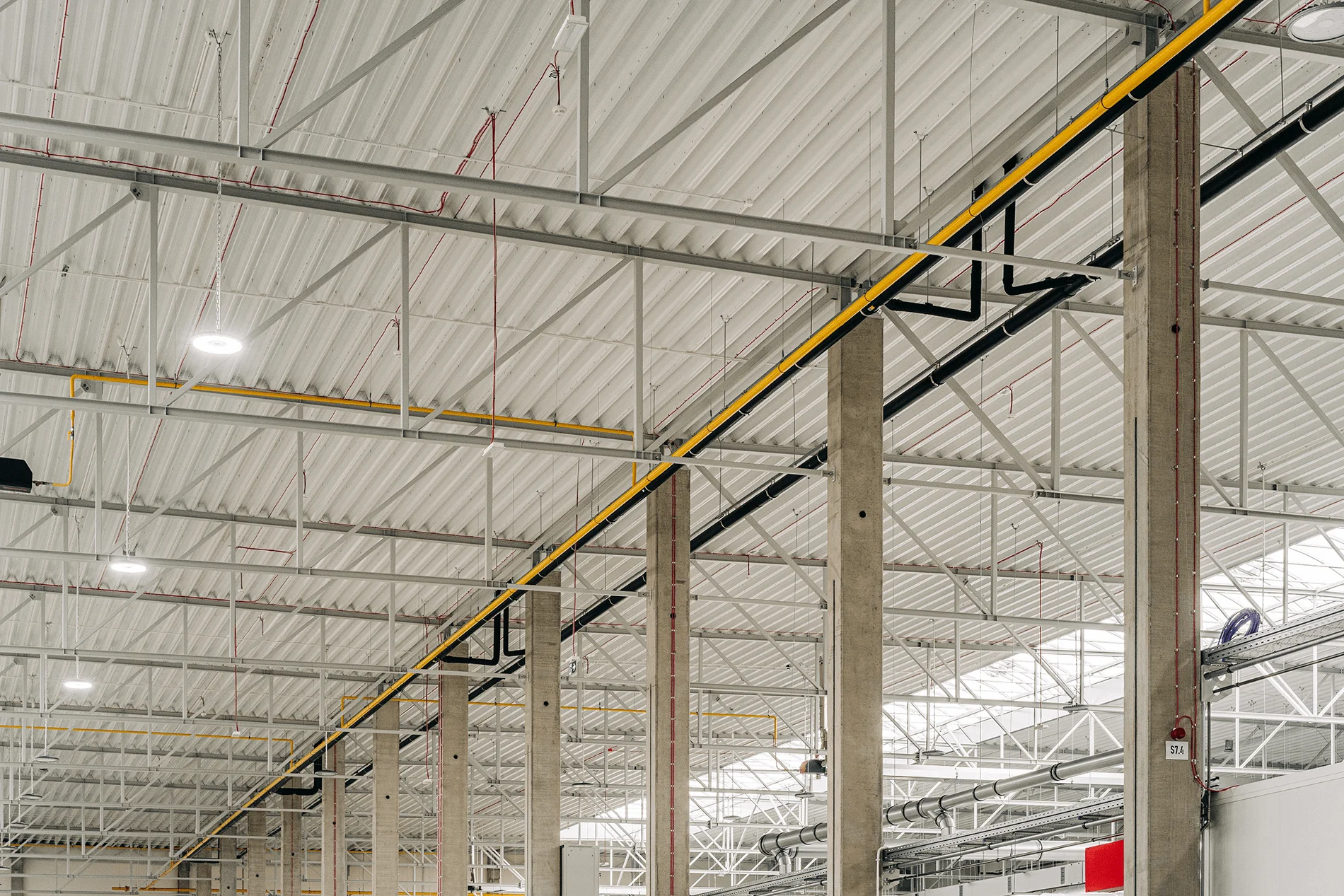
The roof of any building, irrespective of its size, is an extremely important element which, together with the walls, forms the enclosure of the internal volume of the building, protecting it from weather conditions. The roof, as the part of a building that rests above the heads of its occupants, is commonly perceived by the public as one of the most important structural elements of a building. This belief is by all means correct, and in the case of industrial facilities, it is sometimes a difficult technical issue. The roof of a steel hall can be solved in many ways. In the following text, we will take a closer look at both the types of roof in a steel hall and the technical and functional aspects that affect its final form. The advantages and disadvantages of each possible solution will be cited, as well as the technical and performance aspects that often determine the choice of the right solution.
