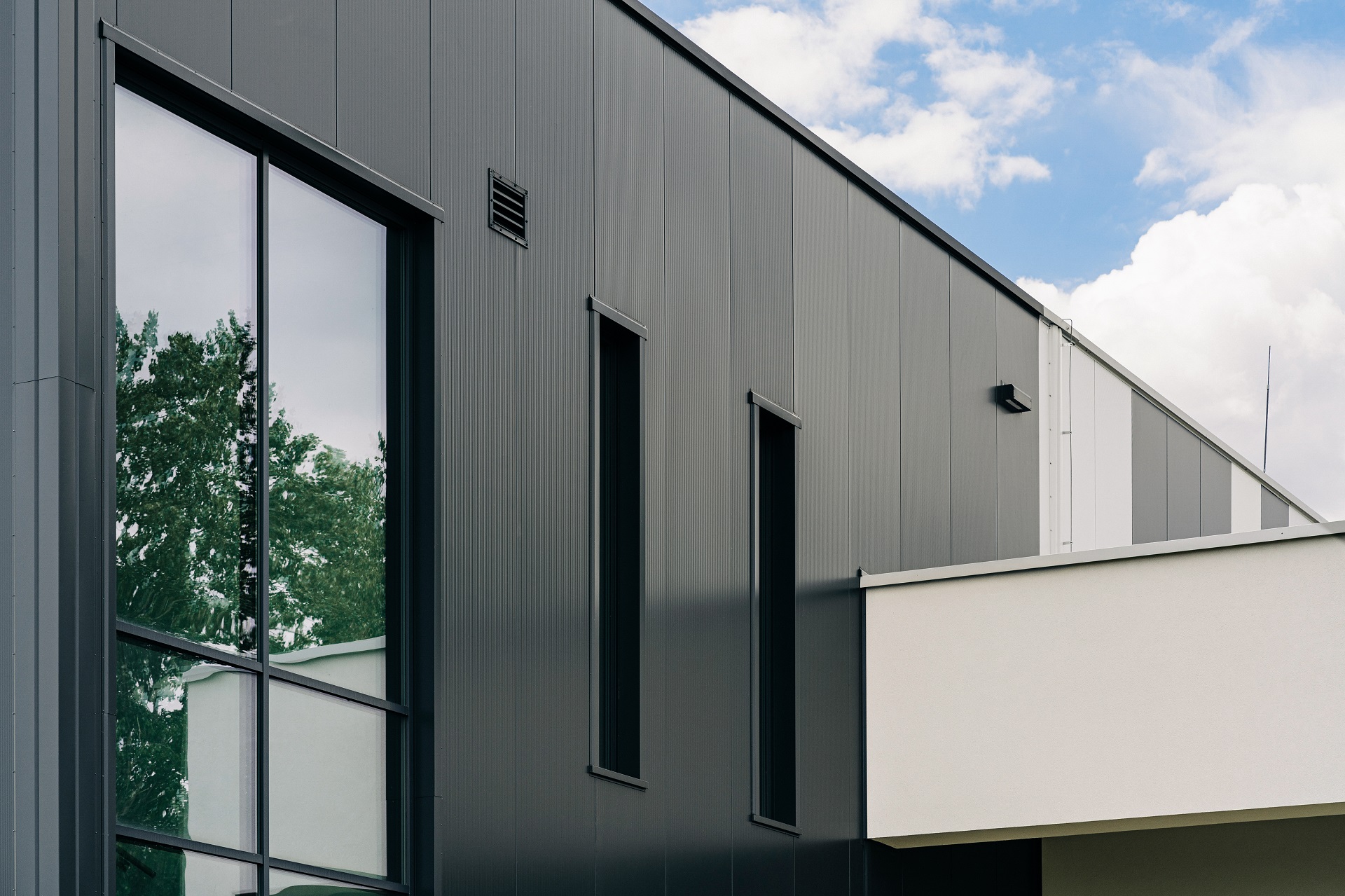
The construction of new production hall structures, industrial facilities and warehouses requires the use of proven technology. This article gives an overview of solutions available on the market that allow you to design and build robust and economical buildings. You will see how steel hall cladding, walls and other parts of industrial buildings can be built.
The market for building materials that can be used for steel hall cladding has developed over the last 20 years to provide adequate insulation from external conditions, aesthetics and functionality as economically as possible. This direction has been set by large-scale facilities the number of which has grown rapidly in the domestic market in the recent years. The interest in building new industrial facilities is constantly growing, so it is important to know what the steel hall cladding should look like, what technology should be used to erect the walls and finish the surfaces.
