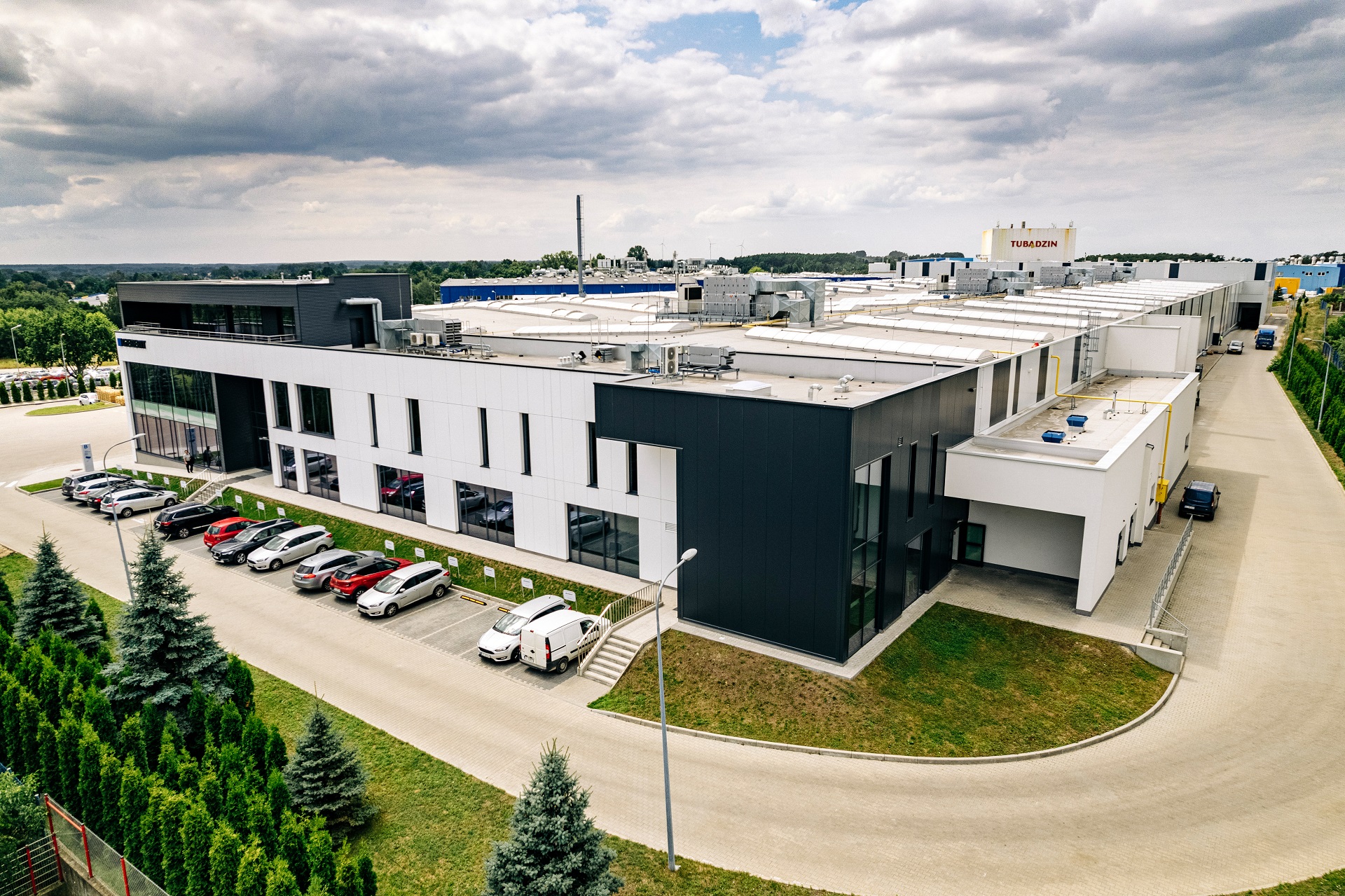
The need to ensure that a building is adequately ventilated is a common state of knowledge – this can be achieved by answering the question if you like being in a stuffy room. In the following text we will answer whether ventilation in industrial facilities is obligatory.
Large-volume buildings, which include, among others, logistics halls, warehouse halls or industrial halls require adequate ventilation for their proper functioning. Although it is not a feature that distinguishes this group of buildings from single- and multi-family houses or public buildings, ventilation in a storage hall is often a complex environmental engineering process if only because of the considerably larger volume of air accumulated inside this type of building. Determining the basic functional parameters of the hall and identifying the processes taking place in it are key guidelines for the proper design of the ventilation system and the selection of equipment.
Does the production hall need to have ventilation?
Production halls require the provision of a ventilation system that is meticulously adapted to the specific production processes taking place in them. The appropriate air exchange rate should be taken into account not only because of separate regulations related to the provision of fresh air at permanent or temporary workplaces, but also the need to ensure the removal of dangerous gases, fumes resulting from production processes or the removal of pollen and other volatile pollutants.