Types of steel hall roof construction
There are two main types of steel hall roof structure – sheet and truss design. In the sheet design, the main structural elements are the beams, which customarily have an I-section shape, made of flat plates that are joined by welding. I-section roof beams formed by welding plates are known as the plate girders or solid-wall girders. The repetitive frames of the hall structure, whose main roof elements are precisely the plate girders, are normally spaced at distances of 5 to 7.6 metres. The smaller spacing makes communication more difficult due to the narrow opening left for the entrance gates. In contrast, the upper limitation is dictated by the need for wall cladding and the design of the secondary roof structure (perpendicular to the main girders) discussed later in the text. Plate girders can reach extremely different spans, from quite small ones of around 6-8 metres to very large ones, exceeding up to 70 metres. Such a considerable difference in the spans achieved by plate girders has consequences in terms of a significant increase in their overall height, the thickness of the steel plates from which they are made and the need for additional bracing for such high and narrow (and therefore flaccid) roof supports. Very often, therefore, plate girders with very large spans are relatively heavy and therefore not very economical. The plate girders, which form the so-called primary (and therefore main and most important) roof structure, interact with the roof beams, commonly referred to as purlins, which are located perpendicular to them. Roof purlins for steel halls may be designed as mill products (I-sections), but more often, due to the need to reduce the dead weight (and therefore the price) of the structure, the purlins are designed from cold-formed sections. The purlins made from cold-formed section usually take the shape of the letter Z (commonly Z sections), and C and G sections are used in the specific areas of the steel hall roof, and their thickness usually does not exceed 2.5 – 3.0 mm. The purlins provide direct support for the steel hall roof sheathing, which is made from trapezoidal sheets ranging 0.7 to 1.5 mm in thickness. The roof purlins are spaced quite densely in the case of a metal plate roof: every 1 – 2 metres as they also act as additional bracing for the roof and, in particular, protect the main metal plate girders from loss of stability. The end result is that, thanks to the dense purlin spacing, the girder is adequately protected against the undesirable effects of loss of stability (which increases its design load-bearing capacity, reduces its dead weight, and thus reduces the cost) and the roof sheet is quite low and thin and so correspondingly cheaper.
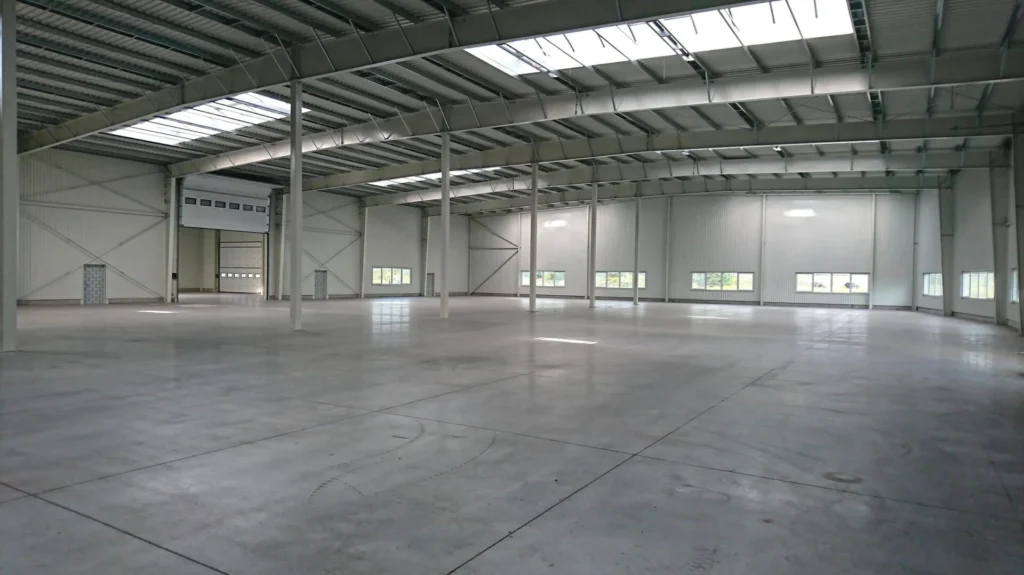
The second structural solution for the steel hall roof is the truss structure. A truss is a system of interconnected bars that, compared to a plate girders, are many times thinner and slimmer. A typical roof truss is a flat member, meaning that all its bars form a single plane. Roof trusses are made up of a bottom chord and an upper chord, which are connected to each other by bars commonly referred to as trusses. The points of contact between the struts and the bottom and top chords are adapted to the specific project, just as the dimensions and type of each bar profile are individually adapted to the internal force patterns within it. It is a very common practice in the design of truss roofs to adopt a scheme in which lattice girders spaced no more than 6.0 m apart provide direct support for the trapezoidal sheeting. In this case, trapezoidal sheeting is expected to have a higher load-bearing capacity, so it is often correspondingly thicker and higher (e.g. 130 mm), but this avoids the need to add cold-formed purlin structures, leading to rational use of the material.
