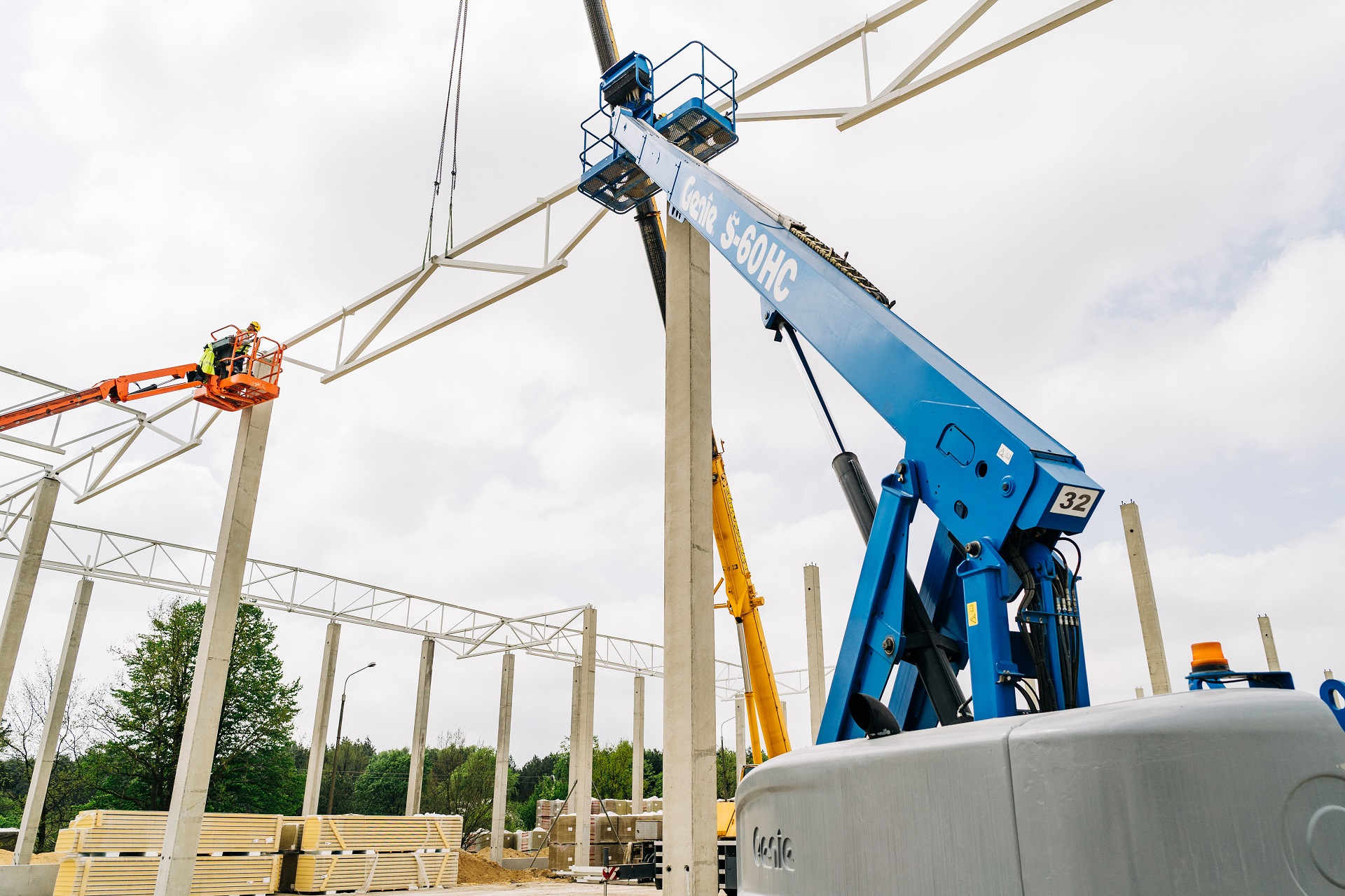
Production and assembly of steel structures
Manufacturing steel structures is a precise and time-consuming process. For a professional contractor, installation of a structure that is well made and delivered on time is a pleasure. Both of these processes consist of several stages that lead to a steel-framed building. A modern steel production plant operates on the basis of procedures and instructions approved by certificates (Factory Production Control in accordance with PN-EN 1090) and production management standards (Quality Management System in accordance with PN-EN ISO 9001). The first stage in the manufacture of steel structures is preparing an order execution plan. It is drawn up on the basis of technical documentation, quality assurance plans and product inspection and testing plans. For each task, a detailed production technology and work schedule is prepared and the material from which the structural elements of the steel hall will be built is ordered. Workshop design provides the contractor with the details on the structure class, surface treatment of the steel structure, corrosion and fire protection methods, the requirements for welds or the method of making openings. The workshop design is based on the technical design. It also contains full lists of the materials and fasteners needed.
The manufacturer of steel halls should only use materials which meet the requirements of European standards and regulations. Each time, the structure manufacturer verifies the steel supplier and material compliance with the detailed design already at the technology preparation stage. After receiving the material, an experienced steel hall contractor segregates it according to profile type, sheet thickness or size and class of connectors. At present, steel prices and availability fluctuate very rapidly, so it is important to order all the material you need at once. Once the steel components have been moved from the storage yard to the production hall, they undergo a pre-treatment to remove residues of the metallurgical processes and corrosion deposits, which would hamper the welding. The cleaned material is subjected to thermal and mechanical treatment. These activities include cutting of bars and hollow sections on automatic band saws. Plates are cut from sheets with gas or laser cutting technology with numerically controlled burners. Thin sheets up to 15 mm thick are cut with PC-controlled plasma cutter. Appropriately cut and prepared for welding, the steel hall components are moved to welding stations.
