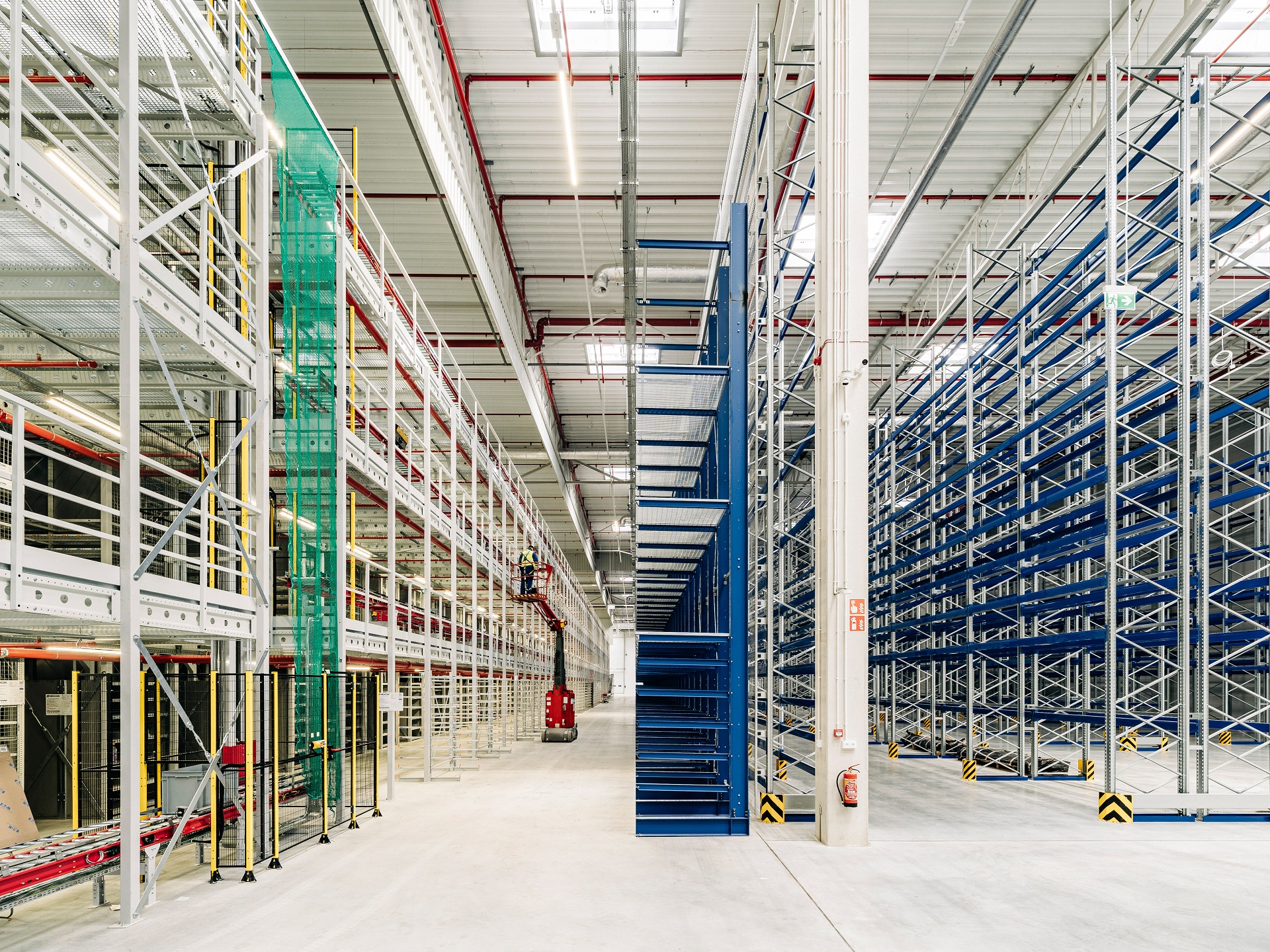
Industrial buildings, whether serving as production halls or warehouses, are commonly designed as steel halls. Steel, thanks to its mechanical properties and weldability, allows buildings with significant spans to be built while having few internal supports and complex and optimally designed shapes. Steel halls for industry and business are often equipped with heavy production equipment, there is also movement of heavy transport equipment, and the floor carries high pressures from stored goods. While using any type of building, including the industrial halls, it is desirable to make optimal use of the available volume. Sometimes, however, the volume of the building is not used to its full potential by not needing or being able to store goods at the full height of the facility, or internal process lines do not use the full height of the hall throughout their projection. Analysing the need to make optimum use of the building’s space, the idea of a storey building automatically springs to mind. Is it worth building storey steel halls?
