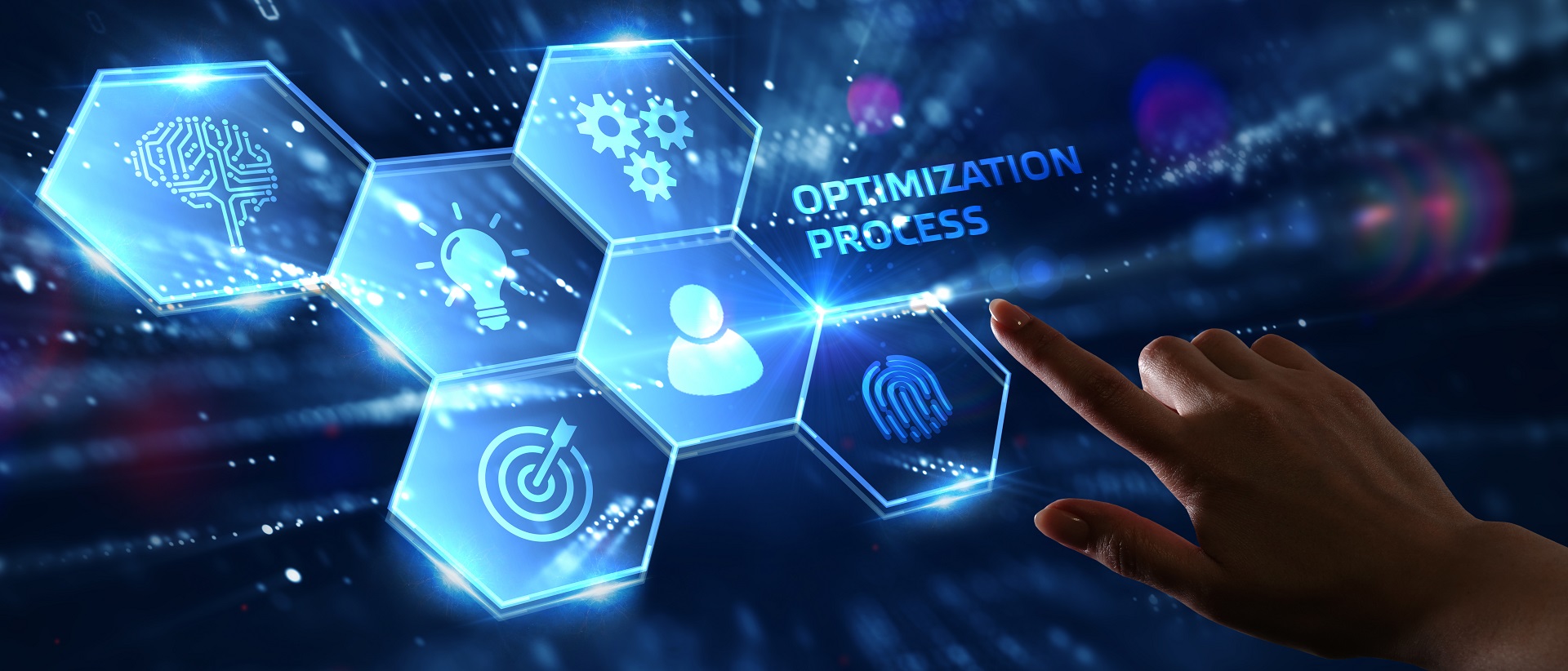
Industrial construction is undoubtedly a domain that requires the use of highly specialised technologies, equipment and materials. This makes construction processes expensive and building materials are used in very large quantities. Given the complexity of the whole project, it is therefore easy to incur large, often excessive cost. It is hence important to optimise the facility construction cost.
Optimisation is understood as a method of determining the so-called optimal solution from the point of view of the adopted objective function. An optimal solution is the one that minimises or maximises the adopted objective function. There can be many objective functions and, in the optimisation task, the extremes of many functions can be sought simultaneously (multi-criteria optimisation). The following will further focus on the single-criteria optimisation of hall construction cost, in which the objective function aims to minimise the cost incurred, assuming that certain boundary conditions are met, such as utility functions or more generally “investor expectations”. Some components and characteristics of steel halls that can be adjusted in order to optimise construction cost, and thus come closer to an optimal solution (i.e. the minimum of our objective function – cost incurred), are explained. While in theoretical analyses, the optimisation is often related to the search for an exact solution based on analytical formulas, in the case of industrial hall design, the optimisation boils down to an iterative search for solutions approaching the extreme being sought. Precisely because optimising a hall construction cost is partly an iterative task, it is advisable to turn to a company with extensive experience in the construction of industrial facilities, as the knowledge acquired with experience allows a better “starting point” to be selected in the iterative search for the optimal solution. As is well known, a common problem is the inability to find an optimal solution because of a poorly chosen starting point.
