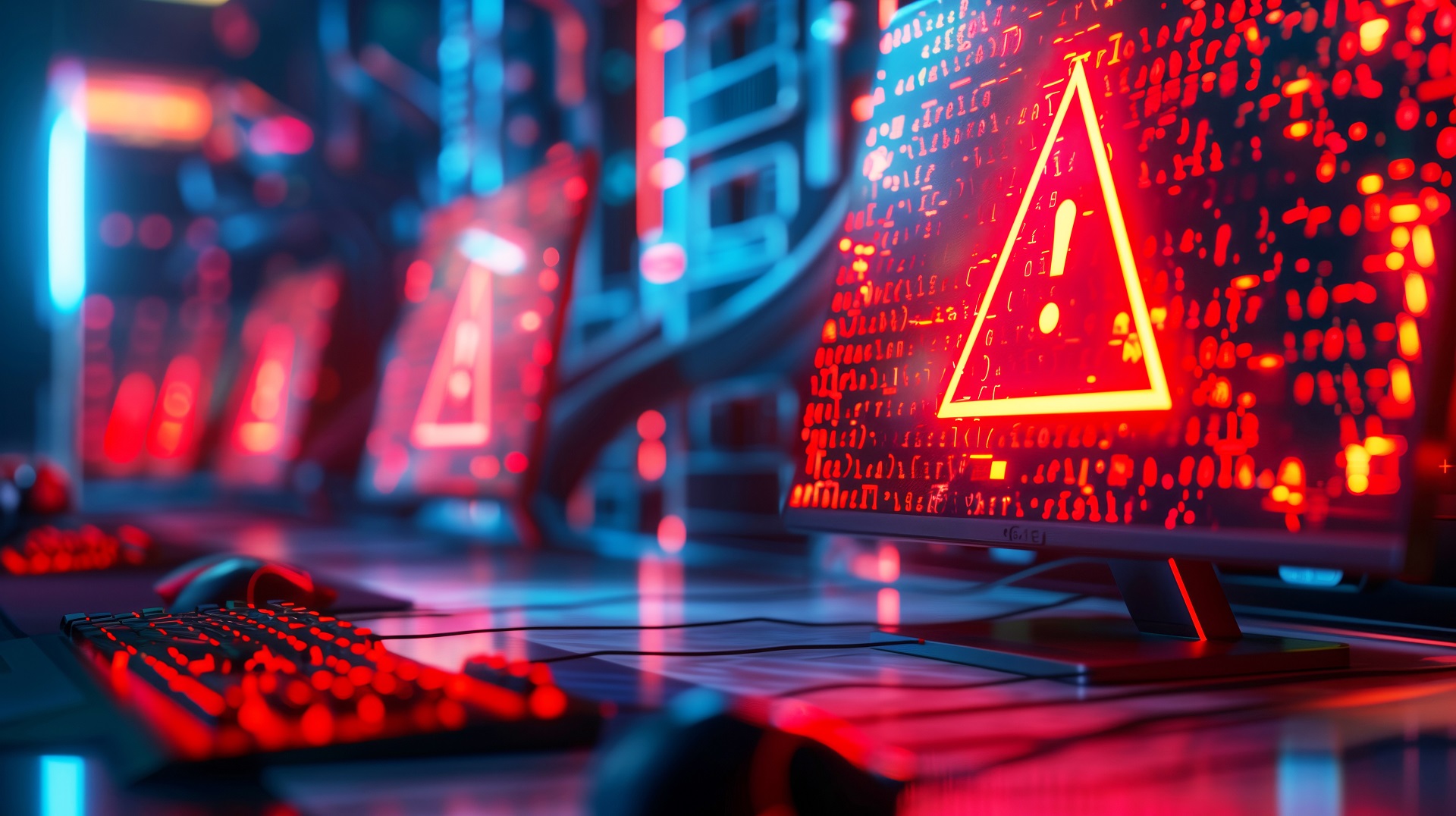
What are the most common mistakes regarding steel hall design?