Storey in a steel hall
Storey industrial halls can be buildings that have two or more storeys over their entire surface area. However, given the specific nature of the use of such facilities, which are dominated by the heavy vehicle traffic associated with the storage of goods described in the previous section, it is considerably more common for a storey in a steel hall to be constructed only in a certain part of it – the storey in the hall designed in this way is called a mezzanine floor.
Mezzanine floor in a steel hall
A mezzanine floor in a steel hall is often designed as a steel post and beam structure, which can be single or multi-storey. Mezzanine floors, depending on their use and therefore their purpose, can have significantly different load-bearing capacities and finishes. Mezzanine floors can be used, among other things, for stacking of large and awkward components and goods that cannot be stored on traditional racking systems. Mezzanine floors are also used to create additional workstations – there can be production workstations or workstations for logistics, maintenance or machine operations, so that no production and storage space is lost at the floor level. Depending on the intended use, the mezzanine floor of a steel hall can therefore differ in certain fittings. A mezzanine floor requires lighting for the workstations and protection of the free edges with barriers to prevent workers from falling from height. The storage mezzanine, on the other hand, should have free, unprotected edges of the ceiling to act as a loading/unloading ramp so that the stored goods can be stored freely.
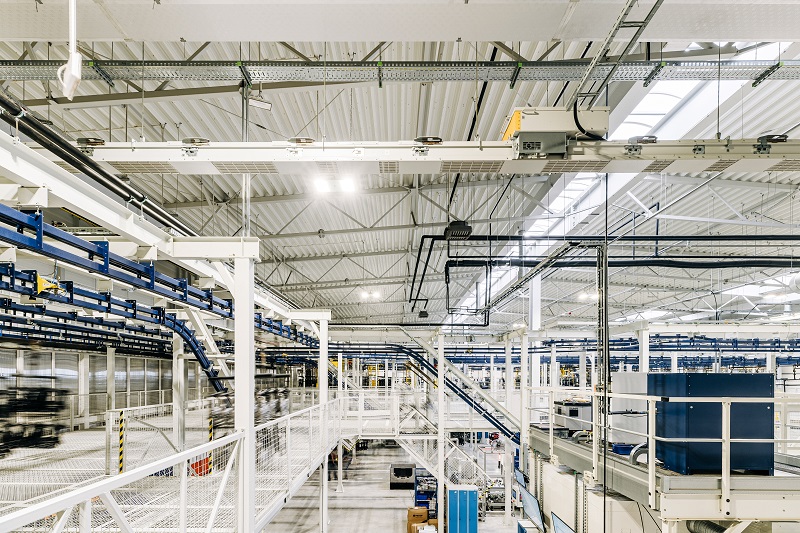
Depending on its intended use, a mezzanine floor can be designed as a structure completely independent of the main building structure, or it can use the main structural columns of the hall to which it adjoins – in either case, its location and shape should be considered in the design of the entire building. It should also be borne in mind that mezzanine floors customarily do not form a partition between the space of the hall and that created by the storey. Sometimes production processes require absolute sterility, in other cases, the stored goods are highly flammable or toxic. For these reasons, among others, a very common alternative used to achieve the desired workstation density in an industrial hall are storey staff and office facilities integrated into the hall.
Staff and office facilities integrated into the hall – advantages and drawbacks
Another example of a storey in a steel hall is the staff and office part of the building, where it is integrated into the body of the whole building. This hall space, separated from the storage area, allows for creating hygienic and suitably equipped permanent or temporary workstations. Staff and office facilities are also often equipped, in the case of production processes, with appropriate access areas, for example, the quality control department, or appropriately designed chambers providing an interface between the “grey” and “clean” areas for production requiring a sufficiently high level of hygiene (e.g. food production, cosmetics production, etc.).