Steel hall and wall cladding – the most common technologies and materials
Economic reasons and the growing needs of investors have meant that building solutions have become increasingly ergonomic. This can be seen in the speed of assembly, the ease of transport and the aesthetics of the surfaces produced. Today, the sandwich panel is the undisputed leader of materials for steel hall cladding. In many ways, it seems to be the ideal solution, but is it really always the right one to use? Find out about other material solutions available on the market for hall cladding.
1. Sheet-wool-sheet design
Trapezoidal sheeting for walls has been known for decades. Solutions based on cold-formed steel profile technology emerged in our country in the early 1990s. The load-bearing part of the walls was a steel transom with “Z” profiles. The roof covering of a steel hall built using this technology has good insulation properties. The outer sheet constitutes a kind of barrier against external conditions, which is effectively supported by filling the spaces between the “Z” profiles with mineral wool. A sheet of the inner wall and a vapour barrier closes the whole system. As a result, this solution provides good thermal insulation.
The main advantages of the sheet-wool design include the flexibility in adjusting thermal insulation levels and ease of maintenance. Replacing damaged sheets does not require dismantling of the adjacent ones. Increased labour intensity can be a disadvantage, while the relatively limited possibilities of automated assembly carry the risk of higher so-called labour cost.
2. Steel tray with mineral wool – trapezoidal sheet metal
Almost the most popular technique a dozen years ago, today it is gradually losing its popularity, but it still has many advantages. It is used for both large and medium-sized facilities. The most important structural elements of this model are the steel trays with mineral wool, the trapezoidal sheets for the walls and the wind insulation. The rapid cut-off from external conditions speeds up the project completion. A steel transom is no longer needed as the load-bearing part of the wall – it remains only as a support for the joinery and carpentry.
In contrast to the previous method, partial automation of work is possible which improves the process timing. The advantages of this solution also include the design that allows large spans between the columns of the steel hall. Further advantages are the great freedom in shaping the external facade, the possibility of installing steel or aluminium coffers and the use of ventilated facades made of cement-fibre and HPL panels. The disadvantage of trapezoidal sheet for walls is the moderate speed of installation and therefore relatively high cost.
3. Sandwich panels
The third solution is today the undisputed number one when it comes to building hall shells. The sandwich panel combines two aspects: economy and ergonomics. Manufacturers of sandwich panels have put great emphasis in the last ten years on increasing the production capacity of their plants, ensuring the highest quality standards as well as the variety of materials needed to shape the planned steel hall wall surfaces. This offers many possibilities in terms of how the hall shell will look. In principle, the basic characteristics of sandwich panels have not changed much over the years. However, the technical details have changed considerably, e.g. joining methods, structure, material texture, colours and corner types. All of this has meant that the entire industrial construction cycle has accelerated considerably, and the projects can have a more varied architecture.
The most important advantages of using sandwich panels include freedom of installation (vertical, horizontal) and the possibility to choose manufacturers and material parameters. There are many variants of panels which differ e.g. in thickness. A wide range of thermal insulation solutions (e.g. mineral wool, polystyrene foam, PIR foams) that will meet the investor’s requirements is also an advantage. The drawback is a possible damage to the surface or paint finish of the panels, which may require the disassembly of adjacent panels in order to repair or replace the damaged ones. The limitation of the length of a single panel depending on the colour group (the darker the colour, the shorter the panel) and the influence of solar radiation and temperature on deformation are also disadvantages of this solution.
Steel hall cladding – solutions for steel hall walls tailored to the investor’s expectations
All the above solutions have their advantages and disadvantages. So which is the best? Unfortunately, there is no clear answer to that question. This is because everything depends on your individual requirements. This is also why, at Commercecon, we always approach the task independently. We analyse the investor’s objectives needs and establish what they actually need to provide a specific design. We also take into account how existing buildings look so that we can maintain visual and technical consistency.