Does the warehouse need to have ventilation?
Warehouses also cannot function properly without an efficient ventilation system. Storage halls and logistics halls are facilities in which the right temperature and air humidity must also prevail. Depending on the specifications and the degree of automation of the storage and handling processes, the ventilation in the warehouse hall must also provide the right amount of fresh air for the people at the workstations (involved in, among other things, the handling and storage of goods). Moreover, even in highly automated facilities, there is a need to control the relative humidity of the air that changes with the external atmospheric conditions, which leads to the conclusion that ventilation in a steel hall is an obligatory system regardless of its purpose and degree of automation. However, it is crucial to correctly identify the needs in terms of the amount of cyclable air and the presence of possible contaminants that appear in the building during the processes taking place in it, which need to be neutralised and removed.
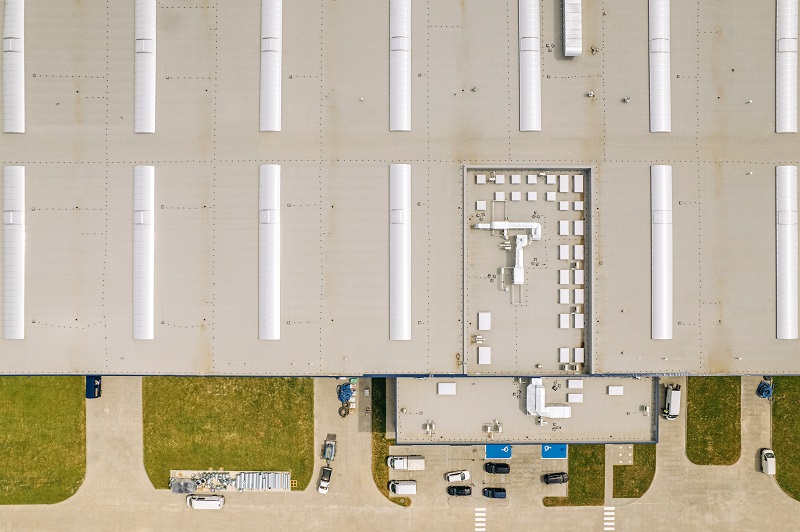
Types of ventilation in logistics halls and warehouses
Breakdown by type of circulation forcing
Ventilation in a building can be implemented in two ways from the point of view of the air exchange process. The spontaneous movement of air without the intervention of additional equipment, which leads to the escape of warm masses through ventilation ducts (located in the roof) and the inflow of air through natural or forced air leaks in the building (door, gate and window seals) is called natural ventilation. The second, and by far the more popular, method of ventilation in a warehouse these days is to force the air to circulate mechanically. Mechanical ventilation in warehouses is provided by the forced expulsion of used air (mechanical exhaust ventilation), the forced introduction of fresh air (mechanical supply ventilation) or a combination of both, i.e. forced intake and exhaust ventilation.Units, very often mounted on the roof of the building called air handling units, are used for the movement of air distributed through ventilation ducts around the building. The steel hall air handling unit has a role according to the type of ventilation designed and is then called a supply, extract or supply/exhaust air handling unit, respectively.
Breakdown by area of operation
Ventilation in industrial facilities can also be classified in terms of its area of operation in the facility. There is a distinction between zone ventilation systems, which provide adequate air exchange and purification for a specific area or even an entire building. The use of zone ventilation is advantageous when the ventilation intensity requirements and the types of pollutants contained in the air in a given area of the hall are uniform. Where hazardous substances are released into the air locally during production processes, targeted and concentrated intensified local ventilation is often used. Local ventilation is usually ensured by stacks and exhaust ducts, and zones where hazardous or explosive substances are vented are usually enclosed with internal partitions isolating the room from the rest of the building – then, in addition to the exhaust ducts, there is a need for an intensive fresh air supply, which must be provided for the balance of air masses between the intake and extraction. In addition, in areas with airborne substances that are extremely hazardous to health, it happens to design an airtight sluice with controlled negative pressure (so that in the event of any leaks, the air is forced in the direction of the “contaminated” room and does not allow a situation of pressure equalisation outside, contaminating the “clean” rooms).