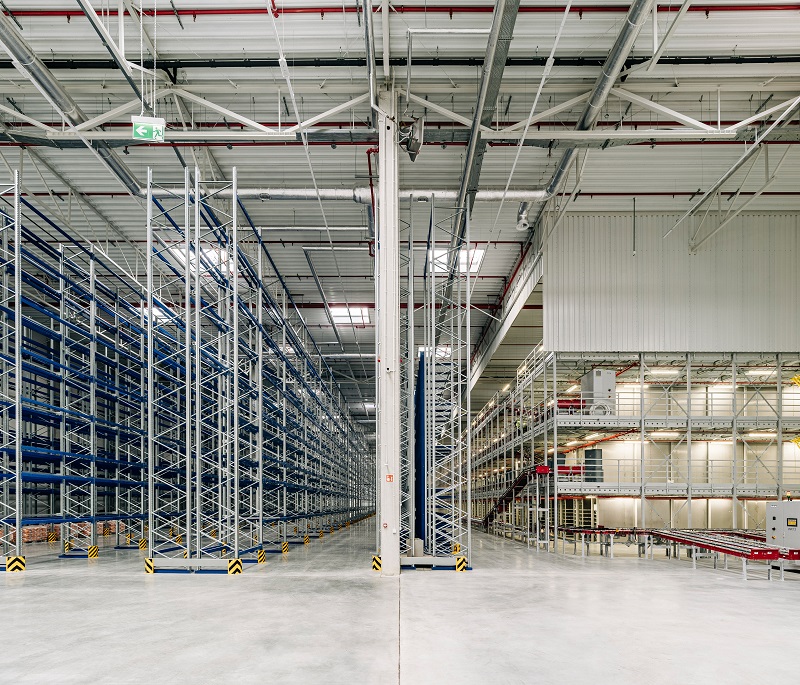
However, note that the staff and office area usually constitutes a separate fire zone and is therefore subject to the relevant requirements of the separate fire regulations. For reasons of fire protection, it is therefore very common for a storey office area to be built with reinforced concrete or reinforced concrete and brick technology, as these materials are naturally more resistant to the adverse effects of temperature rise from a progressive fire.
How many storeys can a steel hall have?
There are various answers depending on how literally one takes the above question. As a rule of thumb, a typical steel hall used for rack storage or production processes has one above-ground floor – directly on the ground. In situations discussed above, where there is a need to compact certain working zones from a process or logistical point of view, a steel hall may have more than one floor in a particular zone.
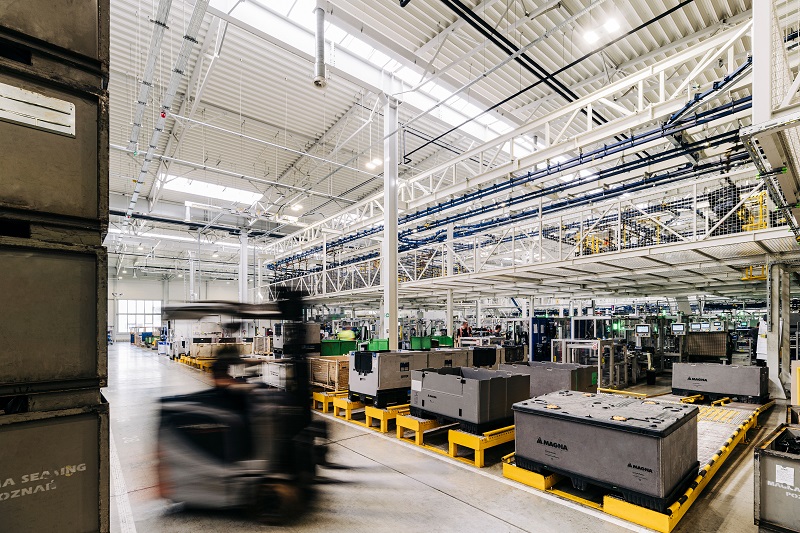
Is it worth building a storey steel hall?
The construction of steel hall elements such as mezzanine floors and storey staff and office facilities is often the case when the available space on the project land is significantly limited. The decision to build a storey steel hall must be supported by an appropriate economic analysis in relation to existing alternatives. When building a storey steel hall , it is important that an experienced general contractor analyses the existing possibilities and, based on their experience, advise on the right solutions to optimise, both logistically and economically, the form and shape that the hall should ultimately take.