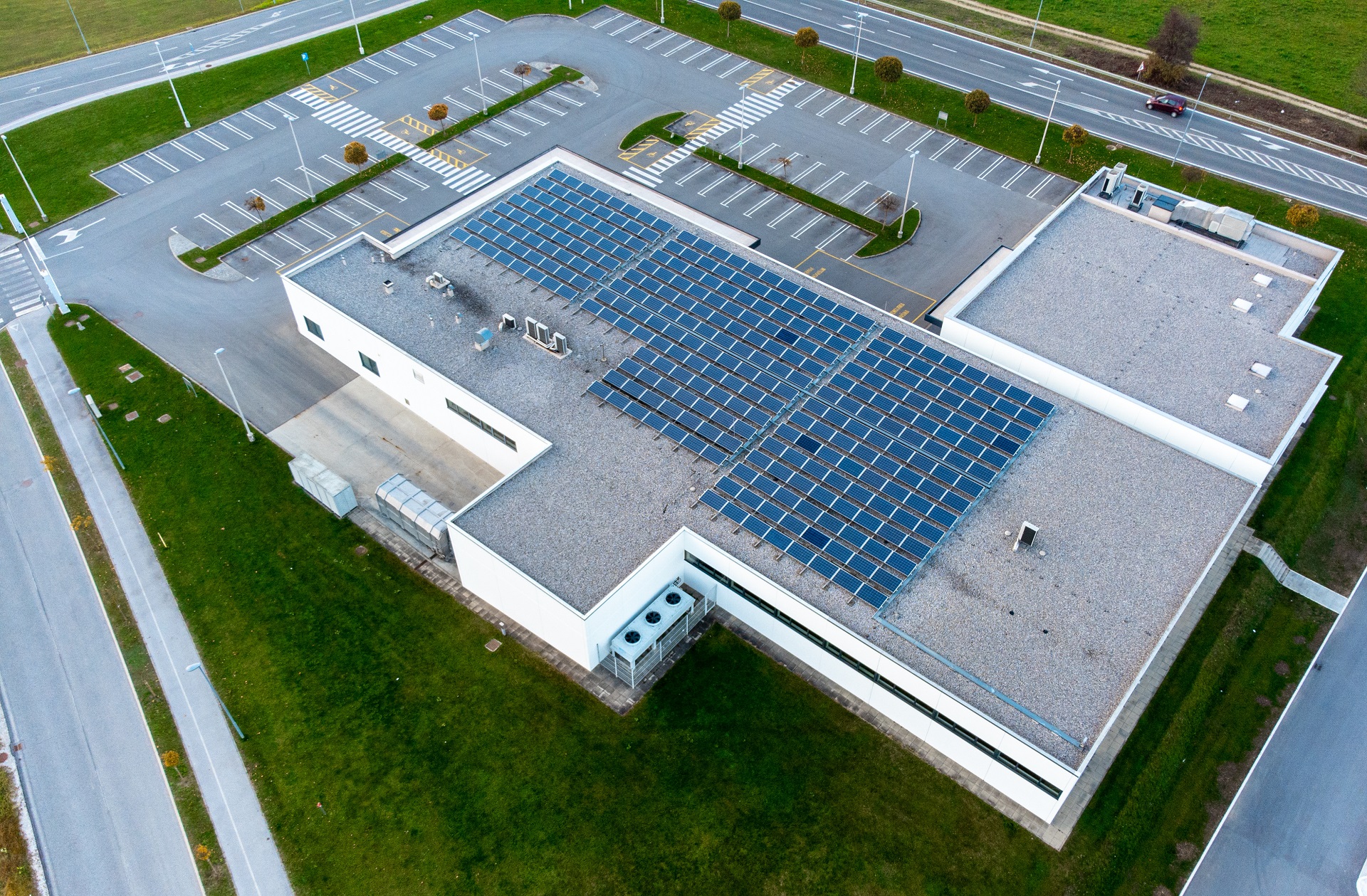
The huge demand for industrial space in Poland in recent years has meant that the number of large-space halls being built in our country has grown at an unprecedented rate. In 2022 alone, the stock of modern warehousing and manufacturing space expanded by as much as 4.4 million sq m. – at the end of last year, total stock reached 28.3 million sq m. Note that, as demand increased, so did investors’ and tenants’ requirements for the facilities under construction – their design, construction technology, but above all the need for environmentally friendly solutions. We discuss the latest trends in the construction of large area halls.
Ecology is a word that – in the context of modern industrial construction – is used in all cases. Alongside social responsibility and corporate governance, this first pillar of companies’ ESG strategies has undoubtedly become a signpost for designers of such facilities. And no wonder – the increasing degradation of the environment, including air pollution, and the turbulence in the energy market that has been accompanying us for the past year, resulting in high prices for conventional energy sources, mean that the building industry of our time must be energy-efficient and environmentally friendly. What more?
