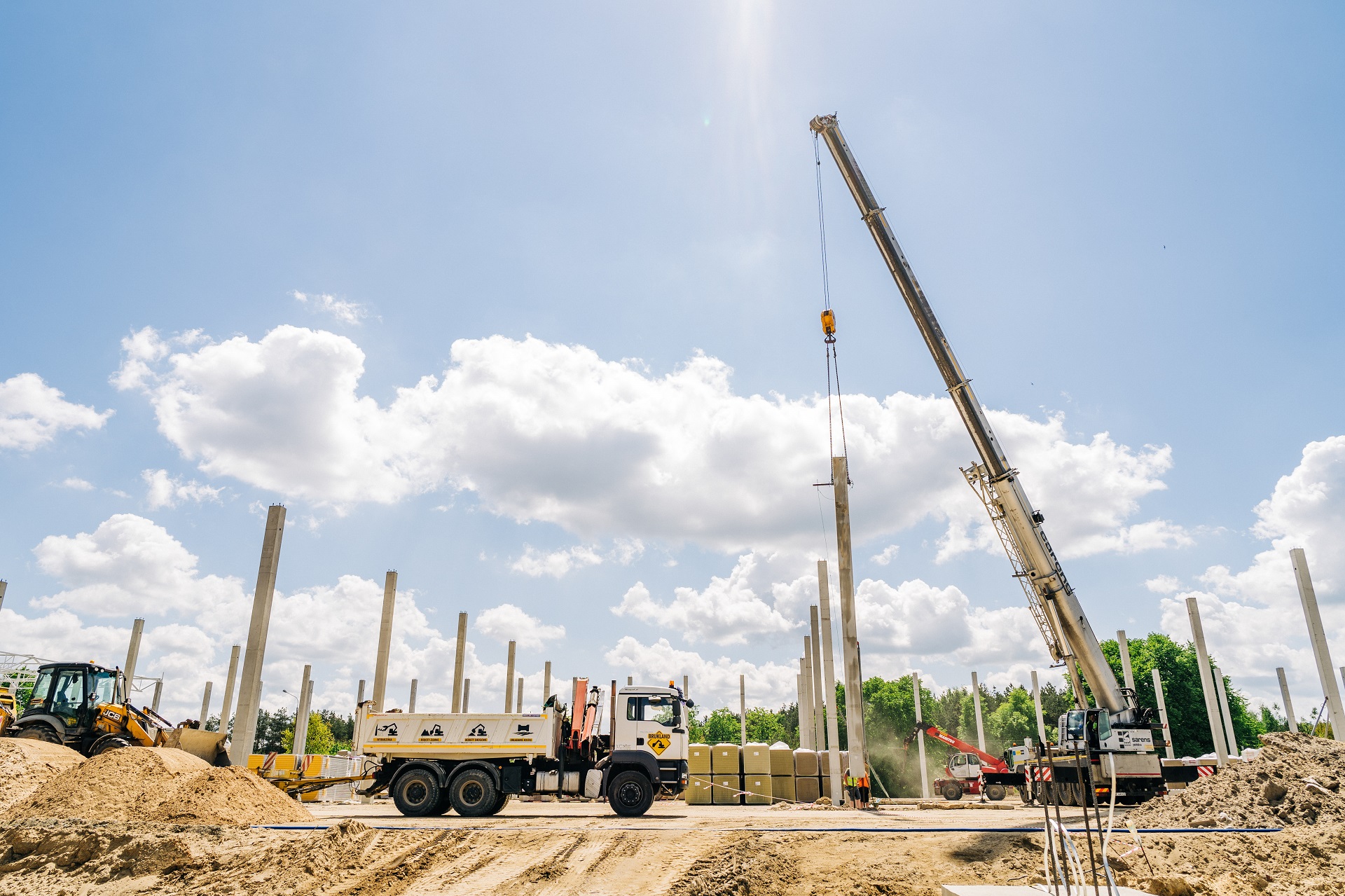
Steel warehouses are indispensable both, for companies that operate in the broad sense industry, and need space to store raw materials, semi-finished goods and products, and for logistics service providers. What needs to be considered when designing and building storage facilities? Why is it so important in this case to adapt the hall to the investor’s needs?
