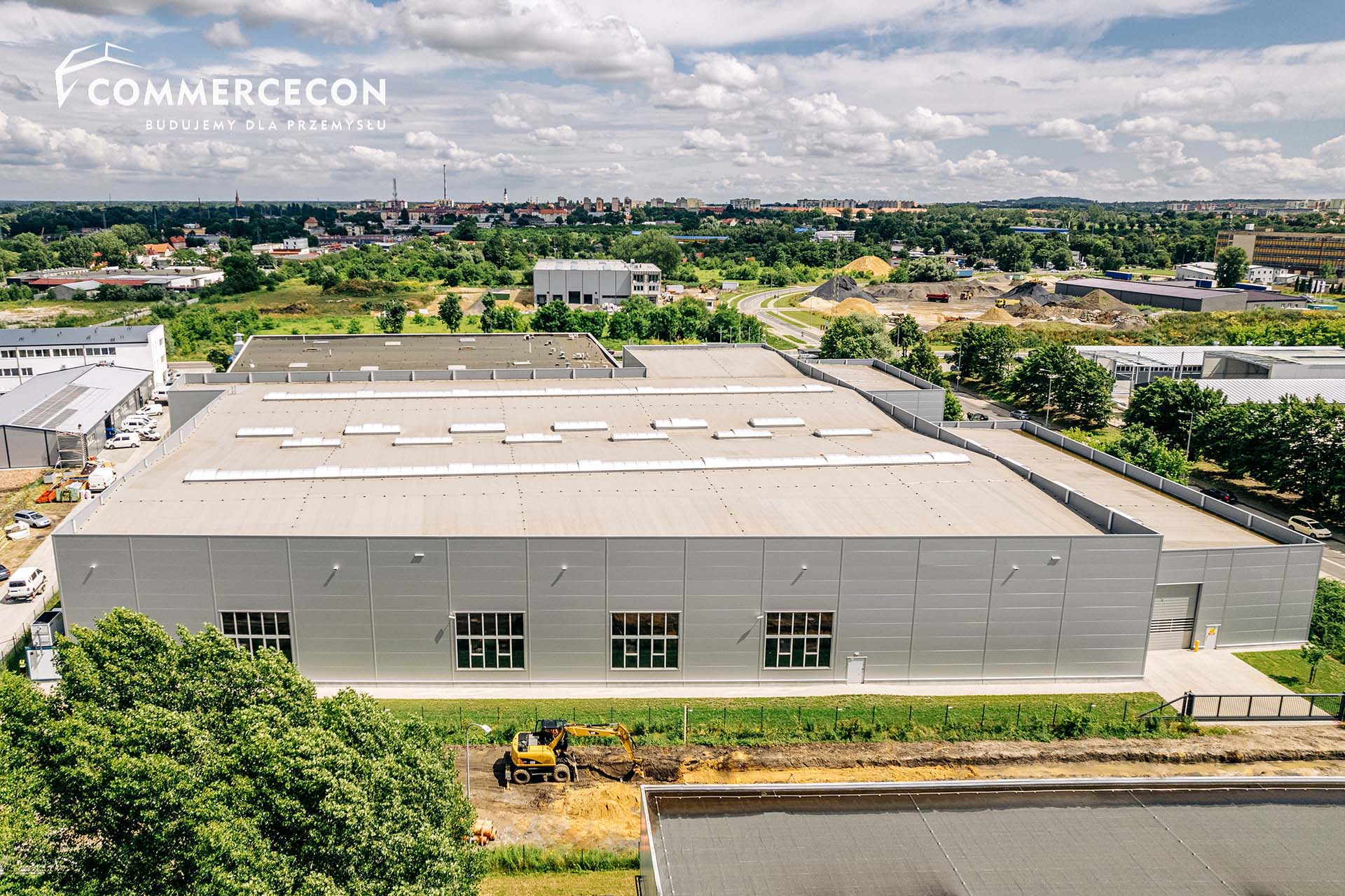
Thick snow cover or water on the roof of an industrial hall can be a serious test to the strength of its structure. And although buildings are designed to cope with the anticipated additional loads, risks cannot be fully foreseen. The solution to that are intelligent roof monitoring systems that provide advance warning of danger. They are increasingly used by general contractors during the construction of modern facilities for the warehouse, manufacturing and retail sectors.