Division by energy recovery
When mechanical ventilation is used in a steel hall, heat can be exchanged between the air being exhausted and that entering the building. Such a process is called recuperation. Buildings in the classical approach (with the exception of cold stores and freezers) require adequate heating during the winter. The process of ventilation and therefore the ejection of used warm air in such facilities is one of the largest components of heat energy loss. Air that is supplied from outside at a significantly lower temperature requires a large expenditure of energy to bring it to the desired temperature and the process of ejecting the ‘used’ air therefore involves the aforementioned cooling of the building. Recuperation in forced ventilation involves introducing ejected (warm) air and fresh (cold) air into the recuperator – in this process, in classical terms, these streams do not mix, but thermal energy is transferred. The end result is the ejection of used air at a lower temperature than the temperature inside the hall, and the introduction of fresh air from outside warmer than the outside temperature. It should also be noted that the recuperation process can only take place effectively with a forced ventilation solution, particularly supply and exhaust ventilation. (Recuperation is not used in natural ventilation, where the movement of air masses, warm and cold, in both directions in the same place cannot be naturally achieved).
Will recuperation guarantee the right temperature in summer?
Indeed, it is also important to note the need to ensure the right temperature inside the building, which in general must not be too low, but also too high in summer. Forced ventilation with recuperation helps reduce the heating costs of a building in winter, however, it will not guarantee an adequately low temperature in summer when we throw out the warm used air and take in comparably warm air from outside.
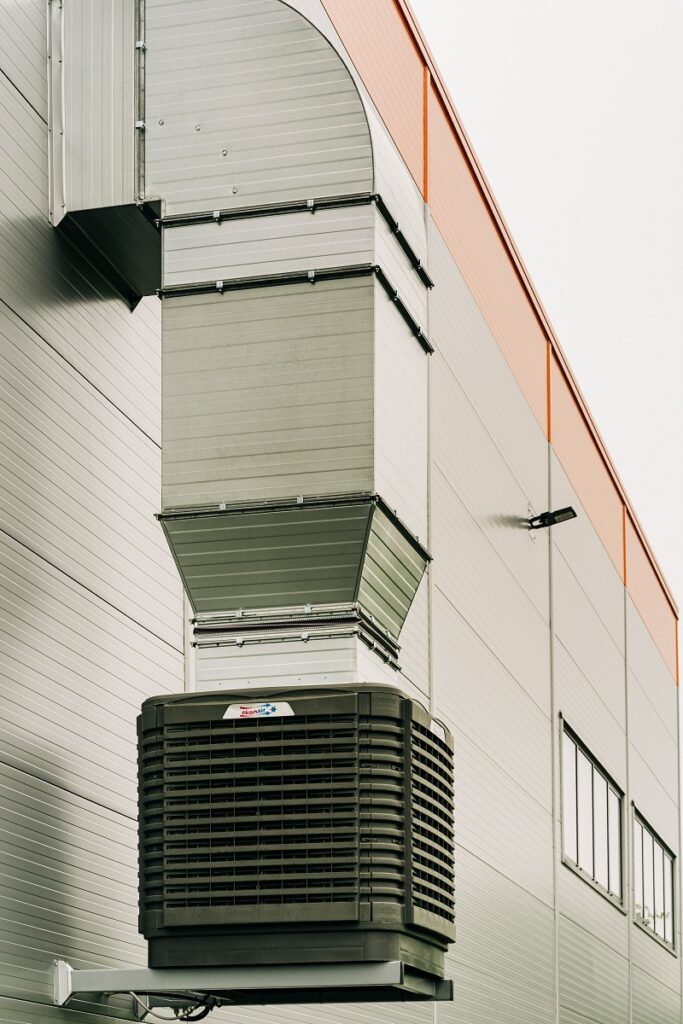
Ventilation of halls – what are the current requirements?
The basic requirements for a warehouse ventilation scheme are to ensure an adequate air exchange rate. Whenever the ‘multiplicity’ of air exchange is referred to, we are referring to the volume of the room ventilated in a certain unit of time – customarily one hour. So when talking about a 2-fold air exchange in a room measuring 10 m × 10 m in plan and 3 m high, the exchange of six hundred cubic metres of air per hour (600 m3/h) is required.
Air exchange rates for different production processes are usually provided by separate regulations. Examples of air change rates are shown below:
- Non-air-conditioned storage hall: 1.5 exchanges per hour
- Performing work involving cyanides for heat treatment of metals, their solutions and mixtures: 10-fold air exchange per hour
- Storage facility for chemicals used in electroplating processes: 10-fold air exchange per hour
- Cotton mills: 5 to 15 times the air change rate per hour
The ventilation for an industrial hall, logistics hall or warehouse should be considered with all identifiable data related to the way the facility is used. The aspects discussed in this guide are only an introduction to the subject of ventilation and refrigeration in environmental engineering. Among other things, this guide does not address the issue of allowing recirculation of stale air and mixing it with fresh air, the problem of cleaning the air from pollen and other airborne pollutants. Only the need for adequate dehumidification and humidification of the air or the use of more specialised technical solutions in terms of storing and working with hazardous substances is mentioned here. The most important thing in choosing the right way to ventilate a steel hall is to entrust this task to an experienced general contractor who will advise and identify the most appropriate solutions with regard to both technical, hygienic and economic aspects as early as the design and build technical consultancy stage.