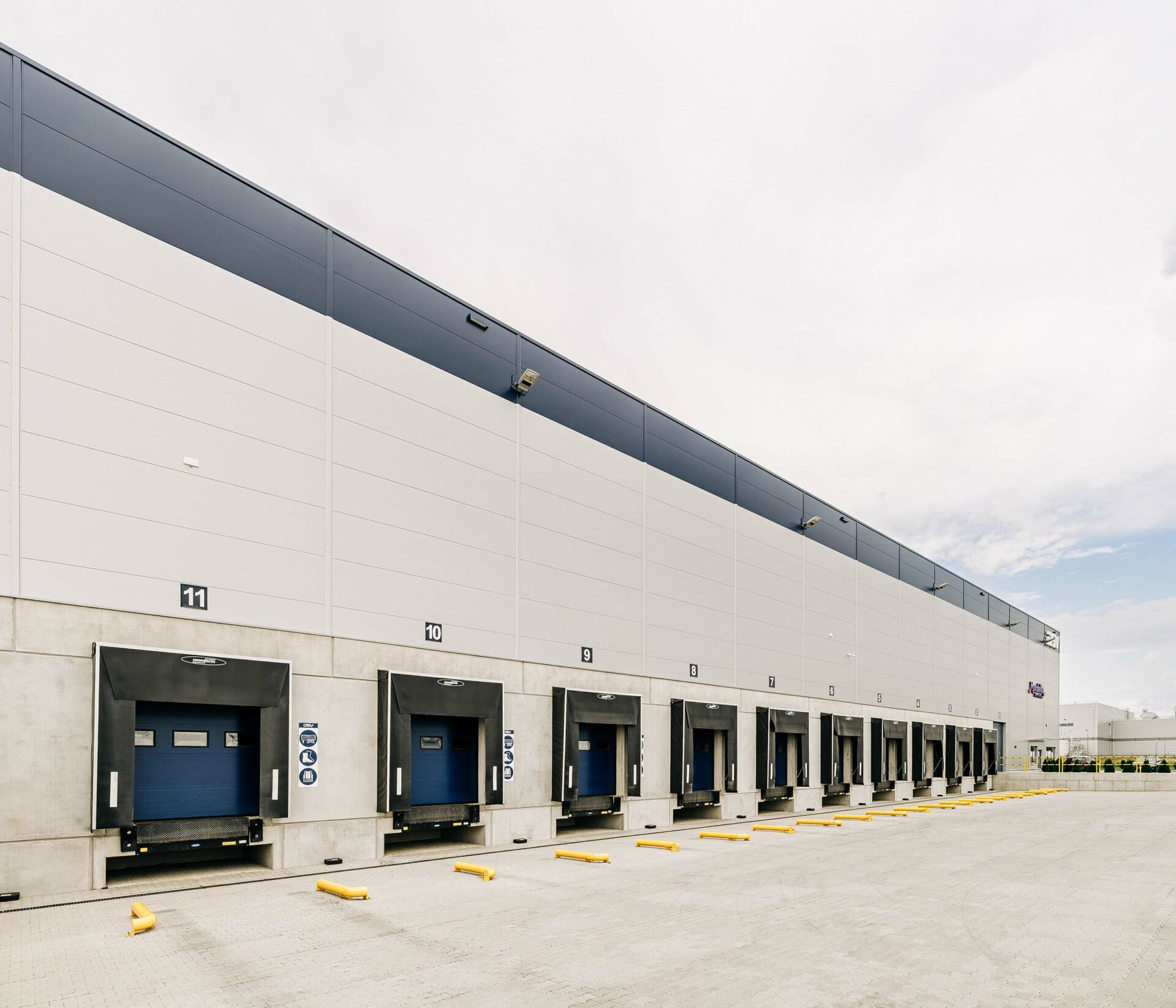
Almost all steel halls and large-scale industrial buildings used in industry and logistics are provided with loading docks. They are used for fast and safe loading of goods, parts, building materials or other products. The construction of loading docks must be included in the design of the facility. Check out what you need to know about the loading docks provided in industrial halls!
Loading dock – construction
Modern logistics halls have separate areas for the smooth circulation of goods. We refer to the loading bay as the dock. It is used for receiving and unloading incoming goods and loading the outgoing goods dispatched from the hall.