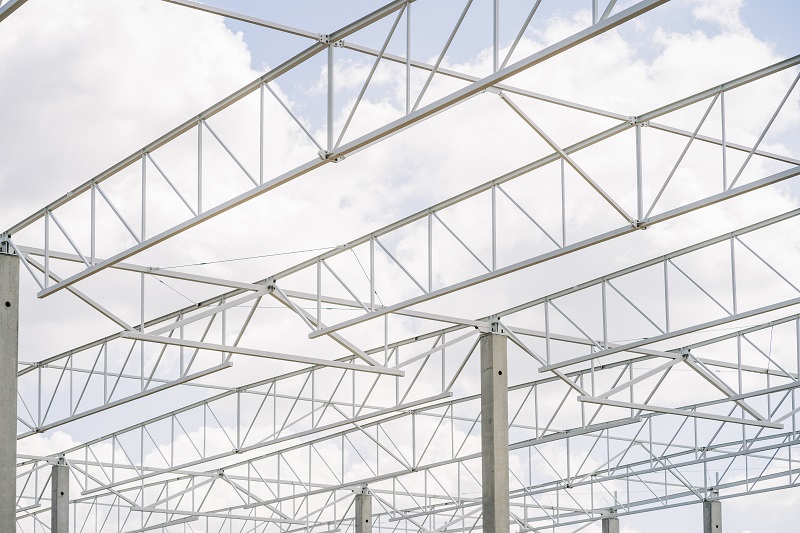
The steel hall contractor should only employ experienced and qualified workers with the relevant qualifications. Welding is one of the most important stages in the construction of steel structures. There are many methods for welding and sealing materials. Depending on the materials used, the covered electrode, submerged arc and gas shielded arc welding technologies are applied. Energy-efficient, automated, PC-controlled welding equipment is used in these processes. The manufacture and erection of steel structures are processes that require continuous quality control of workmanship and testing, proven by certificates and approvals mentioned above. The quality of the manufactured element is ensured by the relevant manufacturer’s department that is appropriately trained and provided with the latest equipment. Compliance with the technical documentation and the applicable standards is checked in terms of materials used, dimensions, welds, holes and anti-corrosion protection. Non-destructive testing of welds is a particularly important stage of quality control. Stringent tests allow defects to be eliminated and failures to be prevented. One of the last stages of production is corrosion protection of the manufactured element. Before applying protective coatings, it is important to thoroughly clean and degrease the surface of the component. During the painting process, it is important to monitor the temperature and humidity of the air in the paint shop. Measurements of component roughness and coating thickness are the basis for verifying the quality of this type of protection. The final stage in the manufacture of a steel structure is the preparation of as-built documentation and issuing a declaration of conformity of workmanship.
Steel structure assembly
Of course, the design for the erection of the steelwork must be prepared before the assembly of the structural elements begins. It includes the necessary permits and approvals (building permits, correct health and safety conditions for workers), a site preparation project and the ultimate method of joining the structural elements.
Steel halls and structures are erected using several basic erection methods:
- assembly of single components,
- block assembly,
- slide-on assembly,
- downstream assembly.
The first two methods are used for production and storage halls. In the single element method, the main columns are erected first and then positioned and levelled by surveying methods. Wall transoms and wall bracing components are then assembled to provide stability to the columns. At a later stage, roof rafters, trusses, roof purlins and slope braces are bolted to the columns. The whole is the framework of the structure. Block erection refers to the method of joining individual elements into larger structural assemblies prior to lifting (e.g. bolting roof rafters together with purlins at ground level, then lifting the entire assembly and installing it on the hall columns).
Assembly of steel structures is carried out on against assembly drawings included in the construction design. They show the exact location of individual elements, the foundation levels of the columns, the height ordinates of the load-bearing beams and the size, length and class of the bolts that should be used to join the elements. For preloaded connections, the designer should determine the bolt torque to be applied using a torque spanner.
The final stage in the assembly of the steel structure is the assembly of the cladding, which gives the building the appropriate aesthetic and thermal insulation properties.
Steel structure erection contractors
Steel halls and steel structures cannot be built without contractors specialising in the assembly of such structures. Steel structure erection contractors must have experienced staff who are constantly improving their skills through courses and training. New equipment, devices and joining methods are introduced every year. In addition to skilled workers, steel erection companies need suitable, reliable construction equipment such as:
- mobile platforms, telescopic handlers with variable reach,
- lifts and cranes,
- welding and sealing machines,
- metal saws,
- magnetic drilling machines,
- other hand-held assembly tools.
COMMERCECON, as a company recognised in the national and international market, offers quality designs of industrial halls or warehouses as well as installation of steel structures, based on skilled workers and the latest assembly tools and machinery.
Health and safety in the steel structure assembly
Assembly work entails risks for those actively involved in the process, but also for those in the vicinity of the site. Therefore, health and safety on the construction site and during assembly work is particularly important. These rules are included in the Health and Safety Plan (H&S Plan).
The main aspects to be considered during installation:
- all workers must have the required health certificates (including authorisation to work at heights) and be trained on health and safety,
- it is advisable to combine elements in as large an assembly as possible on the storage yard to minimise the risk of people, elements or tools falling,
- tools and other equipment must be in working order as evidenced by appropriate certificates,
- a test lift of 0.5 m must be done before lifting the component,
- it is forbidden to lift items whose weight exceeds the permissible nominal load,
- construction components may only be released from the lift after they have been firmly fixed in their final location,
- it is forbidden to carry out assembly work above the place where other teams are working,
- it is forbidden to carry out installation at wind speeds exceeding 10 m/s,
- it is not permitted to carry structural elements over people or driver’s cabs,
- it is prohibited to leave the element on a sling during breaks or after completion of the work.