Storage facilities are classified by taking into account various criteria. The most common is the height criterion that refers to the height of the goods stored. According to this classification, low storage halls, where goods are stored at a maximum height of up to 4.2 m, medium storage halls, where goods are stored at a maximum height of 4.2 to 7.2 m, and high storage halls, from 7.2 m to as much as 40 m, are considered. A similar criterion applies also to the height of the facility from the floor level. A distinction is made between low structures (including warehouses) – up to 12 m, medium-high – from over 12 m to 25 m, high – from over 25 m to 55 m, and high-rise structures – above 55 m. Warehouses are also divided according to their construction: open, semi-open, closed, and according to the functions performed, e.g. transhipment, container, customs or delivery.
The construction of a warehouse should therefore take into account the purpose of the facility, which affects both the size and height of the building, the standard of finish used and the internal transport solutions adopted.
What to look for when designing storage facilities?
The construction of a hall is an investment for years, so the design of the facility should be adapted to the investor’s needs. The size and location of the plot is important, and so are the goods to be stored and the storage mode. The design and construction of a warehouse intended for storing goods on pallets is slightly different from that with storage racks. Additional thermal requirements are also important, for example, if the products stored require a constant temperature to be maintained, this must be taken into account at the design stage.
Storage facilities should provide optimal space for storing goods. They should also have traffic routes that allow free handling. The width and location of the paths will depend on the size of the parcels or pallets being handled.
Moreover, the design of the warehouse must also take into account the static and dynamic loads on the floor. If it is not properly calculated, premature damage to the floor may occur and this will generate unwanted cost.
What else is important at the design stage? Optimisation of the superstructure, selection of the type of wall cladding and roofing, number and location of loading docks, doors and gates. The design should also include fire protection elements ensuring the safe use of the hall, ventilation and heating systems, as well as the installation of skylights, windows and other solutions allowing access to sunlight.
If necessary, the design should also allow for the possibility of rebuilding or expanding the warehouse in the future.
Construction of a storage hall
The construction of a storage hall requires an expert approach of the building contractor. It is about finding a contractor who can advise on the optimum solutions both for storing goods and for heating or lighting the building. What systems are used at the construction phase of a hall will not only affect the cost of construction, but also of its operation.
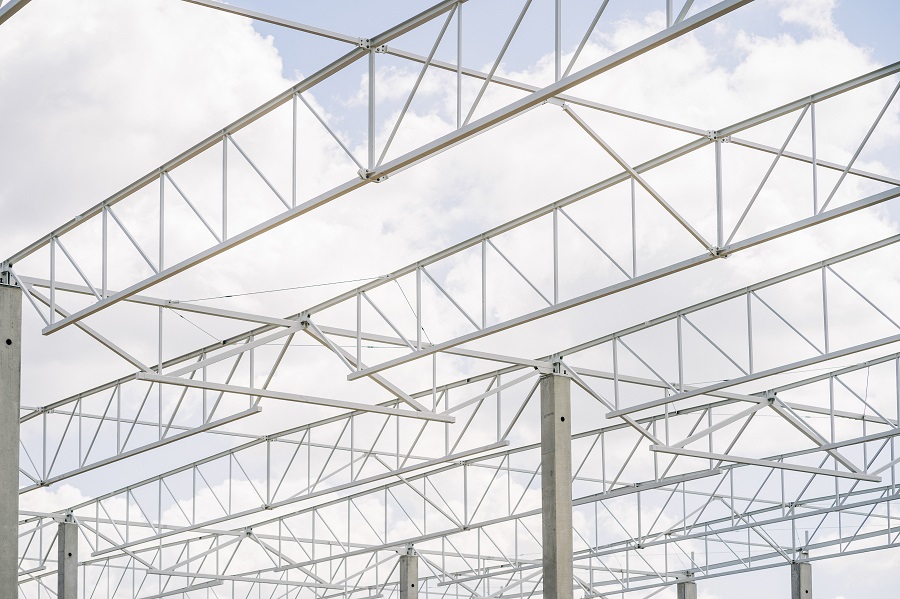
Having a hall completed by a general contractor usually proves to be the best option. General contracting includes obtaining the required permits, carrying out the construction work and supervising the project milestones until the facility is ready for use.
How much does it cost to build a hall? The cost of construction depends, among other things, on the location of the building plot, the land properties, the type of structure, its width and height, the designed load, the internal utilities, connections to external systems, the number of loading ramps and docks, windows, skylights, finishes and many other elements.