Full-wall girder or truss girder?
Truss steel hall roofs can achieve very large spans, while at the same time very often having a lower dead weight than a full-wall girder construction. Another advantage is that it is easier to guide services suspended on the roof, as truss girders are openwork elements and therefore have numerous large voids that allow installations to be guided between the trussing elements. In the case of solid-wall girders, it is of course possible to design process openings, but each of these is a natural weakening of the solid-wall girder, so the number of these openings should be well thought out, as should their location and size. It is often the case that work on individual discipline designs for ventilation, electrical systems, roof drainage and others is preceded by the design of the main structure, so it is sometimes difficult to foresee the appropriate location and dimensions of the aforementioned penetrations in the structure. From this point of view, truss girders allow considerably more freedom in the positioning of suspended systems under the roof and, as a result, to design them more optimally.
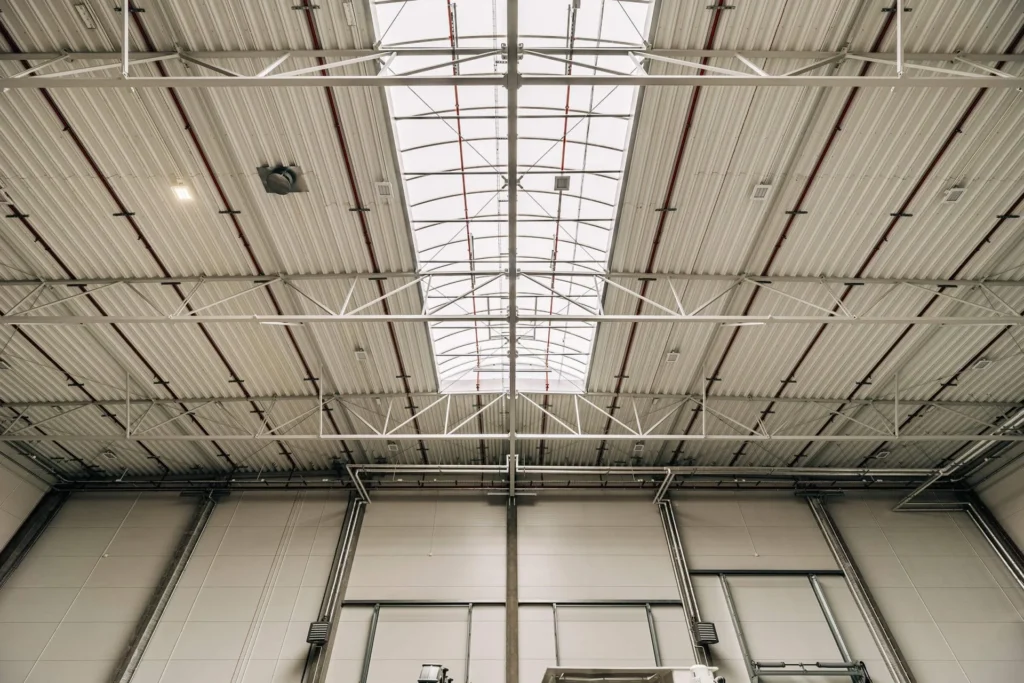
However, truss structures are not without their drawbacks. One of the main ones undoubtedly includes their size. A truss girder relative to a solid-wall girder of the same length is usually taller (up to two to three times). This is an important aspect for warehouses and especially for high-bay warehouses, for which the storage of goods takes place in racking systems that reach almost to the underside of the roof structure. When the roof structure is made of truss girders, the usable height of the hall is reduced by an additional half metre, one or even two metres, with the result that the volume of the hall is not fully utilised, which proves to be important from the point of view of the costs of operating the facility, in which the desired temperature must be maintained in the partially permanently empty and unused space under the roof.