Industrial construction has been booming in recent years. All this is due to the demand for warehouse and production space growing at a very fast pace. Last year, more than 2 million sqm of space was commissioned, and the current year promises to be record-breaking in this respect – for the first half of the year more than 3 million sqm of space under construction is reported. Thus, the total supply of modern industrial and logistics space, which closed at the end of last year at over 20.5 million sq m, will increase significantly this year. Taking into account the construction of buildings for these industries, it can be assumed that this number corresponds to the area of flat roofs created. And such a conclusion that gives much food for thought in the context of safety.
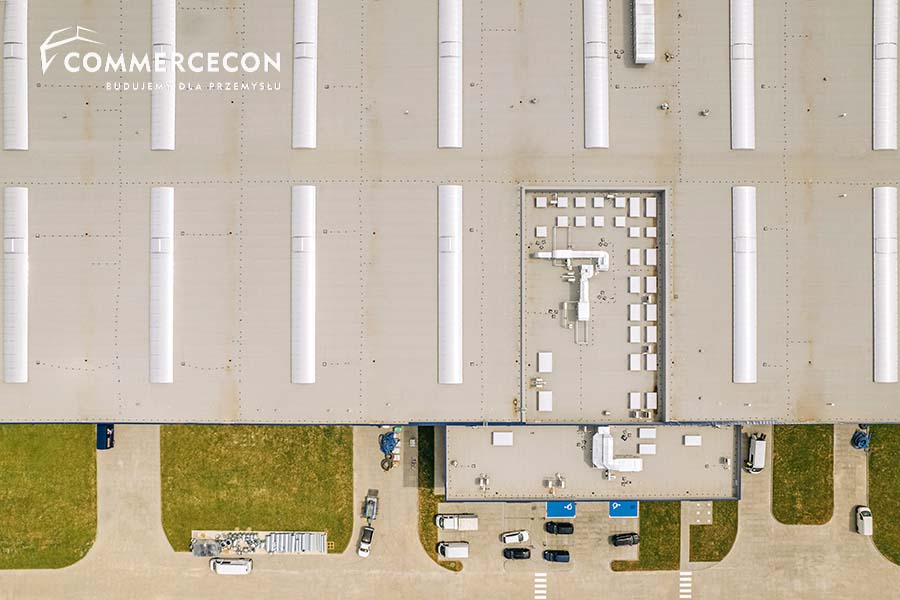
Roof structure and its anticipated loads
One of the key elements of warehouse and industrial halls is the roof which usually consists of two main load-bearing parts: the girders and lattice purlins, and trapezoidal sheet metal as the load-bearing part of the covering. Each element has a different function in the structure. The role of the girders is to collect and transfer loads onto the columns, maintaining the rigidity of the roof, which is subject to various forces during the life of the building. – These is the dead load, but also additional loads from installation of various systems, both suspended under the roof and mounted on its surface, are concerned. This is mainly the technical equipment for the maintenance and PV systems which are increasingly often a partial source of power for industrial facilities according to the sustainable construction principles – explains Marcin Wojcieszek, construction manager at Commercecon, a company that has built more than 270 industrial and logistics facilities with a total area of almost 2 million square meters. Note that these are factors that the building designer is able to anticipate and therefore develop optimal design solutions for.
Risks to roofs from precipitation
The roof is also subjected to loads from precipitation, such as snow, hail or heavy rain, the intensity of which is much more difficult to predict. If these occur intensively or if water drainage from the roof is disturbed it may get overloaded, and its permissible structural deflection is then exceeded. But who can discover that it in the right time, when the roof area often exceeds several hectares? – Certainly not the trained eye of even the most experienced building manager will see this. This is why we have developed the “Intelligent Roof” platform. It efficiently manages the risks of flat roofs and supports large building managers in their safe maintenance. After all, it is difficult to check if the roof drains are clear and the weight of the snow on your own – says Artiom Komardin, co-founder and vice-president of Sense Monitoring. – While the awareness of the dangers of snow on the roof is high, not everyone is aware that in heavy rain, water can pile up above 10 cm which is equivalent to 100 kg/m2 – he explains.