The construction of a multi-purpose steel hall is a complex multi-stage process that requires a wide range of knowledge for all those involved in the process. Taking any action, in any area of life, is fraught with the risk of making mistakes. Nevertheless, it is important not to make so-called ‘fatal errors’, which can result in loss of property, damage to machinery and equipment, or worse, expose people in the facility or its vicinity to direct loss of life or health. Errors can occur at any stage of the project process (conception, design, execution).
The most common mistakes made when building halls are listed and discussed below.
- Incorrect or inappropriate location of the facility may prove to be one of the initial design flaws. When embarking on a project, the ground conditions in the area of the planned construction should be checked very carefully. Inadequate soil identification can lead to defects in the structure caused, for example, by uneven subsidence.
- A great many errors in the building process are due to a lack of or inadequate coordination of individual disciplines. This usually leads to misplaced openings for installations or collisions between elements of different disciplines (e.g. a beam collides with a process pipeline). Remedying such errors are usually time-consuming and costly.
- Errors at the design stage can be the misinterpretation of building standards. From 1 April 2010, the European Standards (Eurocodes)apply in Poland which have replaced the Polish PN-B standards. This change has led to the incorrect or incompetent application of partial coefficients, on which the safety stock of designed objects is based. This resulted, for example, in underestimating the loads on the structure. It was bad practice for designers to make calculations using Polish and European standards at the same time. This resulted in a reduction in the reliability of the structure, as the already mentioned partial factors had different values in these standards, e.g. for permanent loads the gamma factor was 1.1 (according to PN-B), 1.35 (according to EN).
- A major design error is the inappropriate adoption of structural static schemes. Single-aisle steel halls are designed as portal frames with a rigid corner. The problem arises, for example, when a frame corner, assumed to be ‘rigid’, is constructed as semi-rigid or, even worse, articulated. This alters the internal forces in the frame and can result in a situation where the roof transom has insufficient load-bearing capacity. Another example of errors related to the adopted static scheme is the calculation of the roof purlin as a continuous beam, but realised as a single-span located between the roof rafters. Such a procedure also leads to an adverse change in internal forces.
Another group of errors that can occur during the erection phase of a building are assembly and execution errors, which are described below.
- Errors in the halls also relate to the transport and assembly stage of the steel elements. Improper transport can cause the slender components to warp. This leads to unintended eccentricities that were not included in the design. Careless erection of a steel structure by an inexperienced team can lead to changes in the way the structure performs. The lack of alignment of the columns or running tracks of the cranes results in a change in the rigidity of the structure and leads to increased forces in these components.
- Storage halls and industrial halls are structures whose components are connected by bolts. Improper or faulty tightening of the bolts in a compression joint between two components leads to a significant change in the distribution of forces in these bolts and represents a major construction error. A common error is the incorrect (usually too short) length of bolts or the use of a different class of bolt in the design than that assumed by the designer. This problem is eliminated by using a single bolt class for the whole site or a major part (stage) of the site.
- Another type of error is associated with bolts, namely the incorrect positioning of holes. This results in the steel element not being able to be fitted, which causes interruptions in the installation and requires time-consuming alterations on site.
- Logistics halls are undoubtedly facilities where bar bracing is used to ensure the rigidity and stability of the structure. Note that this type of structural element requires the bars to be pre-tensioned (they cannot ‘hang’ freely). Usually this tension is achieved by so-called turnbuckles or tension nuts. Incorrect installation and lack of bracing tension leads to excessive deformation of the structure and changes in the distribution of internal forces.
- Incorrectly installed flashings lead to leaks, the consequence of which can be the premature appearance of corrosion in the steel structure.
In summary, the construction of halls is a very complex process, during which many errors can occur that affect the reliability of the facility and the comfort of the hall. In the face of the problems and errors mentioned, the role of the design checker and the site manager who verifies the correctness of the solutions applied is particularly important. That is why, at COMMERCECON, we provide a professional approach to your project at every stage.