Energy efficiency in buildings – an obligation, not a whim
Buildings are responsible for 37% of global greenhouse gas emissions, so at their scale they have huge potential to improve these infamous statistics. And although the solution to the problem seems simpler than ever today, as it is fully available (we are talking about modern building materials), it proves much more difficult in practice. Why? In our surroundings, there are still a huge number of large halls, but also other buildings with very low energy efficiency. They therefore require comprehensive thermal upgrade – insulating the walls and roof and switching from traditional to renewable energy sources.
These requirements are fortunately being met by an increasing number of newly built industrial, residential or public buildings that fit in with the green trend. The use of energy-efficient and environmentally friendly materials in the construction process of large-scale halls, as well as the use of modern window and door joinery, significantly reduces energy losses, contributing to a lower demand for energy. And this is absolutely fundamental if we are talking about improving the energy performance of buildings. What else influences it?
Use of renewable energy sources
The last year has been a challenging one for the construction industry, though for many others too. The energy crisis, rising inflation, constantly rising material and energy prices – all of these have had an impact on the accelerated energy transition process. And a key role in it is played today by photovoltaic systems which, until recently, were mainly associated with single-family houses, are now also increasingly found on the roof of large-scale production or logistics facilities.
Building large-scale halls with PV panels allows the building to be powered by green energy, and this brings several benefits. Firstly, it has a positive impact on the environment by reducing CO2 emissions. Secondly, the use of broad-based eco solutions is beneficial to the perception of the company by its business environment. And thirdly, in an era of very high prices for conventionally sourced energy, ‘free’ solar energy makes it possible to significantly reduce ongoing building maintenance costs. It is worth mentioning that, with conventional energy prices in place over the past year, the payback time for photovoltaic systems has noticeably shortened. But renewable energy sources are not the only solutions used in the construction of large-scale halls – heat pumps are also increasingly being used.
Intelligent management systems and LED lighting in a large hall
In addition to low energy consumption, modern large-scale halls have recently become distinct for one more thing: the intelligent management of the many processes that take place in them. What is it about? It is about BMS systems, which can perform the important function of monitoring and controlling heating, ventilation, air conditioning, security systems or access control. Their use allows energy consumption to be optimised, which in turn is a simple way to save money by reducing the operating costs of the facility.
And as far as savings are concerned, it is impossible not to talk about lighting systems, which – along with the aforementioned HVAC systems – are an extremely important item in the electricity bills of warehouses or production halls. Why the high energy consumption? Firstly, from the size of the facilities, which often amount to tens of thousands of square metres each. And secondly, also from the fact that work in them often takes place around the clock, and this requires almost constant light in the rooms. For this reason, modern LED lighting supported by advanced control automation is becoming increasingly common in large production and storage halls. And this one allows you to control the light intensity in different zones of a large hall and also gives you the possibility to switch off the lighting where it is not needed at the moment.
It is also worth mentioning the luminaries working with the addressable DALI system, which, in combination with motion detectors, presence detectors and external light intensity detectors, make it possible to significantly reduce electricity consumption.
Construction of modern large-scale halls
Although current trends in the construction of large-scale halls are very much linked to the sustainability, this does not mean that changes on other levels are not taking place. We are talking about the function that warehouses are increasingly performing today. Until recently, such facilities were only used for the storage and warehousing of goods. Yes, they had a small social space for employees (cloakroom, dining room, toilets), but this was usually separated from the area of the warehouse itself, making it less comfortable. This has changed a lot in recent years.
Today, modern warehouses often have a representative, highly functional and comfortable office space that acts as a business back office for all the company’s operations. It is not uncommon for it to be located in a separate building, made using a different technology to the warehouse. All with the aim of making it more employee-friendly and simply prettier. It is well lit (due to large glazing), equipped with air conditioning and finished with high standard materials. The layout of the premises in the office building accompanying the warehouse is also no different from typical office buildings located in city centres – they usually have a representative reception area, comfortable conference rooms and are arranged according to the individual needs of the tenant. However, it is not only the interiors of large-scale halls that are changing. The façade – until recently only in shades of grey – is also becoming a distinctive feature. Today, developers and investors are increasingly opting for façade panels in a variety of colours, making industrial buildings look much friendlier and blend in better with their surroundings.
Modern industrial facilities today are very different buildings to those constructed just a few years ago. General contractors responsible for the construction of large-scale halls must therefore demonstrate a much wider range of competences than in the past – they should offer investors a building design service, also demonstrate experience in dealing with formal matters, knowledge of the latest architectural trends and knowledge of innovative, ecological solutions. And this is a high bar set by investors.