However, it is not only the utilitarian aspects that determine the choice of construction type. A very important aspect in choosing the right solution is the correct combination of loads on the steel hall roof, taking into account, among other things, environmental influences, technological loads but also the insulation of the hall roof.
Steel hall roof layers
A steel hall roof is not only a structure that holds the weight of snow, withstands wind pressure or protects against rainfall. The roofing of the steel hall is equally important. Moreover, it also affects the structure itself and its shape. Among other things, the roof has a thermal insulation role. The choice of thermal insulation for the roof of a steel hall is an important factor from many points of view. The first thing to consider is that the thermal insulation materials offered on the market differ in their dead weight. Materials such as mineral wool, which has a density of 60 to 150 kg/m3 (roofing wool slabs), are available and widely used, but also materials such as polystyrene or PIR (polyisocyanurate), which are much lighter and have a density of 15 to 30 kg/m3. Note that lighter insulation does not always mean cheaper and lighter construction. For steel hall roof structures, it happens that a very lightweight roof structure, on which little load rests, experiences a tearing effect from the wind, for which it has to be additionally reinforced and secured, increasing its weight as a result. Oddly enough, a scenario in which heavier insulation, or a thicker layer of insulation, will make the weight of the roof structure lower, is also possible. Thus, the roof covering of a steel hall can have a real impact on its overall weight.
The roof covering of a steel hall is also related to fire protection, and the choice of thermal insulation material must meet the requirements of the relevant fire resistance regulations depending on the fire resistance class of the building and its components.
The waterproofing of the steel hall roof is usually made of PVC membranes, the outer layer of which is UV-resistant to ensure adequate durability. Alternatively, waterproofing with felt and bitumen compounds is also an option. Both solutions (PVC and felt) are acceptable and practically interchangeable. However, it is important to bear in mind that roofing felt and PVC membrane have different surface roughness – they offer different resistance to water run-off. For roofs designed for membrane application, it is sufficient to ensure a roof pitch of no less than 2%, while for the felt it is a good idea to maintain a minimum roof pitch of 5%. It can be seen that the choice of roof waterproofing affects the overall height of the building (or vice versa – for a given overall height, the usable height decreases) and for long-span structures, for which the distance between the ridge and valley (the highest and lowest points of the roof) is large, the influence is correspondingly greater. Finally, it is only worth adding that these solutions should not be combined, that is, the roof should not be waterproofed with PVC membrane and bitumen at the same time, as the compounds contained in the paper and bitumen strongly degrade the PVC membrane material.
Which solution to choose?
Choosing the right roof covering for a steel hall is a complex issue with many aspects. The right technical solution depends not only on the building geometry and the structural spans, but also on the location, which determines the environmental loads, the building equipment, which defines the installation loads, separate fire protection regulations and additional equipment such as a PV system on the roof, for which the relevant expert or insurance company will set additional requirements for the steel hall roof layers.
Are you interested in this topic? Read the article Industrial hall roofing
Commercecon projects completed
An example of a steel hall with solid-wall roof rafters is the Długopolanka mineral water bottling plant in Stara Łomnica. The two-bay hall structure was designed as a combination of variable-height solid-wall transoms supported by cold-formed (Z) purlins, with trapezoidal plate as the roof sheathing. The spacing of the main frames is 7.30 m and the total height of the hall is over 11 m. Despite a significant structural span of 2 × 30 m, a very low roof steel structure height of around 1.35 m at the highest point has been achieved thanks to the sheet metal girder solution.
An example of a steel hall with lattice roof girders is the Hatrans hall in Łódź. The roof structure is designed as a two-bay structure with widely spaced internal columns (every second internal column). The lattice purlins spanning over 19 metres (19.10 m) are approximately 2.0 m high. Every other pair of trusses coming together in the centre line of the hall is supported on columns, and every other pair is supported on a lattice stringer with an equivalent overall height and a resulting structural span of 12.00 m (2 × 6.00 m). Due to the joint deformation of the purlins and stringers under load, the deflections of the structure had to be strongly limited. Steel trusses perform better in this role, which retain very high rigidity (low deflection) with very low steel consumption, which is why they have been used for this building.