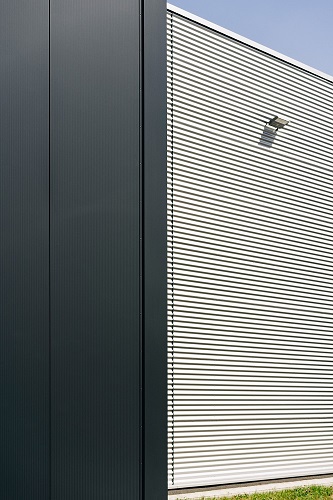
Steel hall cladding and hall walls – design analysis and selection of the best materials
While analysing the design we undertake a number of activities to find the best technology and cost-effective solution. Thermal insulation is a very important factor. The recent years have brought ever increasing tightening of the heat transmission coefficient of partitions. From 2021, it is U=0.20 W/(m2K) for the walls, and U=0.15 W/(m2K) for the roof covering of a steel hall. These parameters have definitely changed the minimum insulation thickness in steel hall walls for the so-called “warm halls” with internal temperatures above 16°C.
When considering a facility, we also take into account the processes that will take place inside. It often turns out that the heat recovery from processes is so high that the hall does not require additional thermal insulation. The statutory reduction of the U-value is naturally linked to the sustainable trend to reduce the energy intensity of new industrial buildings and make them energy neutral.
Aesthetics and finishing in steel hall walls and shells
Another aspect in the selection is the surroundings and the planned appearance of the new facility. Our many years of experience have shown that urban order, colour and appearance preferences are of great importance in the architectural design of new buildings. Many times have we come back to our investors with solutions that may not have been optimal from an economic perspective, but were a continuation of an earlier vision.
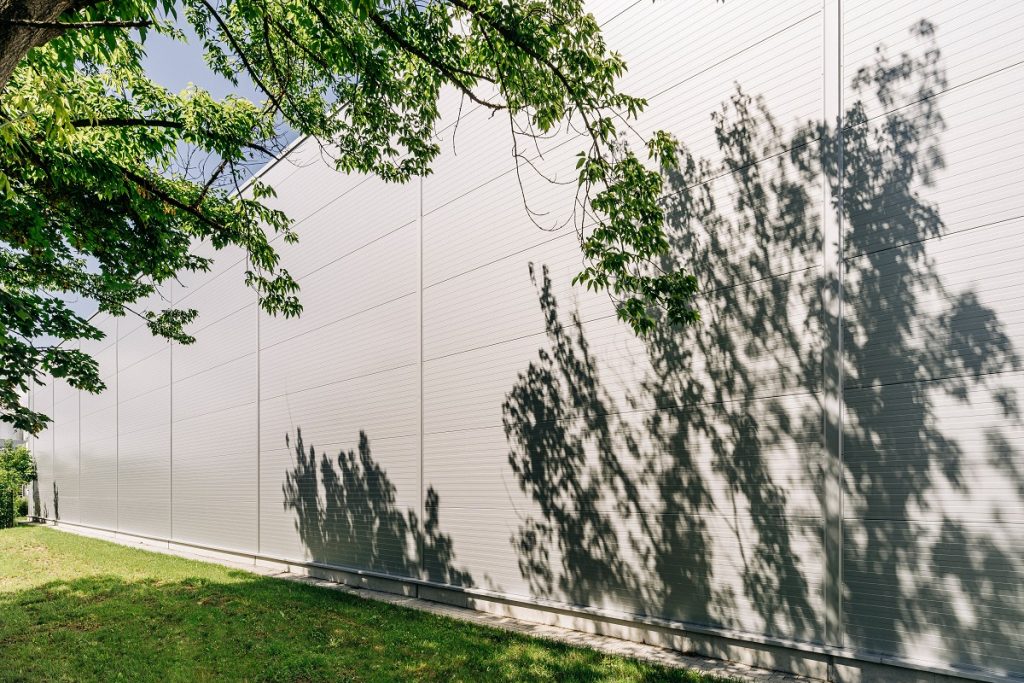
Individual technology and material solutions for steel hall shells, roofs and walls are also selected based on an analysis of the building geometry. The building situation, acoustics and fire protection are other aspects that must be analysed. Nowadays, warehouses and production halls are usually designed with separate office and technical space. The combination of a hall and office space functionality requires the fire performance of adjacent fire zones to be taken into account. The site situation, distance from neighbouring plots and from the street also affects the degree of noise, and therefore the need to reduce its emissions. This also affects the choice of wall cladding and cladding for steel halls. In complex projects, it may turn out that a sandwich panel is not sufficient. A better solution may be to use a traditional layout, based on steel trays with mineral wool and sheet metal on the wall.
It all depends on the individual project. At Commercecon, we will always carefully consider all factors and make the best suggestions.
We are the general contractor for industrial buildings of various purposes, including steel halls, production halls, logistics centres and many others.