Loading docks must be optimally connected with the rest of the storage area. It is extremely important to properly plan the space layout. In terms of construction, the loading dock consists of 5 main components:
- Dock ramp – a place intended for parking lorries, which may optionally be specially separated and isolated with barriers; the ramp on the lock side should be equipped with rubber bumpers to protect the delivery truck from damage,
- Industrial door – a key structure fitted in an opening of a steel hall, securely closed when the dock is not in use.
- Sealing sluice – also referred to as “apron”, intended to seal off the loading area from the surrounding environmental conditions. With the sluice, the goods can be handled safely without getting damaged or wet.
- Hydraulic ramp – the central loading point, surrounded by a lock, with adjustable height and extension; the ramp assists in handling sensitive and bulky goods by bridging the height difference between the height of the warehouse and the vehicle loading area.
- Wheel guides – useful aids that promote an even, perpendicular positioning of the delivery vehicle in relation to the dock; visually, these are usually steel barriers painted with warning colours (yellow-black).
Types of loading docks
Loading docks must be strictly tailored to the purpose of the building. When designing a hall equipped with docks, the type of vehicles that will deliver and remove goods is also taken into consideration. In general terms, we can distinguish the following types of loading docks according to their purpose:
- general use,
- refrigerated,
- with inflatable apron for couriers,
- for double-decker vehicles.
In addition to that, the docks can be of open or closed design. The latter will be more costly to build, but such a structure is ideal for halls where it is very important to maintain constant temperature. In terms of location in relation to the main structure, we distinguish the parallel (standard) and saw-tooth (stepped) docks, which are used less frequently, mainly when there is insufficient manoeuvring space.
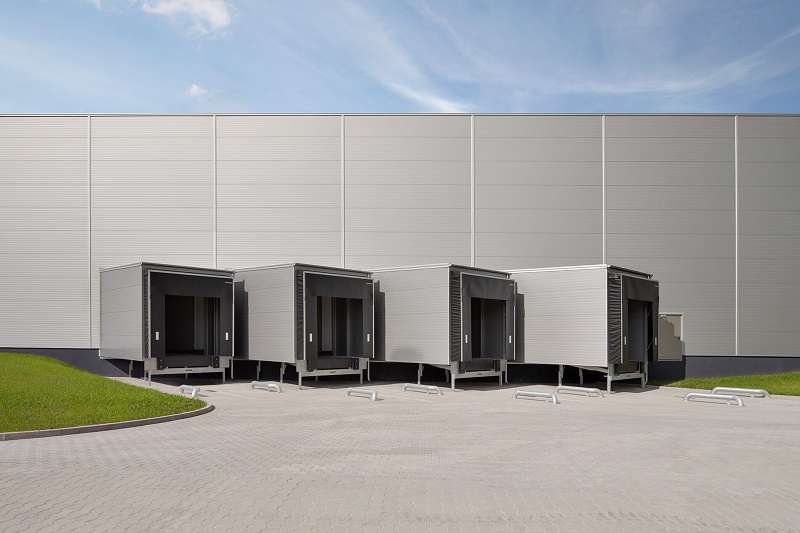
Loading docks – dimensions
Loading docks can have different dimensions, and this aspect should be discussed in detail with the investor when planning the construction of a logistics hall. The basic criterion for the selection of dock sizes is the type of delivery vehicles used. If a company uses or intends to use different types of trucks, then the dimensions of the widest and the tallest model should be taken into account. It is assumed that the width of the dock should not be less than 2.5 metres. However, this distance applies to a perfectly positioned vehicle, i.e. a situation in which the walls of the vehicle are perfectly aligned with the airlock walls. In practice, despite the best efforts, exact positioning of the vehicle is difficult, so a “spare” width should be included, which should be about 20% of the base width. In the example above, the final dimensions of the loading dock in terms of width would then be 3 metres.