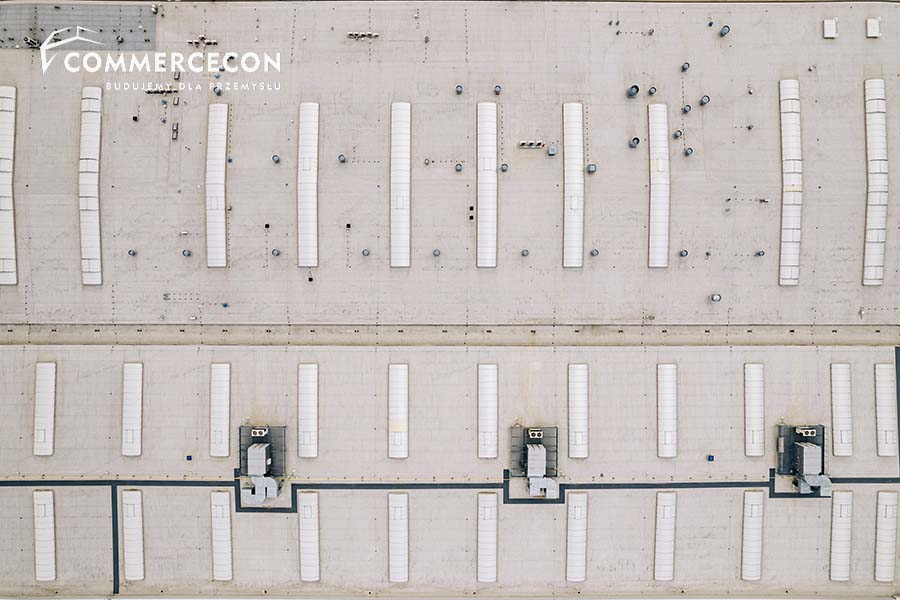
Thanks to the platform, we can control the load the roof (Sense S-One deflection monitoring), as well as measure the water level on the roof (DSW Water Back-up Detection). Both solutions are supported by Weather Alerts (a software function in the Sense Smart Roof app) notifying hall managers of impending hazardous weather events. Early messages increase the alertness of application users and allow appropriate preventive or corrective action to be taken well in advance.
How does the roof load level control platform work?
In the case of Sense S-One deflection monitoring, the system consists of a set of laser sensors and measuring discs, the number of which depends on the size of the roof and the type of its construction. The sensors are fixed at the point of support of the truss, while the measuring disc is fixed at the mid-span of the truss. The deflection measurement, with a 1-milimetre accuracy, is taken at the plane of the roof. The sensors are provided with inclinometers that correct the deflection measurements and continuously measure the verticality of the columns. The solution will prove its worth during intensive snowfall or hailstorms, but also in the case of planned additional loads on the roof, e.g. caused by a photovoltaic system.
The system is also designed to measure the verticality of columns which can change due to uneven foundation settlement. – This can, of course, occur during the life of a building and such systems prove very useful then. However, note that the risk of excessive or uneven foundation settlement patterns can be minimised. As a general contractor for industrial halls, we recommend that our customers carry out a thorough analysis of the geotechnical soil conditions at the construction site. It will allow them to predict the performance characteristics of the building and, consequently, tailor structural solutions accordingly – the Commercecon expert explains.
DSW sensors, on the other hand, are distributed on the roof surface at roof drains where there are no emergency overflows. – They detect abnormal water levels caused by obstructions or clogged drains. Water levels on the roof are measured every 5 minutes with an accuracy of 1 cm. The building manager is notified in real time if the predefined safety levels are exceeded or if there is a prolonged stagnation of water in the vicinity of the gullies, so as to quickly address the problem and have the gullies checked – Artiom Komardin explains.
Both systems operate continuously, immediately warning the application user – with a text message or email – when a certain safety limit is exceeded. What is more, the app collects all the data compiled so far, so the user has constant access to historical readings.
What benefits do building owners get from roof monitoring systems?
The list of benefits is really long, but two aspects are worth noting. The most important one is to ensure the safety of the occupants, but also of the property which can be quite expensive. Modern solutions for the efficient management of flat roof risks, like intelligent building management systems, also help optimise building operating cost, e.g. by avoiding unnecessary and costly snow removal from the roof. – It is worth noting that such an operation always involves the risk of damaging the roof sheathing, services or technical equipment on it. The resulting damage to the sheathing can result leaks and therefore further deterioration of the building. Such damage can be quite expensive to repair – concludes Marcin Wojcieszek.
The “Smart Roof” platform monitors many industrial halls, including those completed by Commercecon who, as a general contractor, has recently delivered a 40,000-sq m production and warehouse facility for one of the market’s leading developers.
See also the “Industrial hall roofing” article