Proper geometry of the primary structure
The industrial hall can be optimised due to the structural solutions used. The first step in optimising hall construction cost is to choose the right primary load-bearing structure in relation to the purpose of the building. For single or multi-aisle steel halls, where the span between naves does not exceed 20 m and the height is 10 m, it is usually advisable to design them with steel plate girders. The conscious design of sheet metal structures, including the correct design of connections between frame members, supported by appropriate technical expertise, leads to a certain distribution of forces in the structural system. Knowing the distribution and course of the internal forces, plate frames can be designed as sections with variable web depth (tapered sections) so that the structure has high bearing capacity and stiffness only where it needs it – at the locations of high forces. Accordingly, the profiles are lower and, at the same time, lighter in places where there are lower forces. As a result of this design, less steel is used to make sheet metal frames, which leads to lower fabrication cost. On the contrary, note that in warehouse halls, where it is important to achieve large structural spans (large spacing of columns – more than 20 m) due to the layout of the space, it is worth considering the construction of truss girders instead of sheet metal girders. Due to the small number of load-bearing elements in relation to the voids, the trusses are characterised by excellent rigidity and adequate load-bearing capacity. For this reason they are recommended for long-span structures. Note also that truss structures are considered optimal when they are sufficiently high in relation to their span, so for example, it is likely that a 20.0 m truss should be higher than about 1.40 m. This has to be considered when planning the construction of a low steel hall in particular.
Use of secondary structure
Another aspect of optimising hall construction cost is the use of other elements accompanying the main structure, whose contribution to the overall safe operation of the structure is necessary, for example, for the possibility of further isolating the interior of the building from the ambient conditions. Steel purlins can be used as an example for steel sheet halls. The plate girders discussed in the previous subsection are structures that exhibit significant stiffness in their plane, however, they are by far weaker in the perpendicular perspective. Steel purlins in steel halls are commonly used not only as a support for the trapezoidal sheeting of the roof, but as a support for the main sheeting frames themselves against loss of overall balance perpendicular to their plane. Correct selection of the steel purlin dimensions and spacing optimises not only the weight of the purlins themselves, but also has a real impact on the weight of the sheet metal structure and the trapezoidal sheet thickness. Thus, an appropriate choice of steel purlins optimises of the cost for the primary structure (sheet metal), the secondary structure (purlins) and the roof sheathing (trapezoidal sheeting).
Another example is the correct choice of trapezoidal plates in truss girder structures. Trapezoidal sheet metal roofing not only allows for thermal insulation and waterproofing of the roof, but can also form a semi-rigid shield in the roof slope causing some stabilising effect on the trusses against the loss of balance.
Considering such beneficial effects of interactions between the primary and secondary elements, and even roof sheathing elements, enables the overall hall construction cost optimisation.
Optimisation of human safety fire protection solutions
For large-area warehouses or production facilities, note that enormous savings can be made at the construction stage by choosing the right fire protection solutions at the design stage.
An important aspect is choosing the right storage height. Above certain storage heights, the fire load per unit area of the building/fire compartment increases and fire protection requirements become more stringent. A sprinkler system is an extremely costly solution. One alternative method of providing adequate fire protection for a facility is to divide smaller parts of the warehouse into separate fire zones each of which does not require a sprinkler system. It is often the case that such division into fire zones proves to be incomparably cheaper than installing a sprinkler system, but this must be considered together with the convenience of use and the logistics of internal handling.
Optimising hall construction cost
There are many options for reducing and optimising hall construction cost available. Not all aspects can be equally mentioned in such a short text. Common to all cost optimisation options is the choice of an experienced contractor who can point important technical aspects affecting the construction cost based on the expertise in the field.
We recommend: Industrial construction – general contracting in construction projects