepared. The surface of the steel after the welding work is sandblasted and shot-blasted to remove welding impurities and temporary protection agents in order to finally achieve the right surface roughness that affects the adhesion of the paint to the substrate (material to be protected).
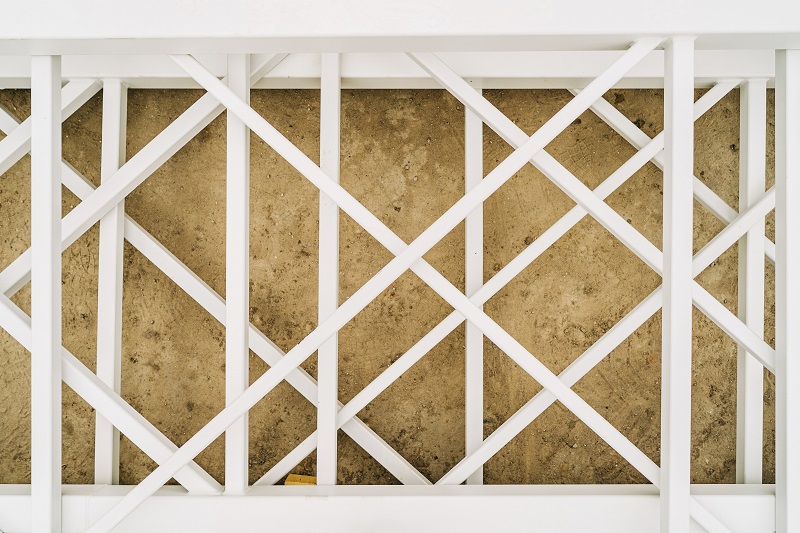
The second most popular group of solutions in the corrosion protection of industrial halls is galvanising. Galvanising a steel structure, as the name implies, involves coating the product with a tight layer of zinc cutting off the parent material from contact with the corrosive environment. There are two processes for coating steel with zinc: hot-dip galvanising and electroplating. Hot-dip galvanising involves immersing steel in zinc heated to 500 degrees Celsius. In the hot-dip galvanising process, the protective coating produced is quite thick but uneven. There is also a risk of damp patches, thus the aesthetics of the structure resulting from hot-dip galvanising are moderate. Quite the opposite is true of galvanising, during which steel products are immersed in an electrolytic bath, resulting in a smoother and more aesthetically pleasing zinc coating which provides an attractive surface finish in the powder coating process. However, the coating resulting from the galvanising process is also thinner and provides inferior protection against corrosion. An important consideration when galvanising a structure is to design it properly. Among other things, suitable process openings must be provided in closed-section components (i.e. pipes) to allow the free flow of liquid zinc.
Corrosion protection of structures must be adapted to the environmental conditions in which the structure is to be operated. The corrosivity categories defined in EN ISO 12944-3:2001 are used for the proper identification of adverse environmental influences. The standard distinguishes categories C1 to C5 from least to most corrosive environments, respectively. Warehouse halls are customarily classified as category C2, while some production halls and outdoor structures (e.g. sheds) are classified as category C3 or higher.
Corrosion protection of steel halls also means designing them properly. This is because it is important to avoid shaping structural elements in such a way that dirt and water can potentially accumulate in hard-to-reach places. The design of structures having deep recesses and pockets should also be avoided because of the difficult accessibility of these areas for painting.
Cost of corrosion protection for steel halls
The cost of corrosion protection for a steel hall is strongly dependent on the corrosivity category of the environment, the protection technology used (galvanising vs. painting) and the durability of the system. There are 3 lifespans: short [L] with a declared lifespan of 2 to 5 years, medium [M] with a declared lifespan of 5 to 15 years and long [H] with a declared lifespan of more than 15 years. Paint systems with a longer lifespan will be more expensive at the prefabrication stage of construction. Note, however, that it is also a significant cost to maintain the structure’s paint finish during operation, particularly in areas that are difficult to access, i.e. where painting is obstructed by stored material or heavy equipment. With a more durable coating, maintenance is less frequent and the final cost of using the initially more durable (and more expensive) coating is not necessarily greater in terms of the overall life cycle of the facility.
To sum up, industrial halls are facilities that absolutely require corrosion protection for their steel components. Professional corrosion protection should take into account the corrosive factors affecting the structure (environmental corrosivity categories), the design life of the coating, aesthetic aspects and the design of the structure, appropriately adapted to the chosen corrosion protection technology.