loading docks
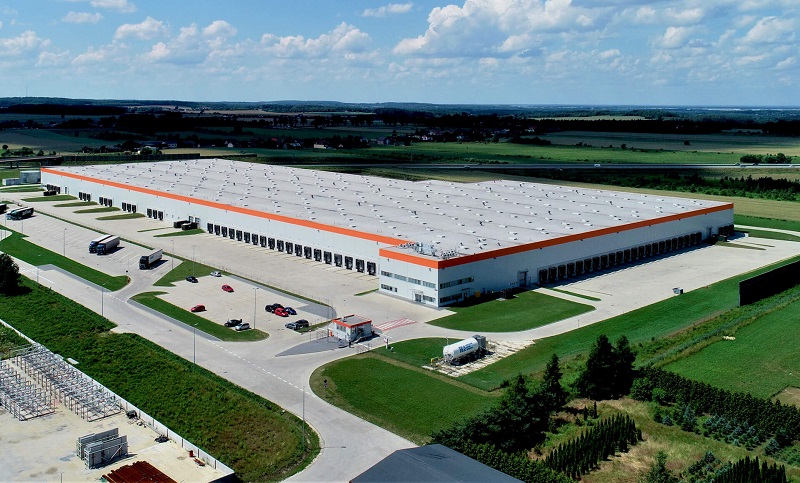
The height of the dock, or rather the door lintel, must be matched to the highest point of the transport vehicles used. As a rule, the height of the top wall will never be more than 4 metres. This parameter is always relative to the manoeuvring yard surface. In this case, it is also worth adding a “spare” 5%-10% of the base height.
Loading docks – loading ramp load capacity parameters
Another important aspect when building storage halls with loading docks is to determine the load-bearing capacity of the loading ramps. The load capacity expresses the load on the ramp. The maximum load-bearing capacity for a given structure depends on the nature and use of the ramp. In determining this value, account is taken not only of the approximate weight of the goods being handled, but also of the forklift trucks, operators and any tools used. Underestimating the load capacity of the ramp at the design stage may result in an accident during the hall use. According to EN 1398, the load-bearing capacity is determined for a wheel contact area of 100 x 150 mm. However, the correct determination of the final load-bearing parameter rests with the architect, who must know the exact requirements of the client.
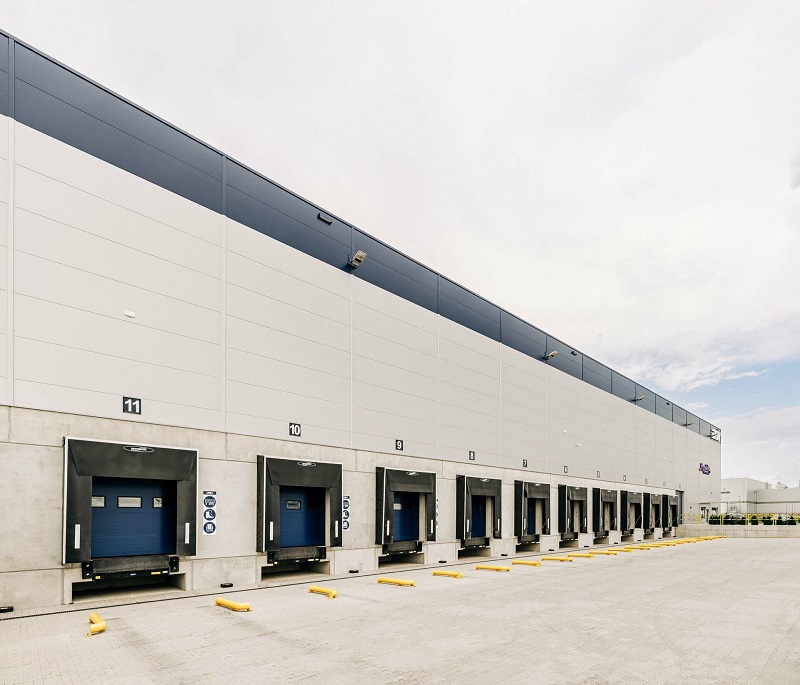
When are loading docks used?
Goods and materials need to be loaded and handled in practically every type of warehouse and production facility. In general industrial contracting, we recognise the very high demand for docks in many industries. A loading dock should be found in every shipping and logistics hall. Manufacturing plants producing medium and large sized products should also be equipped with appropriate handling stations. In other words, this solution is used wherever manual handling of large products would be either impossible or too difficult, time-consuming and capital-intensive. It should also be noted that the functionality and design of the loading dock significantly reduces the working time.
Read also the article: Warehouse with office – overview of solutions